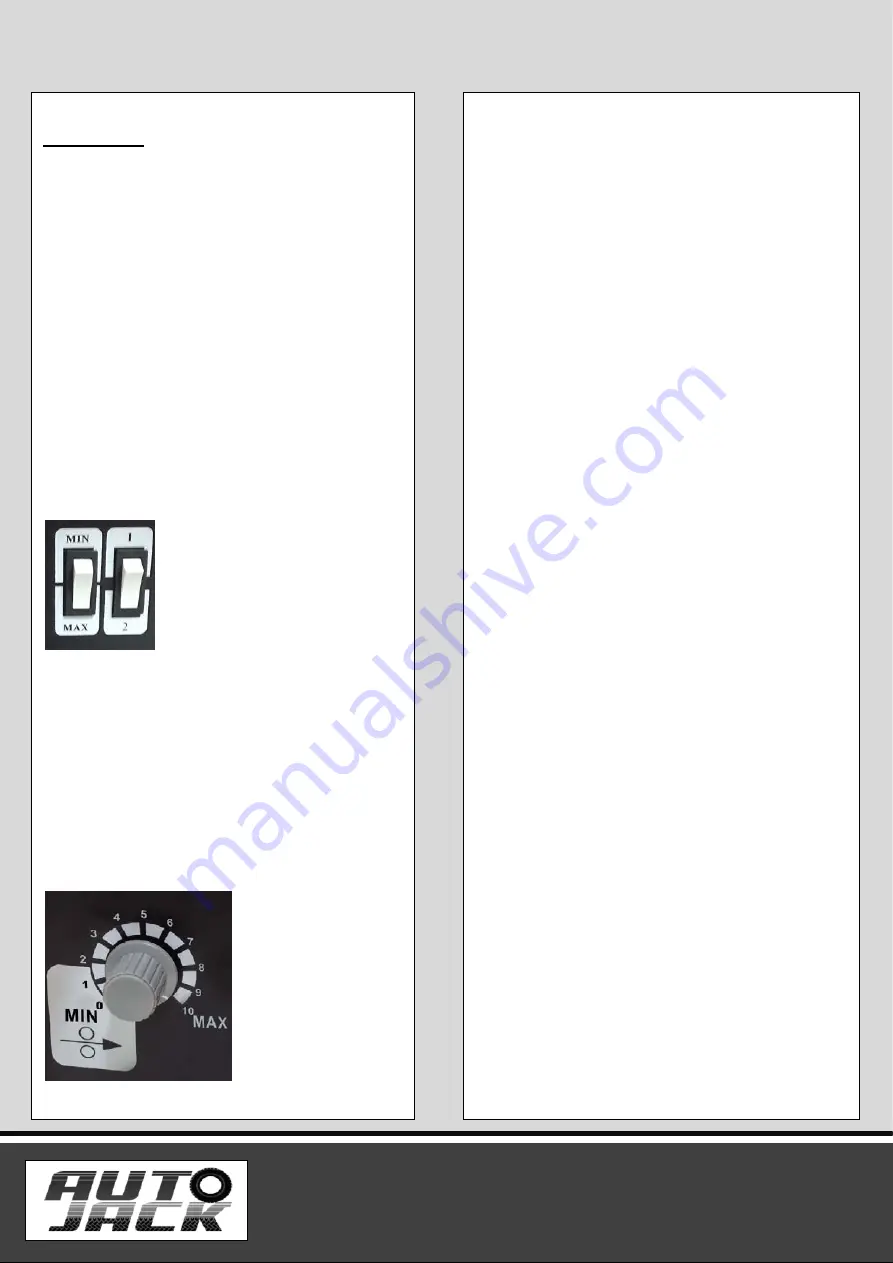
OPERATION
Operation
Before any work on the machine itself, remove
the mains plug from outlet.
Setting
Since the welding set must be set to suit the
specific application, we recommend that the
settings be made on the basis of a test weld.
Setting the welding current
-The welding current can be set to 2 different
levels using the welding current adjustment
switch (6). The required welding current
depends on the material thickness, the required
penetration depth and the welding wire
diameter.
Setting the wire feed speed
-The wire feed speed is automatically adjusted to
the current setting. The final wire feed speed
setting can be made on the welding wire speed
controller (5). It is advisable to start with the
medium setting and to re-adjust the speed as
necessary. The required quantity of wire
depends on the material thickness, the
penetration depth, the welding wire diameter
and also the size of the gap to be bridged
between the workpieces you wish to weld.
Electrical connection
-Before you connect the equipment to the mains
supply make sure that the data on the rating plate
are identical to the mains data.
-The equipment may only be operated from
properly earthed and fused shock-proof sockets.
Connecting the earth terminal
-Connect the welding set’s earth terminal (8) in
the immediate vicinity of the welding position if
possible. Ensure that the contact point is bare
metal.
Welding
-When all the electrical connections for the power
supply and welding current circuit have been
made, you can proceed as follows:
-The workpieces for welding must be clear of
paint, metallic coatings, dirt, rust, grease and
moisture in the area where they are to be welded.
-Set the welding current and wire feed
-Hold the welding screen (13) in front of your face
and move the welding nozzle to the point on the
workpiece where you wish to complete the weld.
Now press the torch switch (14).
-When the arc is burning, the welding set will feed
wire into the weld pool. When the weld nugget is
large enough, move the torch slowly along the
required edge. Move it to and fro if necessary to
enlarge the weld pool a little.
-Find the ideal setting of the welding current and
wire feed speed by carrying out a test weld. Ideally
an even welding noise will be audible. The
penetration depth should be as deep as possible,
but the weld pool must not be allowed to fall
through the workpiece.
MIG100/MIG130 11