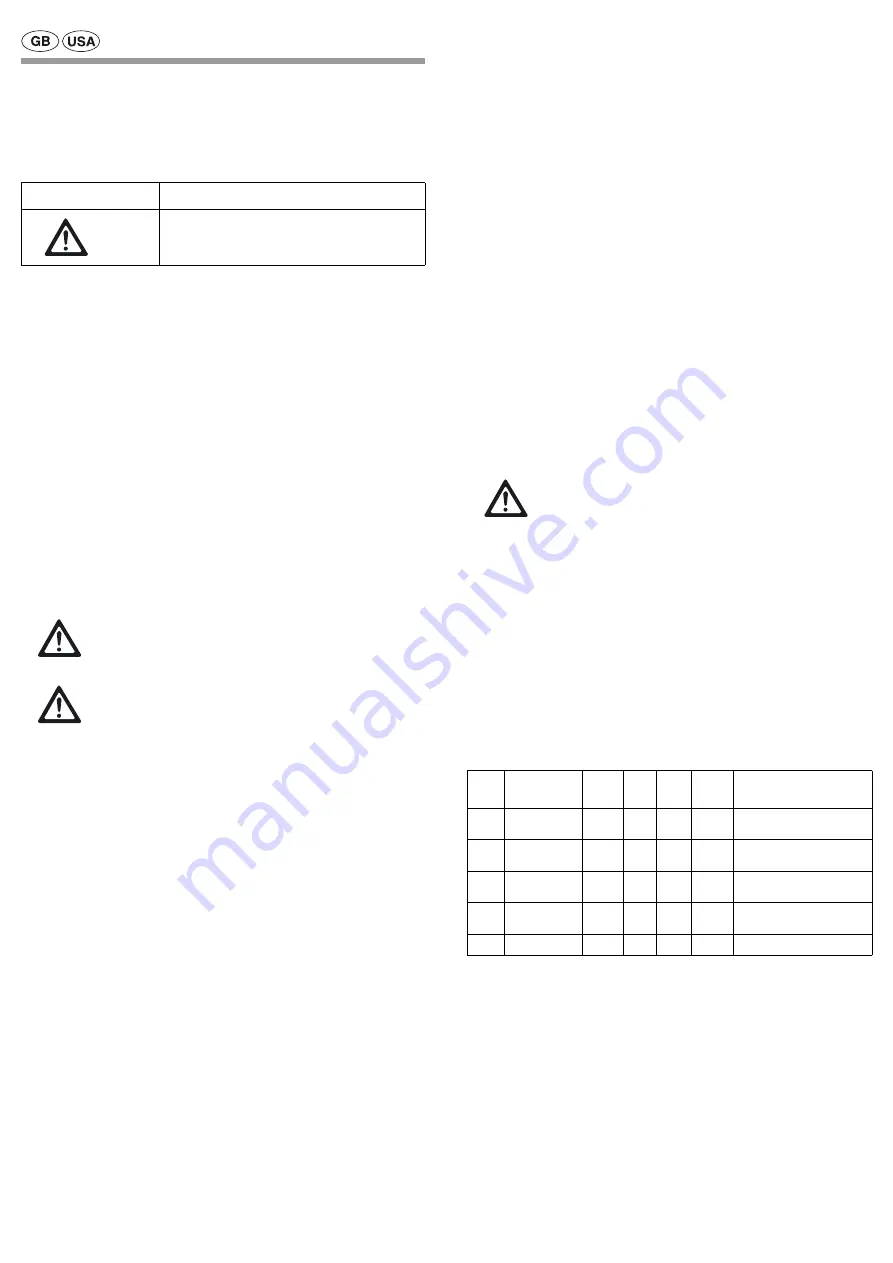
Micro-instruments
Legend
1
Locking button
2
Handle stems
3
Jaw part mounting (on handle)
4
Jaw parts with notched rod
Symbols on product and packages
Intended use
The micro-instruments are intended for use in neurosurgery, and are specially designed for use in tight spaces. They
can be used for cutting, grasping, dissecting, etc. of blood vessels and tissues.
Available sizes
The micro-instruments are available as complete instruments or as separate, combinable components. Various jaw
parts (e.g. straight scissors, curved scissors or forceps) can be used with the appropriate handles.
Note
The current product range is described in Aesculap brochure C 74511.
Safe handling and preparation
CAUTION
Federal law restricts this device to sale by or on order of a physician!
¾
Ensure that the product and its accessories are operated and used only by persons with the requisite training,
knowledge or experience.
¾
Read, follow and keep the instructions for use.
¾
Use the product only in accordance with its intended use, see Intended use.
¾
Remove the transport packaging and thoroughly clean the new product, either by hand or by a mechanical
process, prior to its initial sterilization.
¾
Store any new or unused products in a dry, clean and safe place.
¾
Prior to each use, inspect the product for: loose, bent, broken, cracked, worn, or fractured components.
¾
Do not use the product if it is damaged or defective. Set aside the product if it is damaged.
¾
Replace any damaged components immediately with original spare parts.
Safe operation
Disassembling
¾
Turn the locking button
1
by 180° so that it engages.
¾
Hold the handle stems
2
with one hand and the jaw parts with notched rod
4
with the other hand.
¾
Pull to separate the jaw part mounting
3
and the jaw parts with notched rod
4
.
¾
Turn the locking button
1
back to its original position.
Assembling
¾
Ensure that the link of the jaw parts with notched rod
4
and the groove of the jaw part mounting
3
are in align-
ment when the handle stems
2
are closed.
¾
Push the jaw part mounting
3
and jaw parts with notched rod
4
together until the notched rod engages with an
audible click.
¾
Function check: Press the handle stems
2
together, all the way to the stop.
Check that the jaw parts operate properly.
Validated processing procedure
Note
Adhere to national statutory regulations, international standards and guidelines, and local, clinical hygiene
instructions for sterile processing.
Note
Mechanical processing should be preferred over manual cleaning because of the better and more reliable cleaning
results of mechanical processing.
Note
Successful processing of this medical product can only be ensured if processing is performed through a validated
processing procedure. The user/processor is responsible for the validation.
Note
Up-to-date information on processing can be found on the Aesculap Extranet at www.aesculap-extra.net
General notes
To avoid unnecessary, excessive contamination of the complete instrument tray during operations, take care that
contaminated instruments are collected separately and not put back into the instrument tray.
Encrusted or fixated residues from surgery can make the cleaning process more difficult or ineffective, and can cause
corrosion of stainless steels. Therefore the time interval between application and cleaning should not exceed 6 h,
and neither potentially fixating pre-cleaning temperatures >45 °C nor any fixating disinfectants (active ingredient:
aldehyde, alcohol) be used.
Excessive doses of neutralizers or basic detergents can cause chemical degradation and/or fading and obliteration
of laser inscriptions on stainless steel surfaces, regarding visual reading and machine-readability of the inscriptions.
Residues containing chlorine or chlorides e.g. in surgical residues, medicines, saline solutions and in the service water
used for cleaning, disinfecting and sterilization will cause corrosion damage (pitting, stress corrosion) and result in
the destruction of stainless steel products. To remove such residues, the products must be rinsed sufficiently with
fully desalinated water and dried thoroughly.
Only use process chemicals that have been tested and approved (e.g. VAH/DGHM or FDA approval or CE mark) and
which are compatible with the product’s materials according to the chemical manufacturers’ recommendations. All
process parameters specified by the chemical’s manufacturer, such as temperatures, concentrations and exposure
times, must be strictly observed. Failure to do so can result in the following problems:
•
Optical deterioration, e.g. fading or discoloration of titanium or aluminum surfaces. For aluminum, pH >8 in the
application/process solution can already cause visible surface changes.
¾
Do not use process chemicals that would cause stress cracking or brittleness of plastics.
For further detailed advice on hygienically safe and material-/value-preserving reprocessing, see www.a-k-i.org
¾
Use suitable cleaning/disinfecting agents if the product is put away in wet condition. To prevent foam formation
and reduced effectiveness of the process chemicals: Prior to mechanical cleaning and disinfecting, rinse the
product thoroughly with running water.
Preparations at the place of use
¾
Disassemble the product immediately after use, as described in the respective instructions for use.
¾
Open jointed products.
¾
Rinse surfaces that cannot be visually inspected, e.g. on products with hidden gaps or lumens or products with
complex geometries, preferably with distilled water, using e.g. a disposable syringe.
¾
Remove visible surgical residues as completely as possible, using a lint-free wet wipe.
¾
Put the dry product into a closed disposal container and have it transferred to cleaning and disinfecting within
6 h.
Preparation prior to cleaning
¾
Disassemble the product prior to cleaning, see Disassembling.
Cleaning/Disinfecting
¾
Carry out ultrasound cleaning:
– as an effective mechanical supplement to manual cleaning/disinfecting.
– as a pre-cleaning procedure for products with encrusted residues, in preparation for mechanical cleaning/
disinfecting.
– as an integrated mechanical support measure for mechanical cleaning/disinfecting.
– for additional cleaning of products with residues left after mechanical cleaning/disinfecting.
¾
Clean and disinfect microsurgical products mechanically, provided they can be securely fixed in machines or
storage devices in such a way that they will be thoroughly cleaned.
Manual cleaning/disinfecting
¾
Keep working ends open during cleaning.
¾
Clean products with movable links with the links opened or mobilized.
¾
Inspect visible surfaces for residual contamination after manual cleaning/disinfecting.
¾
Repeat the cleaning process if necessary.
Manual cleaning with immersion disinfection
D–W:
Drinking water
FD–W:
Fully desalinated water (demineralized)
RT:
Room Temperature
Stage
I
¾
Fully immerse the product in the cleaning/disinfecting solution. Make certain that all accessible surfaces are
moistened.
¾
Clean the product under running tap water, using a suitable cleaning brush if necessary, until all visible residues
have been removed from the surfaces.
¾
Brush through surfaces not accessible to visual inspection, e.g. in products with hidden crevices, lumens or
complex geometries, for at least 1 min or until no more residues can be removed, using a suitable cleaning brush
(TA no. FM32800).
¾
Mobilize non-rigid components, e.g. set screws, links, etc. during cleaning.
¾
After cleaning, thoroughly (at least five times) rinse through these components with the cleaning/disinfecting
solution, using a disposable syringe (20 ml).
¾
Do not use metal cleaning brushes or other abrasives that would damage the product surfaces and could cause
corrosion.
Stage
II
¾
Rinse the product completely (all accessible surfaces) under running water.
¾
Allow water to drip off for a sufficient length of time.
Stage
III
¾
Fully immerse the product in the disinfecting solution. Make certain that all accessible surfaces are moistened.
Symbol
Explanation
Caution: General warning symbol
Caution: See documentation supplied with the product
WARNING
Risk of injury and/or malfunction!
¾
Always carry out a function check before using the product.
WARNING
Risk of injury when applying the product outside the field of view!
¾
Apply the product only under visual control.
CAUTION
Damage to the product due to inappropriate cleaning/disinfecting agents and/or
excessive temperatures!
¾
Use cleaning and disinfecting agents according to the manufacturer’s
instructions. The cleaning and disinfecting agents must
–
be approved e.g. for aluminum, plastic materials and high-grade steel,
–
not attack softeners (e.g. silicone).
¾
Observe specifications regarding concentration, temperature and exposure time.
¾
Do not exceed the maximum allowable cleaning temperature of 55 °C.
Stage
Step
T
[°C/°F]
t
[min]
Conc.
[%]
Water
quality
Chemical
I
Cleaning
RT
(cold)
15
2
D–W
BBraun Stabimed; aldehyde-free,
phenol-free and QAV-free
II
Intermediate
rinse
RT
(cold)
1
-
D–W
-
III
Disinfecting
RT
(cold)
15
2
D–W
BBraun Stabimed; aldehyde-free,
phenol-free and QAV-free
IV
Final rinse
RT
(cold)
1
-
FD–W
-
V
Drying
RT
-
-
-
-