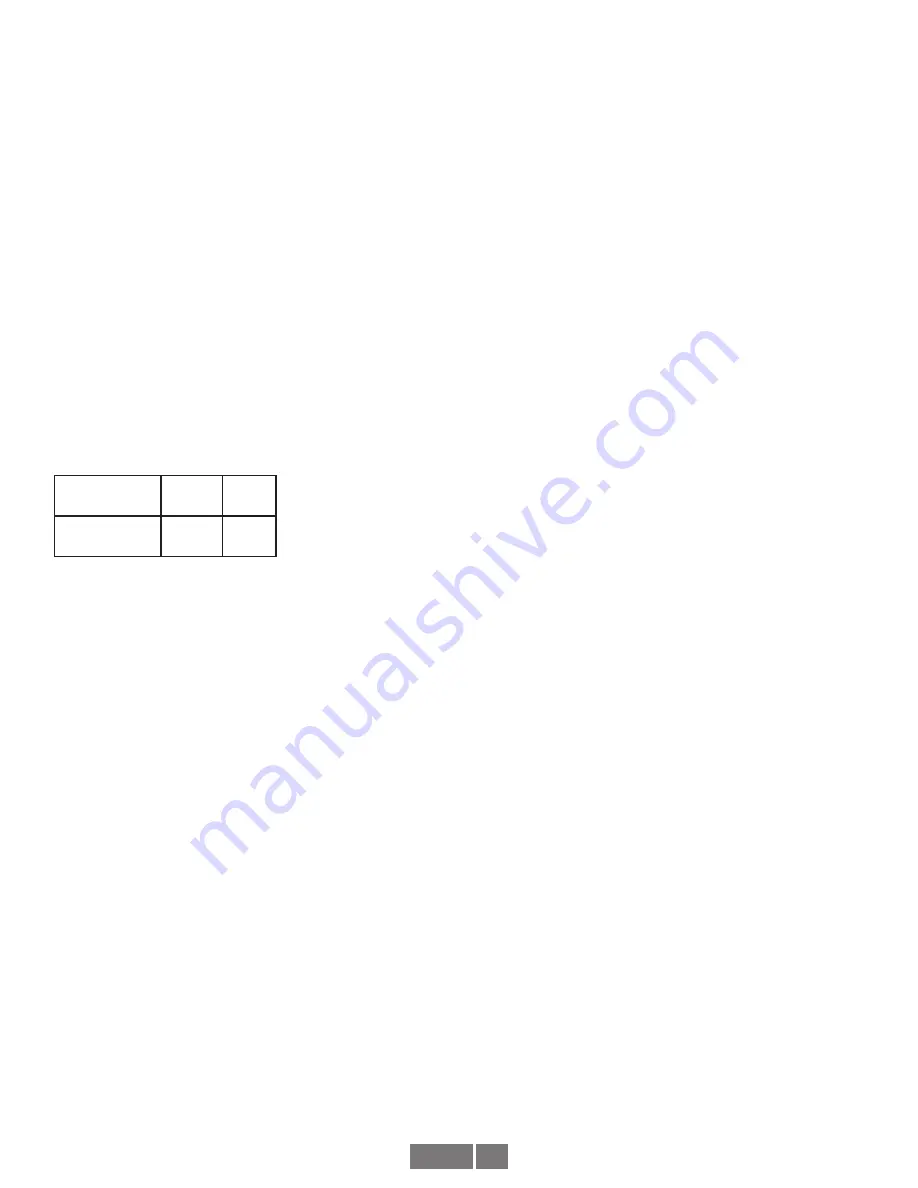
HS6A
9
Ethernet POWERLINK “K”
POWERLINK Ethernet is typically a master-slave network-the
master/scanner device gathers data from each (slave) device on the
bus. Avtron encoders are POWERLINK slave devices.
POWERLINK Ethernet may be wired in several different
configurations, but the best known is a “star” configuration where
each device has a “home-run” network cable that connects to a
central switch or hub.
To reduce the cabling requirements, Avtron encoders support
“Daisy-Chain” configurations. The master device must be at one
end of the bus. The signal is repeated by each encoder to it’s
output port (labelled “Hub”), which can in turn be connected to an
input port of another encoder. No external or switched termination
resistors are required for POWERLINK Ethernet. Power is carried to
the device via a separate set of wires. A maximum of (7) encoders
can be daisy-chained together to a single Ethernet master/scanner
or switch port.
Preferred cable: Nidec Avtron recommends structured Ethernet
wiring systems, available from a broad range of vendors as well as
Avtron.
For more details on POWERLINK, consult the POWERLINK
Standardization Group:
http://www.ethernet-POWERLINK.org
Number of
Nodes
1-7
Units
Max. Overall
Cable Length*
330
[100]
ft
[m]
*Using Ethernet standard cable, CAT6 or CAT5e required
NOTE: UNLIKE OTHER AVTRON ABSOLUTE ENCODERS, DO NOT
REMOVE THE CONNECTION CAP TO SET THE ADDRESS.
Setting Station/Node, Baud Rate
To set the node number: use the rotating switches on the back of
the connection cap. The format is hexidecimal, from 0x00 to 0xEF
(0-239 decimal). The left-most switch is the sixteen’s switch and
the right switch is the one’s).
Example: Left-most switch (16s set to 1, right most switch set to A.
Address = 0x1A = 1*16 + 10 *1 = 26 decimal
Setting the node number also sets the IP address.
Avtron POWERLINK encoders are located at 192.168.100.Node
For the example above, the IP address would be 192.168.100.26
The address may also be set via software using EPL telegrams. Set
the rotating switches to 0, 0 to enable software addressing.
POWERLINK baud rate is auto-detected by the encoder, no settings
are required. 100mBit and 10mBit are supported, Gigabit Ethernet is
not supported at the encoder level but may be utilized at the switch
backbone level.
Measuring Position, Speed, and Acceleration
To read position into your device (acceleration and speed
measurement is not supported.): Following the instructions for
your master/scanner module for the POWERLINK network, load the
encoder XDD file into your configuration. Assign it to the correct
node number. Store the configuration to the scanner module.
All of the position data and other parameters will be read by
the scanner module and placed in registers identified in the
configuration package.
For multiturn & single turn encoders: position data provided as
4 bytes, 32 bits: Format is little-endian (lowest bit = right-most
bit). Single-turn data/data within 1 turn is provided in the least-
significant bits. Multiturn data is provided directly “above” the
single turn data, bitwise. Example: 12 turns x 13 bits/turn encoder,
lowest 13 bits = position within one turn, next 12 bits (up to bit 25)
represent turns position data.
The position data is provided at parameter 0x6004.
Setting Zero Position for Multiturn Encoders and Single turn
Encoders:
Using XDD file permits setting of the Preset Value 0x6003 object
which will load a value in at powerup of the master system.
However, if the machine is not at the home/preset position at master
power-up, the system will nonetheless load the Initial Value into the
encoder. This can cause a position error.
Setting Direction of Rotation for Count Up/Down:
Object 0x6000, least significant bit (0) can be set to change
operation:
bit 0 = 0, Counterclockwise rotation = count up
bit 0 = 1, Clockwise rotation = count up
(rotation as viewed from the back of the encoder)
Scaling Counts:
To use scaling, set bit 2 in object 0x6000 = 1, default value = 0
0x6001 supports scaling of user units per revolution,
default value 0x2000
0x6002 enables setting of the total measuring range in user units
default value 0x1000
Multiplexed Mode
Multiplexed mode is supported by Avtron encoders. Multiplexing
slows the data feed from each encoder to enable other data to pass
more quickly to the master/scanner module.
For maximum encoder updates per second in mission critical
applications, turn Multiplexed mode off using the master/scanner
configuration software.
Other Parameters
Contact Nidec Avtron for additional parameters, diagnostic registers,
cam and programmable limit switch functionality and other
advanced features.
POWERLINK TROUBLESHOOTING
Viewing on oscilliscope: for POWERLINK/Ethernet, the transmit and
receive signal pairs should change state rapidly as the controller
transmits messages to the encoder and the encoder replies.
Transmission rates vary, but these messages can be extremely short
and typically require scope triggering to spot them.
A software “snoop” or “sniffer” program can also be used to packet-
analyze the communication. However due the the extremely high
speed of Ethernet communication, and the time-stamped nature
of the information on POWERLINK, it may be necessary to use a
hardware tool such as the B&R debugger/analyzer.
Ensure there are no more than (7) POWERLINK encoders connected
via daisy-chain to a single connection to a switch or bus master
device. Note this number is decreased for any hubs between the
master/scanner device and the encoder daisy-chain. More than
7 daisy-chained hubs + encoders will violate the Ethernet hub
repeater rule and cause Ethernet errors and highly inconsistent data
loss.
If the position is changing as the encoder moves, but is reported
incorrectly, the Initial Value parameter may have been loaded into
the encoder at the wrong physical position of the machine. Drive the
machine to the home/preset position, and cycle power to see if the
position is correctly reloaded.