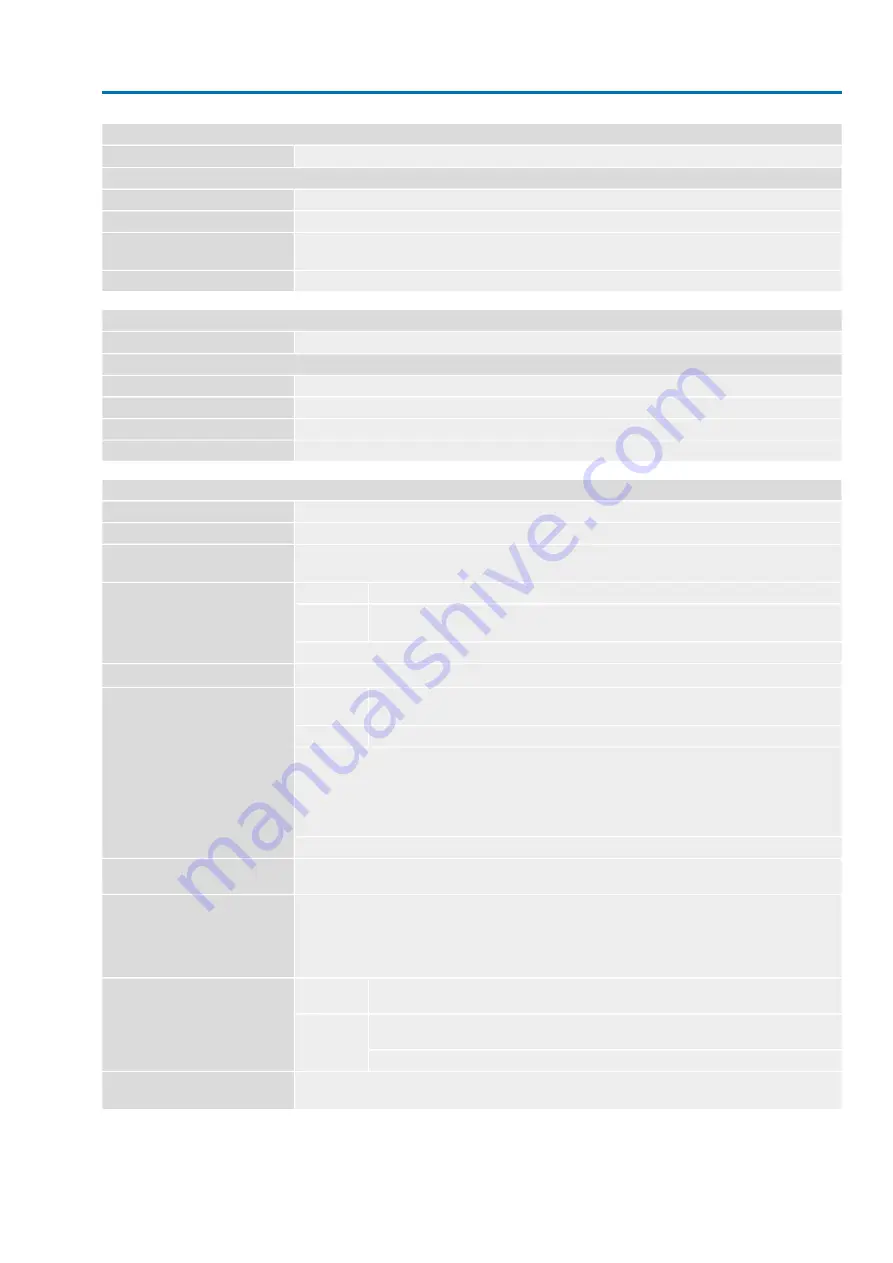
Technical data for blinker transmitter
10
7
starts
Mechanical lifetime
Silver plated contacts:
10 V AC/DC
U min.
250 V AC/DC
U max.
3 A at 250 V (resistive load)
2 A at 250 V (inductive load, cos phi
≈
0.8)
I max. AC current
0.25 A at 250 V (resistive load)
I max. DC current
Technical data for handwheel activation switches
10
6
starts
Mechanical lifetime
Silver plated contacts:
12 V DC
U min.
250 V AC
U max.
3 A at 250 V (inductive load, cos phi = 0.8)
I max. AC current
3 A at 12 V (resistive load)
I max. DC current
Service conditions
Indoor and outdoor use permissible
Use
Any position
Mounting position
≤
2 000 m above sea level
> 2,000 m above sea level, on request
Installation altitude
–30 °C to +70 °C
Standard:
Ambient temperature
–40 °C to +70 °C
–60 °C to +60 °C (with 3-phase/1-phase AC motors)
Options:
For exact version, refer to actuator name plate.
Up to 100 % relative humidity across the entire permissible temperature range
Humidity
IP68 (with AUMA 3-phase/1-phase AC or DC motor)
For special motors differing enclosure protection available (refer to motor name plate)
Standard:
Enclosure protection according to
EN 60529
DS Terminal compartment additionally sealed against interior (double sealed)
Option:
According to AUMA definition, enclosure protection IP68 meets the following requirements:
●
Depth of water: Maximum 8 m head of water
●
Duration of continuous immersion in water: Maximum 96 hours
●
Up to 10 operations during flooding.
●
Modulating duty is not possible during continuous immersion.
For exact version, refer to actuator name plate.
Pollution degree 4 (when closed), pollution degree 2 (internal)
Pollution degree according to IEC
60664-1
2 g, from 10 to 200 Hz (for actuators in AUMA NORM version)
1 g, from 10 to 200 Hz (for actuators with mounted AUMA actuator controls)
Resistant to vibration during start-up or for failures of the plant. However, a fatigue strength may not be
derived from this. Indications apply to actuators with AUMA 3-phase AC motor and AUMA plug/socket
connector. They are not valid in combination with gearboxes.
Vibration resistance according to
IEC 60068-2-6
KS: Suitable for use in areas with high salinity, almost permanent condensation, and high
pollution.
Standard:
Corrosion protection
KX: Suitable for use in areas with extremely high salinity, permanent condensation, and
high pollution.
Option:
KX-G : same as KX, however aluminium-free version (outer parts)
Double layer powder coating
Two-component iron-mica combination
Coating
51
SA 07.2 – SA 16.2 / SAR 07.2 – SAR 16.2
SEM 01.1/SEM 02.1
Technical data