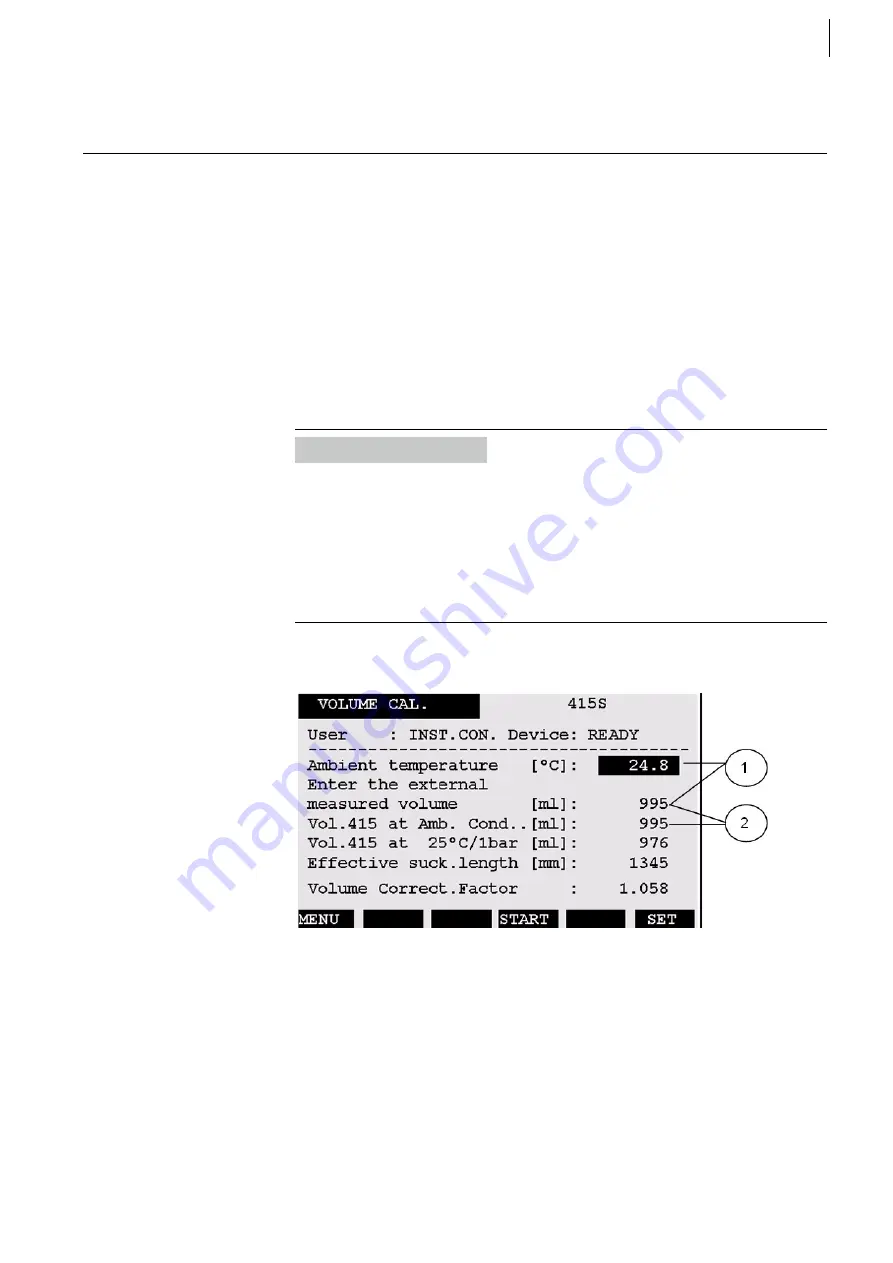
37
Checks
AVL 415SE Smoke Meter — Maintenance Guide
3 Checks
3.1
Sampling Volume Check
This function is used to compare the amount of the sampling volume with an
external measurement system.
This check can be performed:
with AVL 4210 Instrument Controller;
see
Sampling Volume Check with AVL 4210 Instrument Controller
via terminal;
see section
Sampling Volume Check via Terminal
via device user interface DUI;
see
AVL 415SE Smoke Meter Calibration, User’s Guide (material number
AT3803
).
3.1.1
Sampling Volume Check with AVL 4210 Instrument Controller
1.
Enter measurement values.
2.
Compare measurement values.
Information
In heated devices, the calibration should be carried out when the device is
heated. For this you need the Retrofit Kit (material number: BO3776).
Remark: this is a standard part of the AVL 408S Volume Tester, if delivered after
1. Jan 2000.
Measurement device and volume tester have to be operated at ambient pres-
sure which has to be parameterized.
This check shall be performed at stable thermal conditions, e.g. heated devices
should be heated completely with closed front door.
Fig. 32 Sampling volume check with AVL 4210