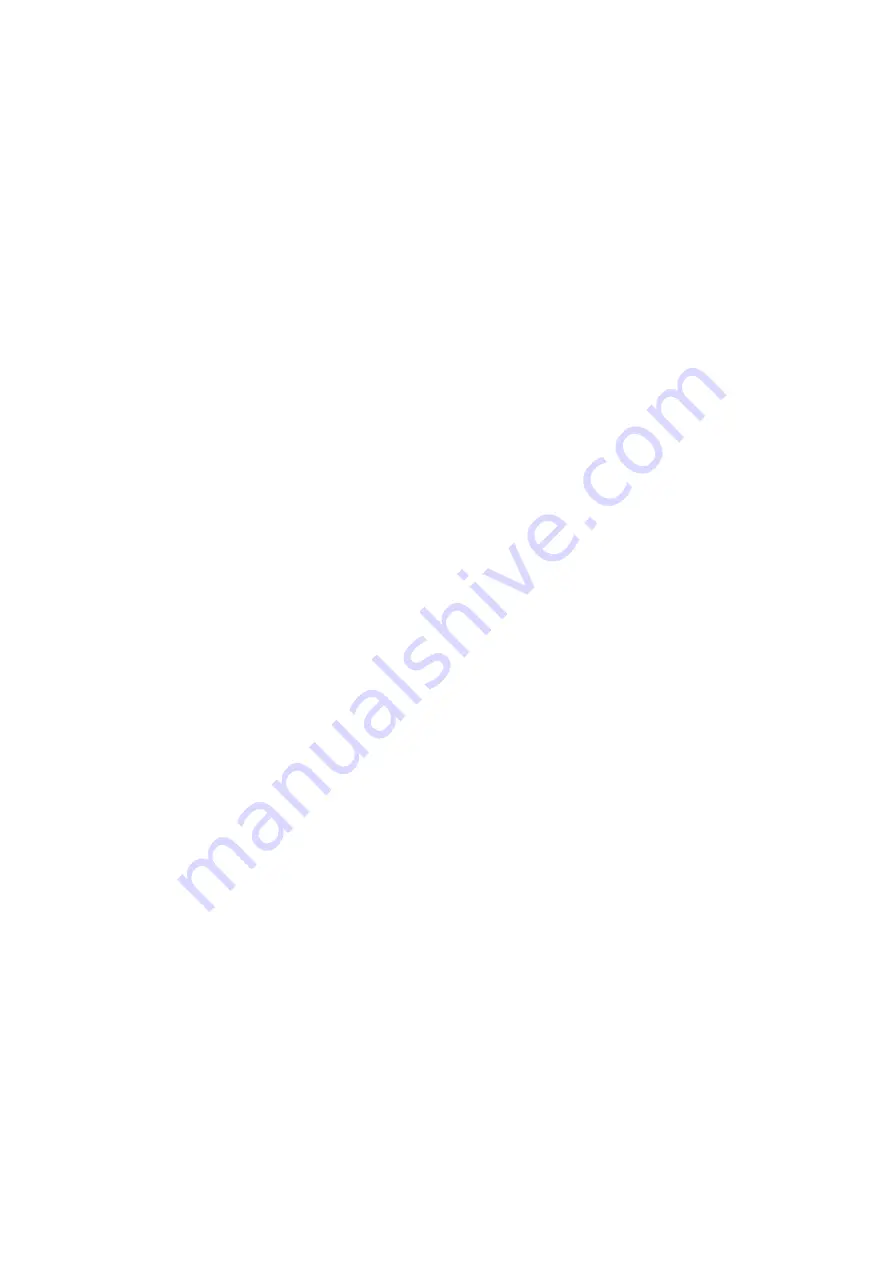
6-1
Chapter 6. Direct / Reverse Action type Conversion and
Spring range Change of Actuator
6-1. Direct / Reverse action change
As a general rule it is most recommendable to prepare separately the direct type and reverse
type of actuators and not to convert actuators into different types. However, when it has
become unavoidable to convert actuators into other types, conversions may be done by using
the parts mentioned below (Table 6-1 on page 6-2 and Table 6-2 on page 6-3). The parts
marked “+” are the ones which are newly needed and those marked “-” are ones which are not
used.
Содержание ACN Series
Страница 1: ...CM2 ACP100 2001 Control Valves Model ACP_ _ _ ACN_ _ _ User s Manual ...
Страница 18: ...1 4 ...
Страница 24: ...3 2 ...
Страница 44: ...4 20 ...
Страница 58: ...7 6 ...
Страница 62: ...8 4 ...
Страница 68: ...10 4 ...
Страница 90: ...12 14 ...
Страница 94: ...14 2 ...
Страница 95: ......
Страница 98: ......
Страница 100: ......