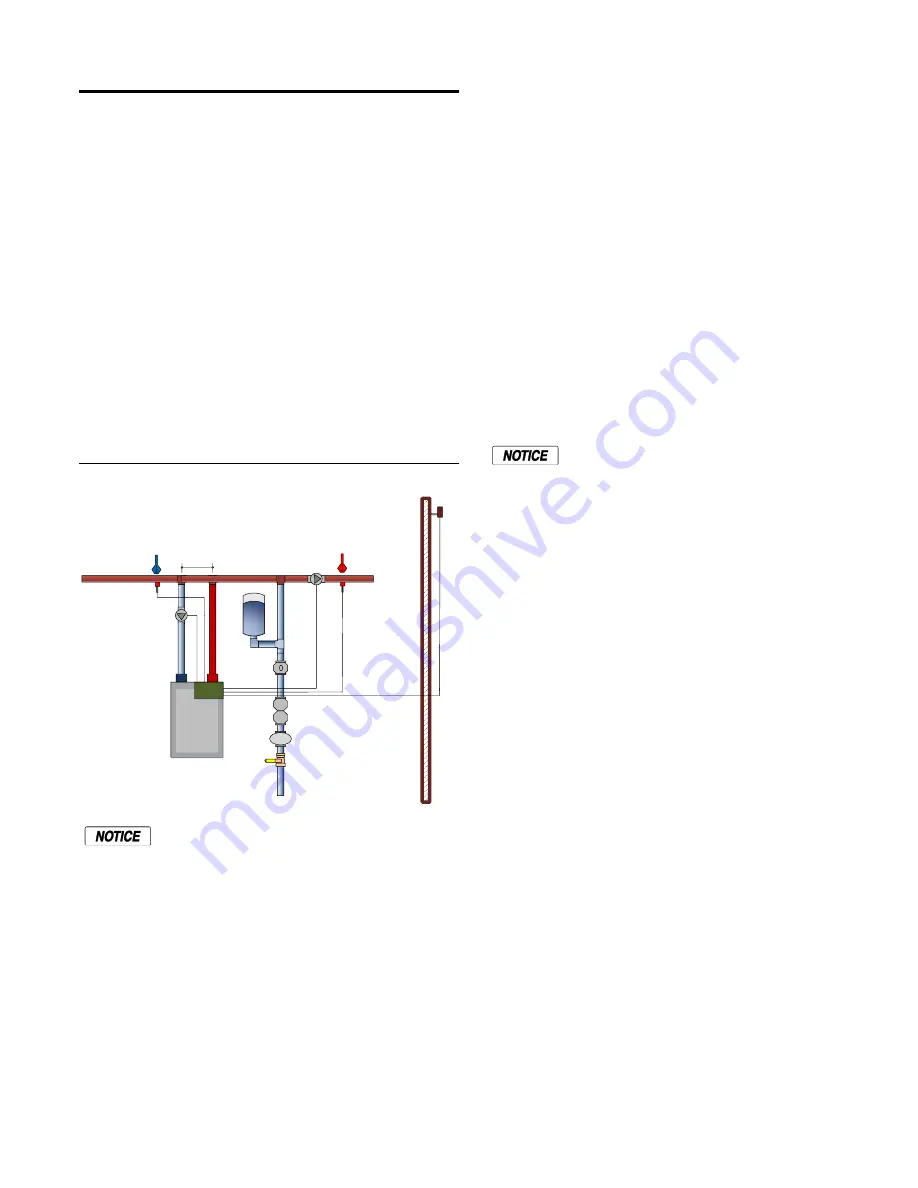
CONTROL METHODS
HeatNet Control V3 3.x
Page 31
Heating Control Methods
An overview of the (5) methods for controlling the KN-Series
boiler are presented here. They are outlined in more detail at
the end of this section.
Heating Control Method 1
The first method is to use the KN-Series boiler in its stand-
alone modulating method. This method uses a PID algorithm
to maintain a setpoint and is enabled using the HEAT
DEMAND input. Closing a relay contact or switch across the
HEAT DEMAND input will cause the MASTER boiler to
control all MEMBER boilers using H-Net.
A MEMBER boiler may also be controlled by the HEAT
DEMAND input (LOCAL mode). The MEMBER boiler will
then ignore commands from the MASTER and maintain its
LOCAL SETPOINT at the supply sensor.
Figure 20
Basic Single Boiler
MASTER
System Header Sensor
System Return
Sensor
Lo
ca
l P
u
m
p
System Pump
E
xp
a
n
sio
n
T
an
k
Backflow
Prevention
Pressure
Reducing
Ball Valve
Sy
st
em
P
u
m
p
Su
p
p
ly
H
ea
d
er
Se
n
so
r
HeatNet
Outdoor Air Sensor
MIN 3X PIPE DIAMETERS
MAX 10X PIPE DIAMETERS
BETWEEN CENTERS
WM
Water Meter
System Supply
Sy
st
em
R
e
tu
rn
Se
n
so
r
The example drawings in this section are
simplified. They are meant to illustrate
connections to the HeatNet V3 control. Only major
components are illustrated. The system engineer must ensure
additional safeties, piping, maintenance valves, and
components meet code requirements and safe operation.
Heating Control Method 2
The second method is to view the KN boiler as two separate
boilers or as a HIGH/LOW boiler using T1 & T2.
Heating Control Method 3
The third method is to allow a remote 4-20 mA or 0-10 VDC
signal to control the firing rate (modulation) of the boiler
using the 4-20mA input, along with the 4-20mA REMOTE
ENABLE input.
Heating Control Method 4
The fourth method turns the boiler ON and OFF @ 100%
modulation using the AA terminal.
Heating Control Method 5
The fifth method uses an RS485 digital communications cable
with the MODBUS protocol. The boiler is controlled by
writing and reading registers using MODBUS commands. A
bridge module may also be used to convert BACnet or
LonWorks protocols to MODBUS.
Short cycling may occur when a firing rate is
sent to a MEMBER boiler that would cause the
supply temperature to raise high enough to trip
the operating limit (low flow rate). After the
supply temperature falls, the boiler would
restart, and the process may continue. A
MEMBER boiler would use its supply (outlet)
sensor to protect itself from short cycling by
limiting the firing rate coming from the
MASTER. This occurs when the MEMBER’s
supply temperature increases above the
(OPERATE LIMIT- OPERATE LIMIT
BAND).
Operating Limit
When the MASTER boiler or an external control input is used
to control a MEMBER boiler (i.e., AA, T1-T2, 4-20mA, H-
Net), a software operating limit on the MEMBER boiler will
be used to limit the maximum output of the MEMBER boiler.
This operating limit can be adjusted in the
SETTINGS:
SETPOINTS: OPERATE LIMIT
.
There is also an associated operating limit band that must be
set in conjunction with the operating limit to help prevent this
LIMIT from being reached. Its purpose is to limit the output
of the boiler as it approaches the operating limit. If the band is
set to 10 degrees, then for every degree that it approaches the
operating limit, the maximum output will be lessened by 10%.
With a band of 20 degrees, for every degree that it approaches
the band, the maximum output will be lessened by 5%. You
can think of this operating limit as a smart aquastat which
prevents the High Limit from tripping. This method
minimizes boiler short cycling when using external inputs.
The minimum setting is 1 degree and effectively turns the
limit band OFF. The default setting is 20F.