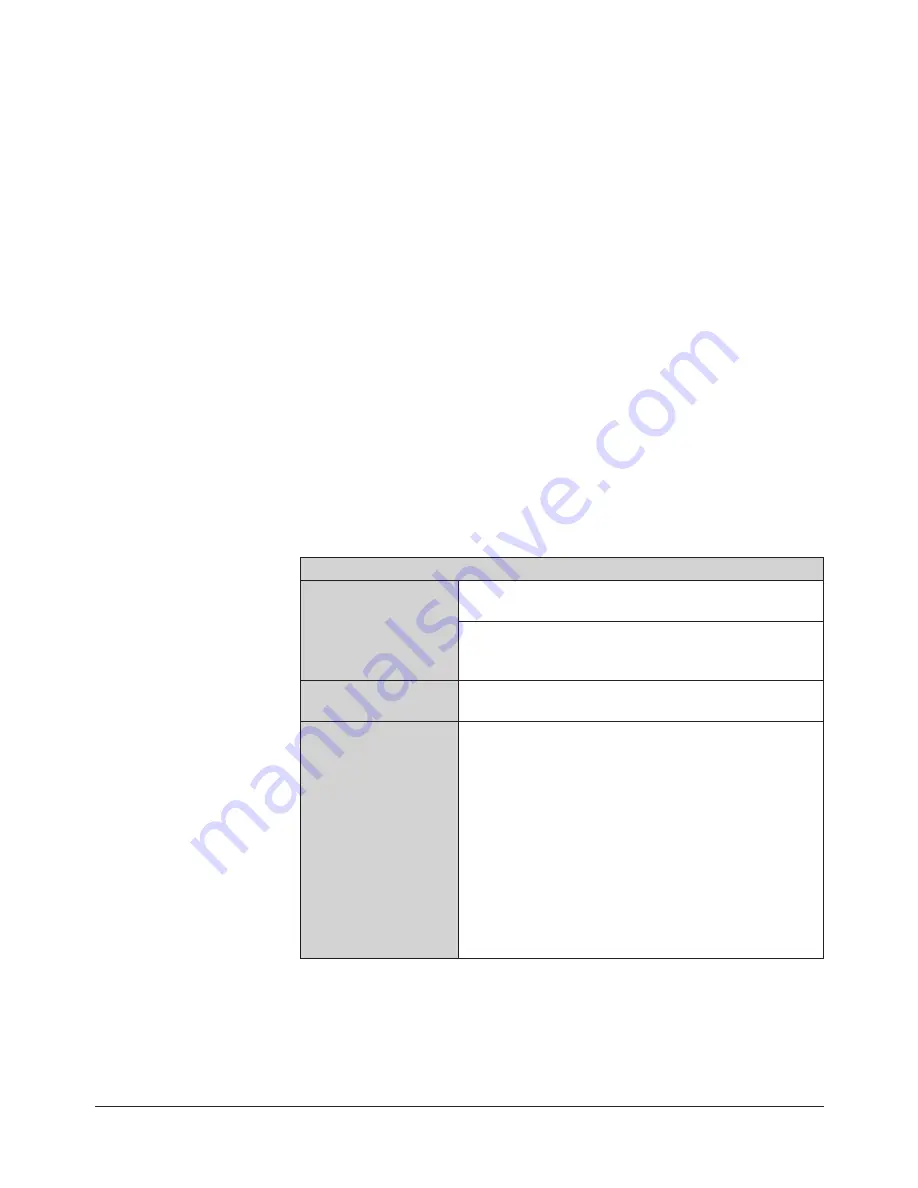
Manual, Robotic Deburring Tool, RCV‑490 Series
Document #9610‑50‑1032‑06
Pinnacle Park • 1031 Goodworth Drive • Apex, NC 27539 USA • Tel: +1.919.772.0115 • Fax: +1.919.772.8259 • www.ati‑ia.com
8
2.1 Tool Collet Systems
The standard tool holding system for RCV‑490 series of products is an economical, industry standard
ER‑11 collet design. This design is suitable for most applications where industry standard shank diameter
cutting tools are used and run out tolerances of up to 0.001” (0.025 mm) are acceptable. The ER‑11 collet
system is used worldwide on machine tools which allows users to procure different collet sizes from local
industrial supply firms.
All deburring tool products utilize removable collets to grip customer supplied cutting tools. Different collet
diameters may be substituted to retain the various bur shank diameters. The collet retaining nut is loosened
to open the collet, allowing cutting tools to be removed and inserted. Once the tool is set to the desired
depth, wrenches are used to tighten the collet nut causing the collet securing the cutting tool. The air motor
design does not allow the installation of quick‑change or drawbar collet systems.
2.2 Deburring Tool Part Number Structure
For the following part number, 9150‑RCV‑XXX
•
“RCV” designates a multi‑axis a tool of radial compliance and vane motor
•
“XXX” designates the motor power in Watts
2.3 Technical Description
A technical overview of the product is provided in the following section: For additional technical
specifications (refer to
)
2.3.1 Environmental Limitations
2.3.1.1 Operation
Table 2.1—Operation
Installation Position
Mounted to robot by means of the side
mounting pattern.
Mounted to a table or stand by means of the bench
adapter. The robot is carrying the work piece to
the RCV‑490.
Temperature Range
5
°
C – 35
°
C
41
°
F – 95
°
F
Utilities
The tool requires the following:
•
Clean, dry, filtered air. The vane‑type air motor
can be operated with the recommended amount
of air tool oil to the motor air supply.
•
A coalescing filter and filter elements that are
rated 5 micron or better.
•
Air supply to the spindle must be 6.2 Bar (90 psi)
to develop the full rated power.
•
The radial compliance (centering) air must be
supplied at 1.0–4.1 Bar (15–60 psi) from a
regulated source.