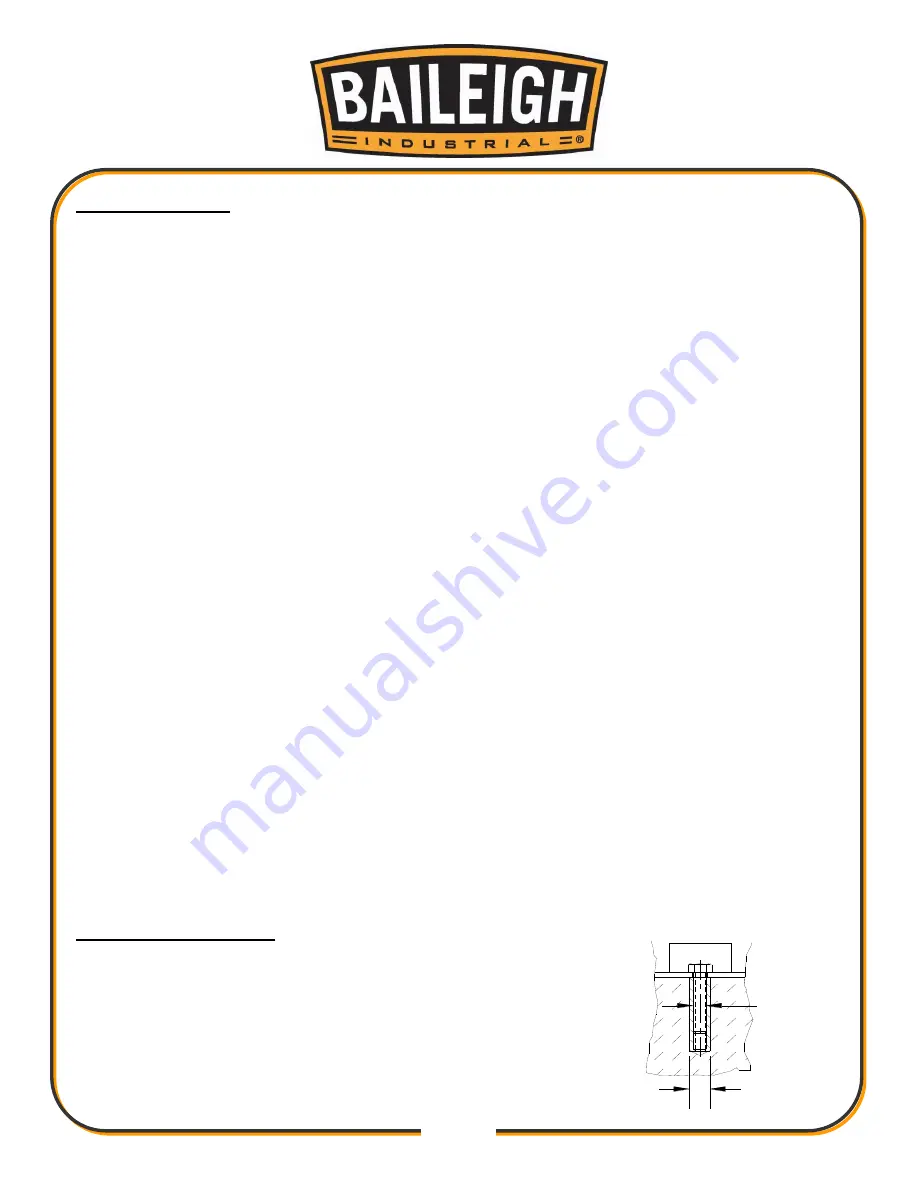
12
12
INSTALLATION
IMPORTANT:
Consider the following when looking for a suitable location to place the machine:
•
Overall weight of the machine.
•
Weight of material being processed.
•
Sizes of material to be processed through the machine.
•
Space needed for auxiliary stands, work tables, or other machinery.
•
Clearance from walls and other obstacles.
•
Maintain an adequate working area around the machine for safety.
•
Have the work area well illuminated with proper lighting.
•
Keep the floor free of oil and make sure it is not slippery.
•
Remove scrap and waste materials regularly, and make sure the work area is free from
obstructing objects.
•
If long lengths of material are to be fed into the machine, make sure that they will not extend
into any aisles.
•
LEVELING:
The machine should be sited on a level, concrete floor. Provisions for securing it
should be in position prior to placing the machine. The accuracy of any machine depends on
the precise placement of it to the mounting surface.
•
FLOOR:
This machine distributes a large amount of weight over a small area. Make certain
that the floor is capable of supporting the weight of the machine, work stock, and the
operator. The floor should also be a level surface. If the unit wobbles or rocks once in place,
be sure to eliminate by using shims.
•
WORKING CLEARANCES:
Take into consideration the size of the material to be
processed. Make sure that you allow enough space for you to operate the machine freely.
•
POWER SUPPLY PLACEMENT:
The power supply should be located close enough to the
machine so that the power cord is not in an area where it would cause a tripping hazard. Be
sure to observe all electrical codes if installing new circuits and/or outlets.
Anchoring the Machine
•
Once positioned, anchor the machine to the floor, as shown in
the diagram. Use bolts and expansion plugs or sunken tie rods
that connect through and are sized for the holes in the base of
the stand.
•
This machine requires a solid floor such as concrete at a
minimum of 4” (102mm) thick. 6” (153mm) minimum is preferred.
.31"
(7.87mm)
.50"
(12.7mm)
Содержание AS-350M
Страница 15: ...13 13 OVERALL DIMENSIONS...
Страница 16: ...14 14 GETTING TO KNOW YOUR MACHINE B G A I H L C E D F M K J...
Страница 29: ...27 27 ELECTRICAL SCHEMATIC...
Страница 30: ...28 28 PARTS DIAGRAM...
Страница 35: ...33 33 NOTES...