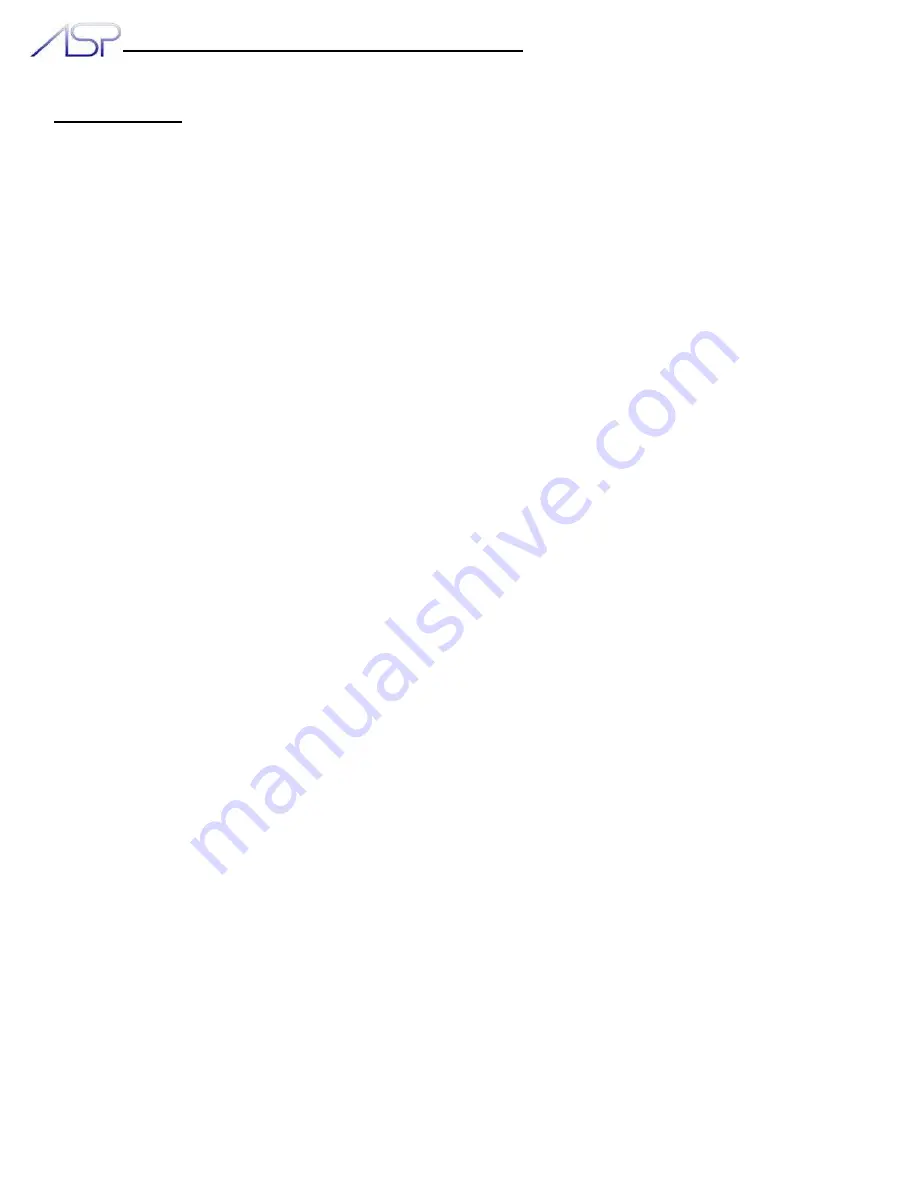
American Stainless Pumps, Inc.
www.aspumps.com
4
Disassembly
Disconnect and lockout the electrical power before attempting any disassembly.
The pump may contain hazardous fluids. Drain and flush and take necessary
precautions.
It is not necessary to remove piping from the case to disassemble the pump. Pump is a back-pullout design and unless
the casing needs to be repaired or replaced, it can stay in place during servicing. See page 7 for cross sectional drawings.
1. Close all valves and drain pump and pipes. Flush pumps and piping if necessary.
2. Remove any motor hold down bolts from the motor foot or stainless steel pump base (Item 800)
3. Remove the eight (8) case bolts (Item 7CS) with a 3/16” Allen wrench.
4. Pull the motor and pump internals back out of the case. The baseplate (Item 800) will slip off when the bottom two
case bolts are removed and can be left with the pump case.
5. Remove the case o-ring (item 500) and inspect for damage or hardness.
6. If the motor is a three phase motor, a locking mechanism (item 7SC) is used to prevent the impeller (item 200) from
unthreading if started in the wrong direction. The locking screw (item 7SC) is installed with removable Loctite® thread
locking compound, to prevent it from coming out when operating in the correct rotation. Remove this locking screw by
turning it
counterclockwise
while holding the impeller against rotation. If the pump casing has a label indicating the
impeller locking screw has LEFT HAND threads, or if the motor is manufactured by Emerson or Nidec, remove this
screw by turning it
clockwise
.
7. Remove the impeller (item 200) by turning the impeller counterclockwise (when looking at the impeller from the pump
end) while holding the motor shaft. It may be necessary to remove the motor shaft plug/cap in the center of the rear of
the motor to gain access to the shaft. Using a screwdriver, wrench or vise grips as needed, hold the shaft tightly
against rotation while turning the impeller.
DO NOT apply any heat to the components
. If you are unable to hold the
shaft in this manner, remove the rear motor housing and grip the motor shaft with vise grips or other similar device (do
not hold shaft where bearings will mount).
8.
Model SSP Only:
There should be several spacing washers behind the impeller. These spacers locate the open
impeller vanes close to the case for efficient operation. Measure the thickness of this stack of spacers for future
reference. Remove them from the shaft but do not lose these washers. You will need them for reassembly.
9. Remove the rotating element of the mechanical shaft seal (item 300). This element is held in place by the impeller
only. If the rotating element does not come off easily, it is stuck to the shaft. Pry up the seal plate (Item 400) with
screwdrivers or pry bars. The seal plate should compress the seal spring and force the seal off the shaft. If seal is
stuck, and you must pry with force, do not pry towards your face or body. The seal and seal plate can come free
unexpectedly and injure you.
10. If the seal plate (item 400) did not come off with the seal, remove it now.
11. To replace the stationary seal seat, you will need to press it out from the back of the sealplate (Item 400). Do not push
with your finger, as you may cut it on the edges of the seal plate when the seal pushes out. Use a flat head screw
driver to press seal seat out of the seal plate.
12. If you plan to replace the motor or motor adaptor (Item 600), remove the four motor adapter bolts (Item 7MB) with a
7/32” Allen wrench. Remove the motor adaptor.
13. If the motor comes with a rubber deflector (slinger), the deflector should go outside of the motor adapter plate and
must be removed if the adapter plate is to be removed.
14. Check the suction o-ring (item 510) in the casing suction nozzle. It may be difficult to remove. Use a sharp pointed awl
or similar device to pry the o-ring from the groove, or blow it out with a high pressure air nozzle. Replace o-ring if
damaged, swollen, fretted, or worn out. The o-ring improves the pumps efficiency, but is not necessary for pump
operation.