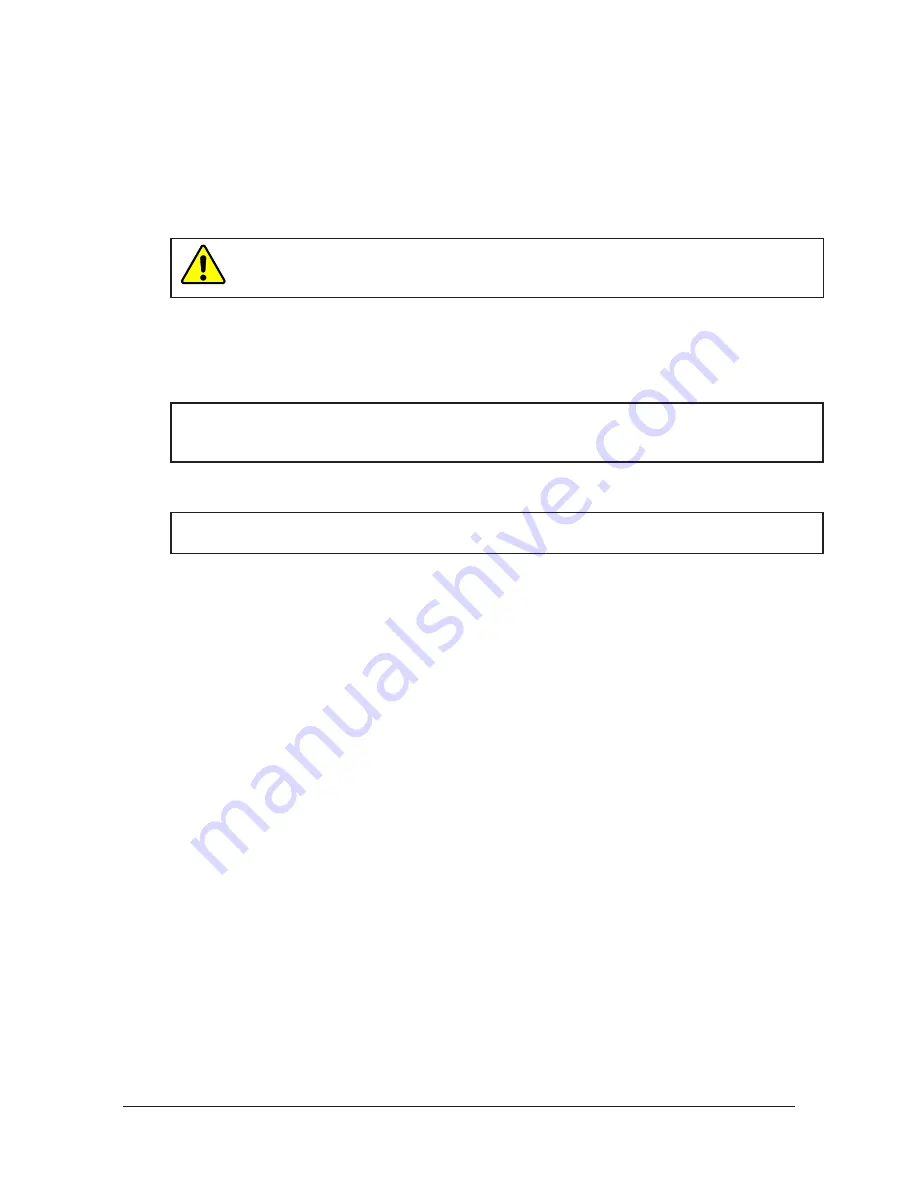
Manual, Robotic Electric Tool Changer, QC‑18
Document #9620‑20‑B‑18 Electric Tool Changer‑06
Pinnacle Park • 1031 Goodworth Drive • Apex, NC 27539 • Tel: 919.772.0115 • Fax: 919.772.8259 •
B-16
US Patent No.: 8,132,816 B2
3.3 Fail-Safe Condition
In the event of power loss to the locking mechanism the Tool Changer
will not uncouple
. A slight
separation between the Master and Tool plates might occur just after power loss but at this point the worm
gear teeth will not back drive without power being applied to the unlatch command. This feature provides
the Tool Changer with a fail‑safe mechanism.
Positional accuracy may not be maintained during power loss but will be regained once power is
re‑established to the motor module.
CAUTION:
Do not use the Tool Changer in the fail-safe condition for extended periods
of time. Do not transport the Tool Changer in the fail-safe condition. Possible damage
to the locking mechanism could occur.
3.4 Procedure for Tool Drop Off
1. Place the tool securely in the tool stand.
2. If the Latch command is ON, turn it OFF. Turn the Unlatch command ON. Within 1 second, the
Master will unlock.
NOTICE:
If the QC is in the proper position or the same signal is raised a consecutive number of
time, the unit will not respond to the repeated signals. The Unlatch and Latch output signal must
be on for a minimum of 50 ms or the QC will not respond.
3. Verify the Unlocked signal is ON and the Locked signal is OFF, indicating the Tool Changer is in the
Unlocked position.
NOTICE:
The Unlocked signal should read “ON” and the Locked signal should read “OFF”. Any
other condition indicates a problem and the robot program should be halted.
4. Move the Master away from the tool.