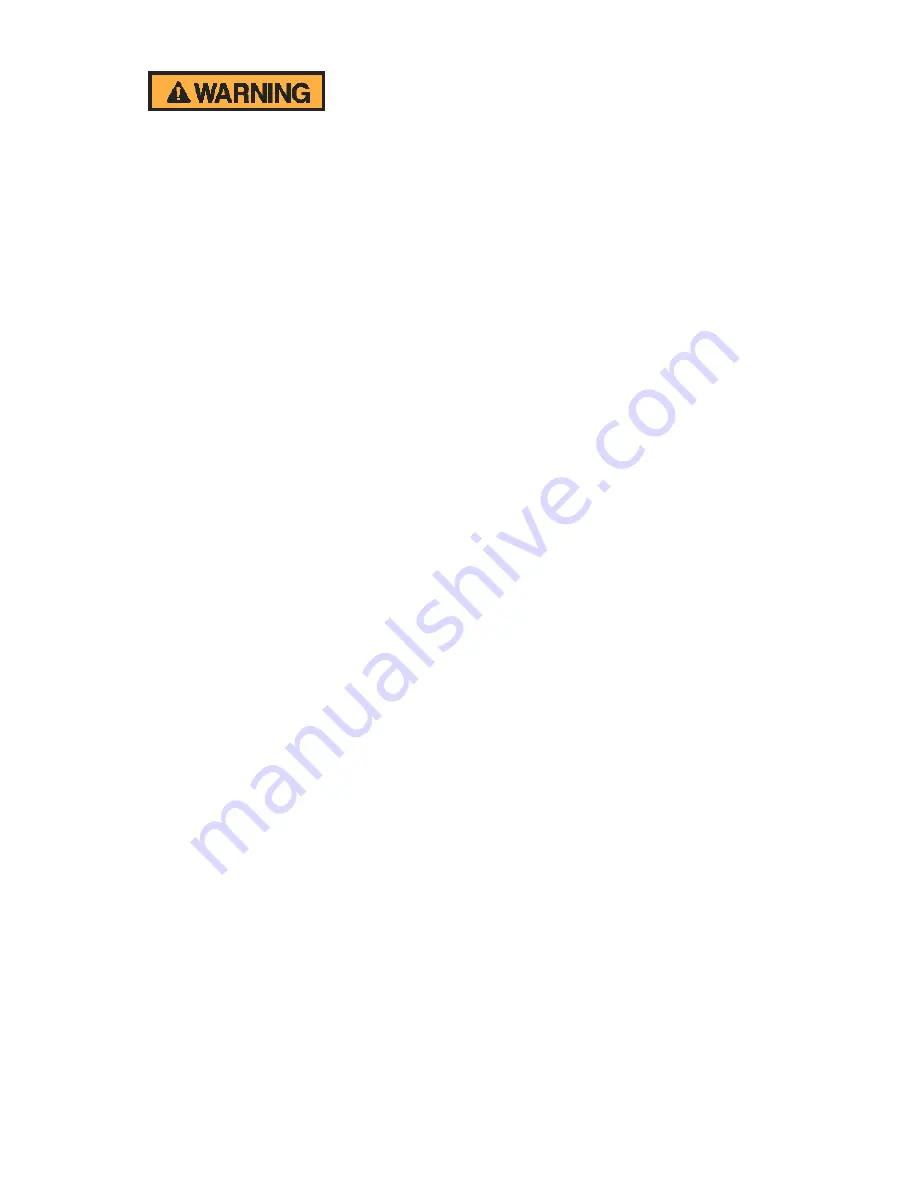
16
Valve, fitting, and/or hose rupture can cause serious injury or death. Do Not install or connect
any valves, fittings or hoses that are not rated for a minimum 150 psi operating pressure.
5.2 Pre-filter
Compressed air enters the system through the air inlet pre-filter (#4) (the maximum inlet
pressure should not exceed 150 psi). The pre-filter removes large particle contaminants and
moisture from the incoming air. The water and debris that is removed by the pre-filter can be
drained through the drain valve (#7) located at the bottom of the pre-filter. This ball valve should
be left slightly open anytime the system is in operation. This allows water to be drained as it is
filtered from the air. Leave the drain valve (#7) closed anytime the AirPrep System is not in use.
5.3 Aftercooler
Radiator
After passing through the pre-filter, the air enters the aftercooler (#8). The aftercooler is a large
fan cooled radiator that reduces the temperature of the compressed air which initiates moisture
condensation. The fan is powered by either an air motor or an optional electric motor (#9). Refer
to section 11.0 table 1 for the capacity of the aftercooler unit. The coil surfaces of the aftercooler
radiator must be kept clean to maintain performance (see Section 8.0).
5.4
Air Motor (radiator fan)
The air motor (#9) is a rotary type motor operated by compressed air. The expansion of the
operating air during normal operation creates a cooling effect. Therefore, the temperature of the
air motor will not exceed the higher of the surrounding atmosphere or the air input temperatures.
The vanes of the air motor take up their own wear and will last 5,000-15,000 hours depending
upon speed, method of oiling, operating pressure and the maintenance performed on the motor.
The operating air must be clean, oiled and should not exceed the specified pressure, therefore a
filter, air regulator and an automatic lubricator are installed in the air line upstream of the motor
(refer to Section 11.0, Table 2 for air motor specifications). Ball valve (#21) turns off the air
motor.
Note:
The air motor air supply must be clean, dry and lubricated to prevent motor failure.
5.5
Air Filter (fan air motor)
The compressed air supplied to the air motor passes through air filter (#22) to remove moisture
which could cause rust in the air motor and also could cause ice to form on the exhaust muffler
(#26). The water that is removed by the filter can be drained by opening the petcock valve at the
bottom of the air filter. This valve should be left slightly opened anytime the system is in
operation. This allows water to be drained as it is filtered from the air. Some models may be
equipped with filters having automatic drains.
5.6
Air Regulator (fan air motor)
The aftercooler fan speed can be controlled by changing the supply air pressure. The pressure is
adjusted by turning the knob of the air regulator (#23), clockwise to increase pressure/motor
speed and counter-clockwise to decrease pressure/motor speed. The air pressure is indicated by
the pressure gauge (#25) mounted on the regulator body.
Note:
The air motor pressure must not
exceed the specified maximum pressure (see Section 11.0, Table 2).
5.7
Automatic Air Lubricator (fan air motor)
After the air motor supply air passes the filter and regulator it is oiled by the automatic lubricator
(#24). The amount of lubrication needed is dependant upon the volume of air passing through
the motor. The lubricator should be adjusted to feed (1) one drop of oil for every 50-75 cfm of
air going through the motor (refer to Section 11.0, Table 2). The oil feed adjustment is made by
turning the knob at the top of the lubricator, clockwise to increase flow or counter-clockwise to
decrease flow. The lubricator reservoir can be drained if contaminants accumulate inside.