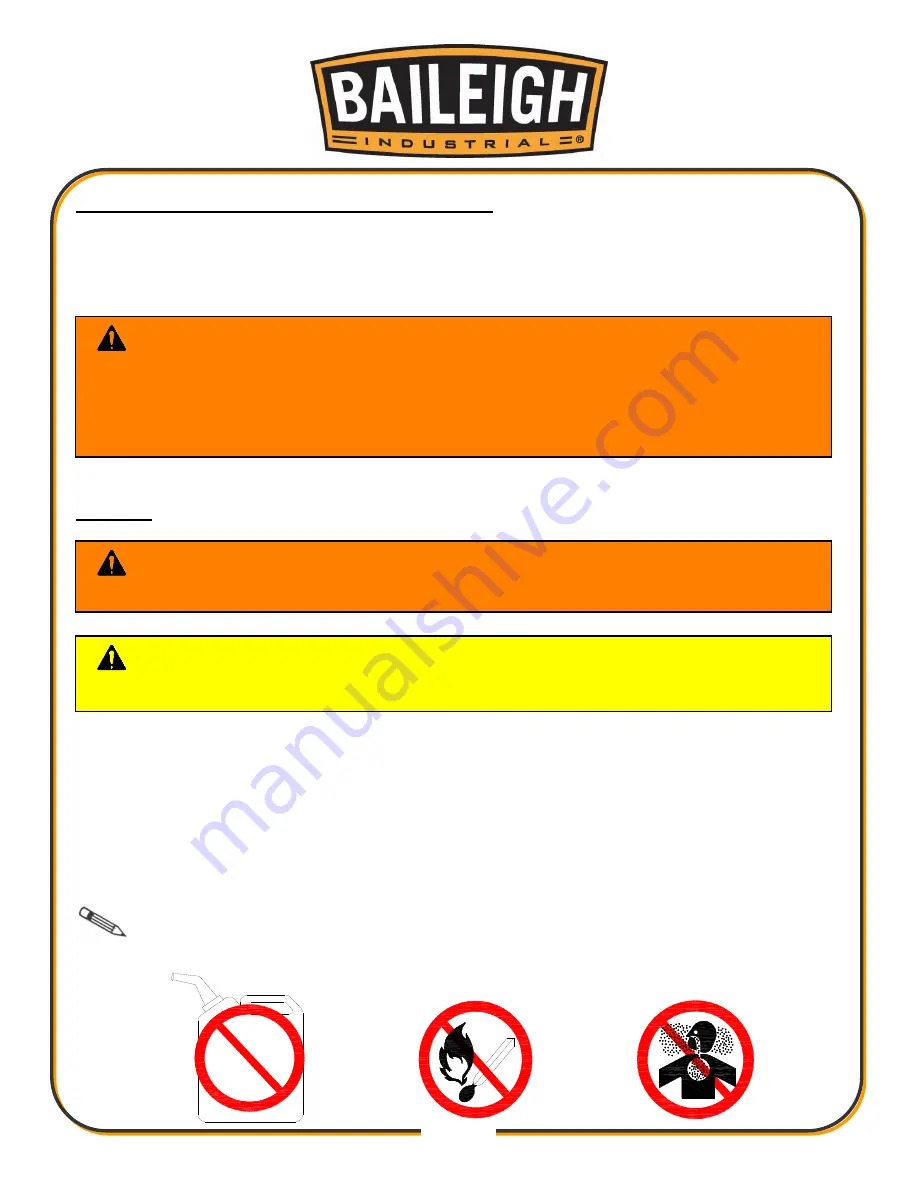
10
10
UNPACKING AND CHECKING CONTENTS
Your Baileigh machine is shipped complete. Separate all parts from the packing material and
check each item carefully. Make certain all items are accounted for before discarding any
packing material.
Cleaning
Your machine may be shipped with a rustproof waxy coating and/or grease on the exposed
unpainted metal surfaces. Fully and completely remove this protective coating using a
degreaser or solvent cleaner. Moving items will need to be moved along their travel path to
allow for cleaning the entire surface. For a more thorough cleaning, some parts will occasionally
have to be removed.
DO NOT USE
acetone or brake cleaner as they may damage painted
surfaces.
Fol
low manufacturer’s label instructions when using any type of cleaning product. After cleaning,
wipe unpainted metal surfaces with a light coating of quality oil or grease for protection.
Important: This waxy coating is NOT a lubricant and will cause the machine to
stick and lose performance as the coating continues to dry.
WARNING:
SUFFOCATION HAZARD! Immediately discard any plastic
bags and packing materials to eliminate choking and suffocation hazards to children
and animals.
If any parts are missing, DO NOT place the machine into service until the missing
parts are obtained and installed correctly.
WARNING:
DO NOT USE gasoline or other petroleum products to clean
the machine. They have low flash points and can explode or cause fire.
CAUTION:
When using cleaning solvents work in a well-ventilated area.
Many cleaning solvents are toxic if inhaled.
GAS
Содержание BS-350SA
Страница 17: ...14 14 OVERALL DIMENSIONS...
Страница 18: ...15 15 GETTING TO KNOW YOUR MACHINE I H G F E D C B A T P O Q S M N U L R V J K T...
Страница 36: ...33 33...
Страница 49: ...46 46 ELECTRICAL SCHEMATIC...
Страница 58: ...55 55 NOTES...
Страница 59: ...56 56 NOTES...