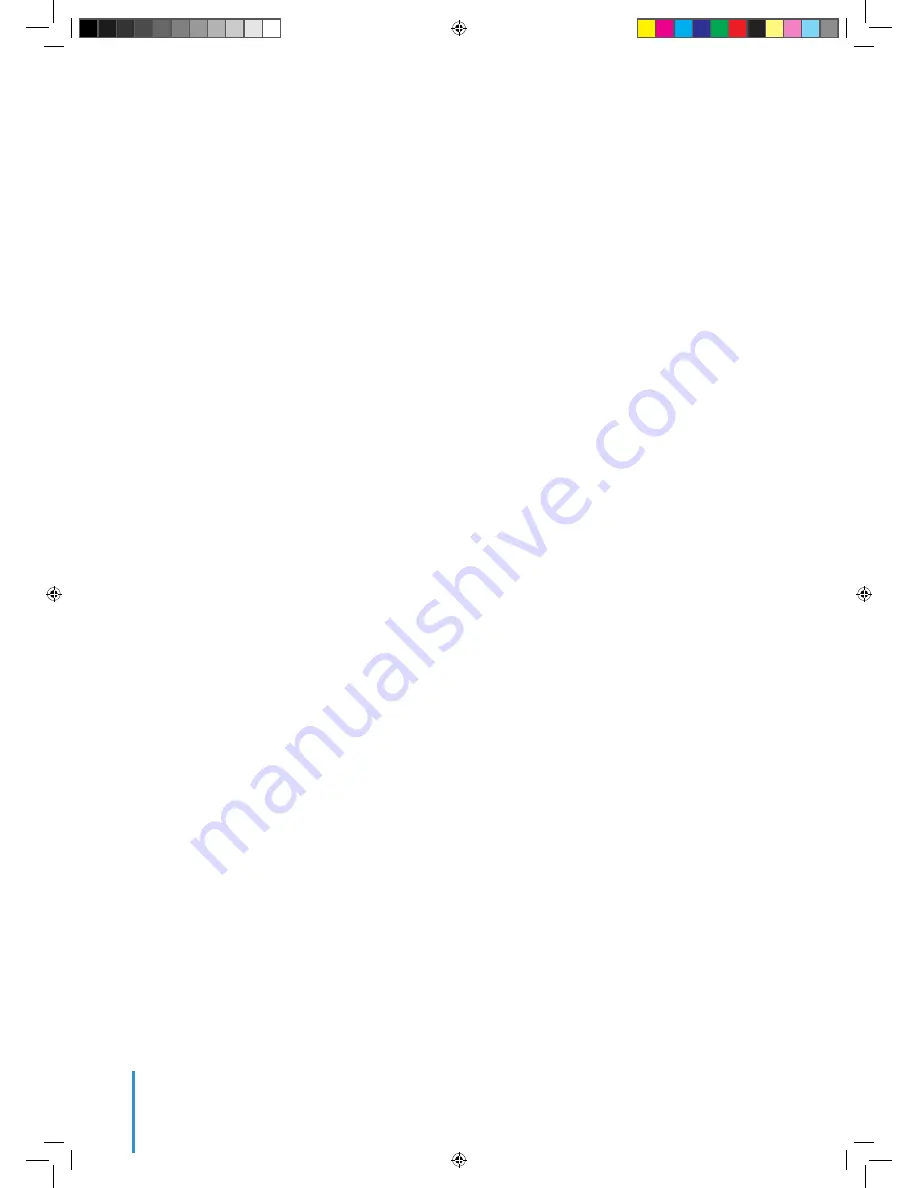
28
AVANTI Service Lift for Wind Turbines
Purpose
This instruction may be a substituting part of the Daily Lift
Checking to be used by authorized users and Certified
technicians. The information describes an alternative way
of how to check the over speed triggering and arresting
function in the Avanti Safety Fall Arrest Device model
ASL. Second, the test also documents that the Safety
Brake maintains its grip on the Safety Wire after
engagement. This testing we name the “Stomp-test”.
This stomp-test-method may replace the given daily
obligation in your manual explaining “to descend the lift,
manually engage the FAD (Fall Arrest Device), verification
by short no-powerdescent, unloading the FAD again by
ascending and observing centrifugal weight unit through
the window during lift use”. With the “Stomp-test” we
test the ability of the FAD to trigger in case of over speed
and arrest the load.
Tools:
None
Measurement Equipment:
None
Validity
It is applicable for testing the installed Safety Fall Arrest
Device (ASL) on-site. The test must only be performed by
trained users/Certified technicians and always with
respect of all the relevant safety regulations.
Cautions
Be aware that the instruction only explains the steps of
how to execute the “Stomp test” in the lift installation; it
doesn’t guide any safety precautions and the necessary
use of safety equipment.
Therefore, Avanti strongly recommends you to read and
understand what the physical work steps in the “Stomp-
test” are, and then execute your own Risk and Hazard
Assessment according to the valid safety working
procedures in your own organisation before starting the
test.
1. Test Preparation
The cabin (with 1 person inside) is ascended with a
service lift user inside, and the cabin bottom is
positioned (“parked”) in a height of app. 3 m/10 ft. above
the bottom landing floor platform.
2. Test Step
With the cabin in “parked” position app. 3 m/10 ft. above
the bottom landing floor, the user starts descending by
electrical power using the push down button. When the
cabin starts descending the user executes a hard stomp
with one foot in the cabin floor – The hard stomp is
executed by lifting one foot, so the lower leg is positioned
with a knee angle of 90 degrees – Then immediately after
the foot is stomped in the cabin floor -The user must
make sure to have a solid footing during the foot stomp!
The foot stomp should engage the ASL and arrest the
electrical descent of the cabin, the red light (if existing in
the control box) should turn “on” and the cabin load
should be hanging on the FAD/Safety Wire.
If the ASL doesn’t arrest at the first trial, then
re-establish the cabin in the position described in the
preparation part mentioned above and execute the
“Step” once again stomping a little harder.
3. Test Result
If the ASL activates properly after the stomp, the ASL will
now hold the cabin on the Safety Wire.
In order to ensure important maintaining grip by the
Safety Brake, the user then activates the manual descent
function and result shall be a Safety Fall Arrest Device
ASL holding the cabin fixed on the Safety Wire (manual
descending is not possible).
- If the activated ASL fixes the cabin on the Safety Wire
while manual descent is activated, the Safety Fall Arrest
Device (ASL) is in good and operational condition.
In order to release the activated ASL push the ascent
button up a little before releasing the ASL by the
unlocking handle.
-
If the ASL can´t activate after first or second “Stomp-
test”, or can´t fix the cabin in activated position
- User must immediately bring the cabin down and
park it at the bottom landing platform floor.
- Lock Out the installation from use and contact Avanti
for further approach!
- Document the execution of the above described
procedure in the Daily Inspection Log Appendix.
Any doubts regarding above instruction, please do not
hesitate to contact Avanti’s local representative for help.
- www.avanti-online.com
Appendix B: Stomp-test Instruction
Alternative way to inspect the ASL during Daily Inspection before Operation
AT00014348_Dolphin A-V164_User´s Manual E01R05.indd 28
10/24/2018 12:25:03 PM