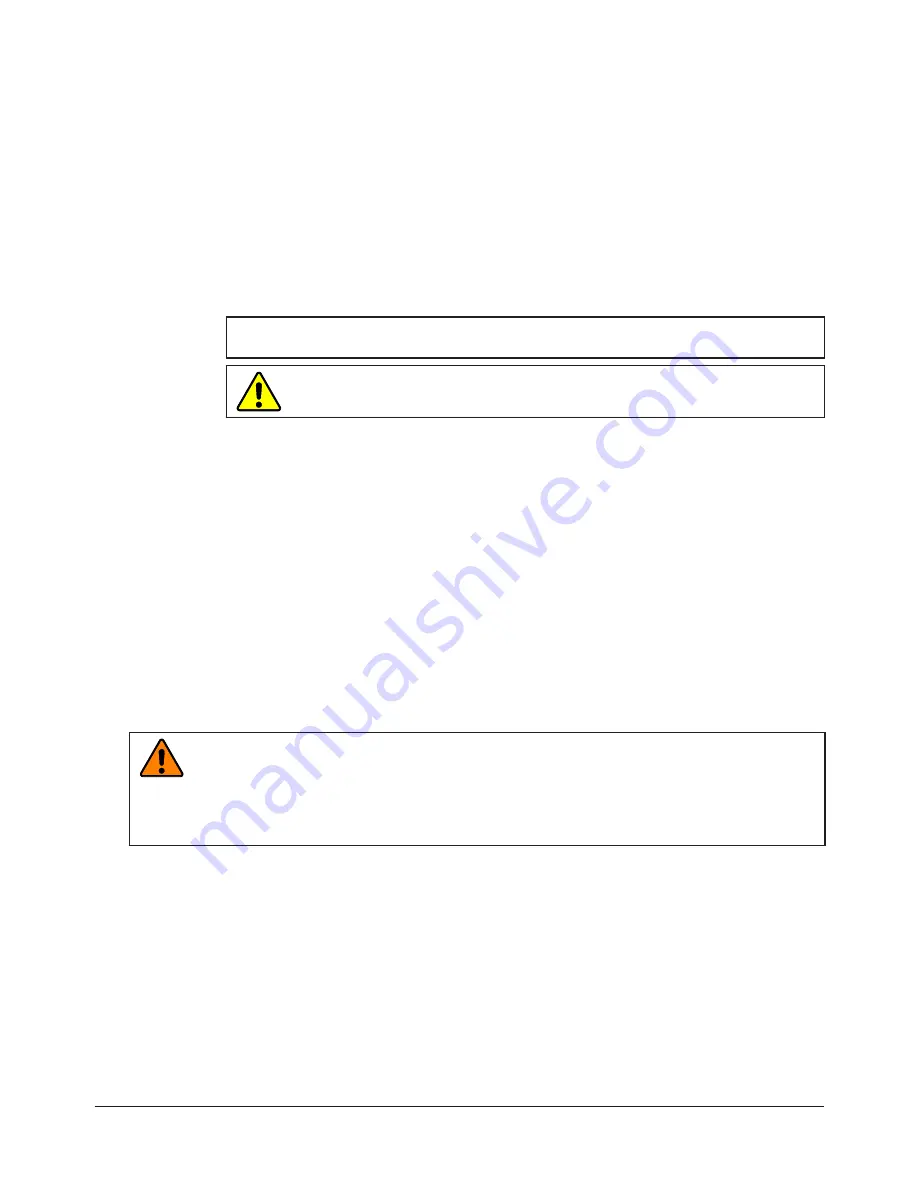
Manual, Collision Sensor,SR‑82
Document #9610‑60‑1007‑08
Pinnacle Park • 1031 Goodworth Drive • Apex, NC 27539 USA • Tel: 919.772.0115 • Fax: 919.772.8259 • www.ati‑ia.com
13
3.3.2 Determining Exact Pressure Required
1.
Set the pressure approximately 5 psi (0.3 Bar) higher than the pressure calculated in
Section 3.3.1—Calculating Estimated Pressure Setting
2.
Run the robot through a fully loaded cycle.
3. Watch for crash signals.
If the collision sensor does not generate a crash signal (open circuit) slightly reduce the pressure
until a crash signal is generated and then increase the pressure slightly until the unit runs without
false crash signals.
If the collision sensor does generate a crash signal increase the pressure slightly until the unit runs
without false crash signals.
NOTICE:
If the pressure required is above 90 psi remove the unit from service and
contact ATI to determine the correctly sized collision sensor model for this application.
CAUTION:
Use of pressures in excess of 90 psi can result in excessive
damage to the unit in the event of a crash and voids the warranty.
4. Operation
With the Collision Sensor mounted and connected pneumatically and electrically the unit may be placed into
operation. If possible, for safety and convenience, position the Collision Sensor and the tooling vertically so that the
load is suspended below the Collision Sensor. Apply low‑pressure air (2–15psi, 0.15–1bar) to the unit. Gradually
increase the air pressure until the desired working pressure is applied.
In operation, the Collision Sensor should be supplied with the minimum air pressure necessary to allow continuous,
uninterrupted operation of the unit. Nuisance collision detections caused by high accelerations and unanticipated
loads will occur if the air pressure is too low. The magnitude of overhung loads, robot accelerations, and applied
loads prevent ATI from recommending air pressure settings. Where high robot accelerations are anticipated the
user may wish to supply the Collision Sensor with electronically variable or multiple, switchable air supplies.
Alternatively, where working loads are small the Collision Sensor may be outfitted with auxiliary springs and
supplied with high‑pressure air only during robot moves. Using these techniques, the Collision Sensor may be
supplied with higher air pressure when higher loads or accelerations are anticipated.
5. Maintenance
WARNING:
Do not perform maintenance or repair on the Collision Sensor with air pressure
applied, current supplied to the sensor, or the robot in an unsafe condition. Injury or
equipment damage can occur if this is not observed. Always ensure that air pressure has
been vented from the unit, that electrical current is not supplied to the Collision Sensor’s
signal circuit, and that the robot is in a safe, locked‑out condition consistent with local and
national safety standards before performing maintenance or repair on the Collision Sensor.
The Collision Sensor is a reliable device fabricated using heavy‑duty components. In normal operation the unit
requires no maintenance if proper air quality and pressures are maintained. Service kits are available in the event
that the Nano connector or collision sensing switch becomes damaged.
Proper collision sensing should be verified on a regular basis. This can be scheduled twice a year or as a part of any
robot or work cell preventive maintenance activities.
In applications where a high number of collisions occur on a regular basis, the life of the Collision Sensor can be
extended with periodic maintenance. Partial disassembly allows the unit to be cleaned, re‑greased, and reassembled
without special tools or adjustment procedures. Such maintenance work should be conducted every 5,000 or
fewer collisions.