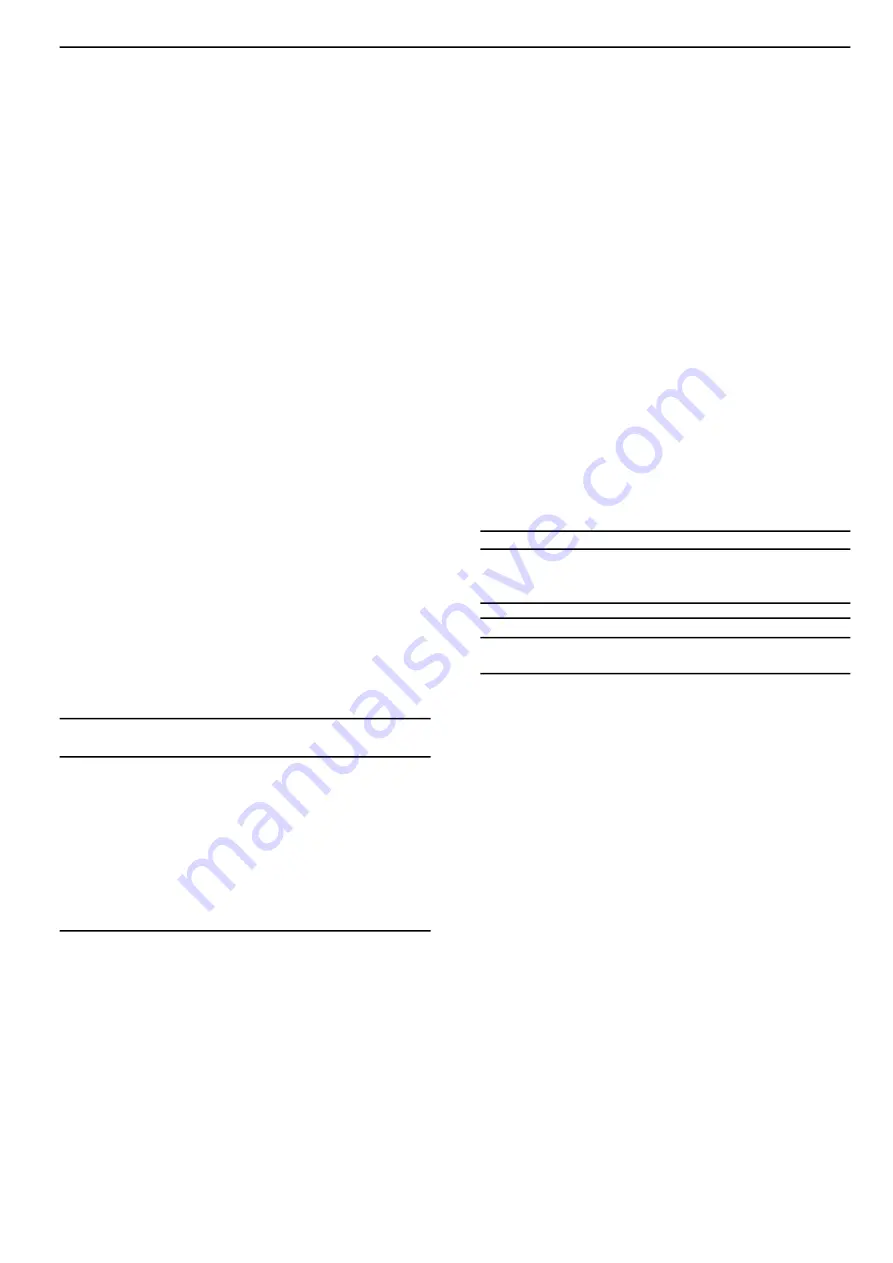
after the throttle has been released. Do not lay the
tool down until rotation has stopped
►
Observe that stored compressed air in the hose
may cause an accidental start
►
Release control device if the energy supply should
fail
Maintenance
Rust protection and internal cleaning
Water in the compressed air, dust and wear particles
cause rust and sticking of vanes, valves etc.
This can be solved by lubricating with oil (a few
drops), running the machine for 5-10 seconds and
wiping off excess oil with a cloth.
Do this before
longer standstills.
Lubrication
The front motor ball bearing should be lubricated
with grease in conjuction with the regular overhaul
of the machine.
For flexible spindle extension
– When fitting the
extended spindle – apply 0.5 cm
3
of grease type
“Lubricating Engineers LE3752” (or EP grease) at
the bottom of the hole in the collet holder.
Lubricating guide
Use lubricants of good quality. The oils and greases
listed in the lubrication table are examples of lubric-
ants that can be recommended.
Air lubrication
General purpose
Bearings
Brand
Energol E46
Energrease LS-EP2
BP
Spheerol EP L2
Castrol
Arox EP46
Beacon EP2
Esso
Chopin 46
Rembrandt EP2
Q8
Almo oil 525
Mobilegrease XHP 222
Mobil
Tonna R32
Alvania EP2
Shell
Aries 32
Multifak EP2
Texaco
BR2 Plus
Molycote
Overhaul
T
WARNING Overspeed could result in serious
injury or death
►
If governor is used, check that correct governor
is assembled. Careless handling may put it out of
order
►
Do not disassemble security parts, e.g. speed
governor or overspeed shut-off. These parts must
be completely replaced when damaged
►
Always check the free speed of the machine after
service. See Section
Preparation before using the
die grinder
The entire machine should be checked regularly at
six-month intervals. If it is in heavy duty service or
not running properly it should be taken out of service
more often for inspection.
The strainer at the air inlet should be cleaned fre-
quently to prevent clogging and decreased capacity.
Useful information
You can find all kind of information concerning Pro
products, accessories, spare parts, published matters
on our WEB site!
C
Log in to www.pro-powertools.com
Technical data
Noise and vibration emission
dB(A)
Noise (according to ISO 15744)
71
Measured sound pressure level
-
Determined sound power level
3
Spread in method and production
m/s
2
Vibration (according to ISO 8662-13)
<2.5
Measured vibration value
-
Spread in method and production
Declaration of noise and vibration emis-
sion
These declared values were obtained by laboratory
type testing in compliance with the stated standards
and are not adequate for use in risk assessments.
Values measured in individual work places may be
higher than the declared values. The actual exposure
values and risk of harm experienced by an individual
user are unique and depend upon the way the user
works, the workpiece and the workstation design, as
well as upon the exposure time and the physical
condition of the user.
We,
Atlas Copco Tools AB
, cannot be held liable
for the consequences of using the declared values,
instead of values reflecting the actual exposure, in
an individual risk assessment in a work place situ-
ation over which we have no control.
7
© Atlas Copco Tools - 9836 3959 00
Safety and operating instructions
G2414-S080