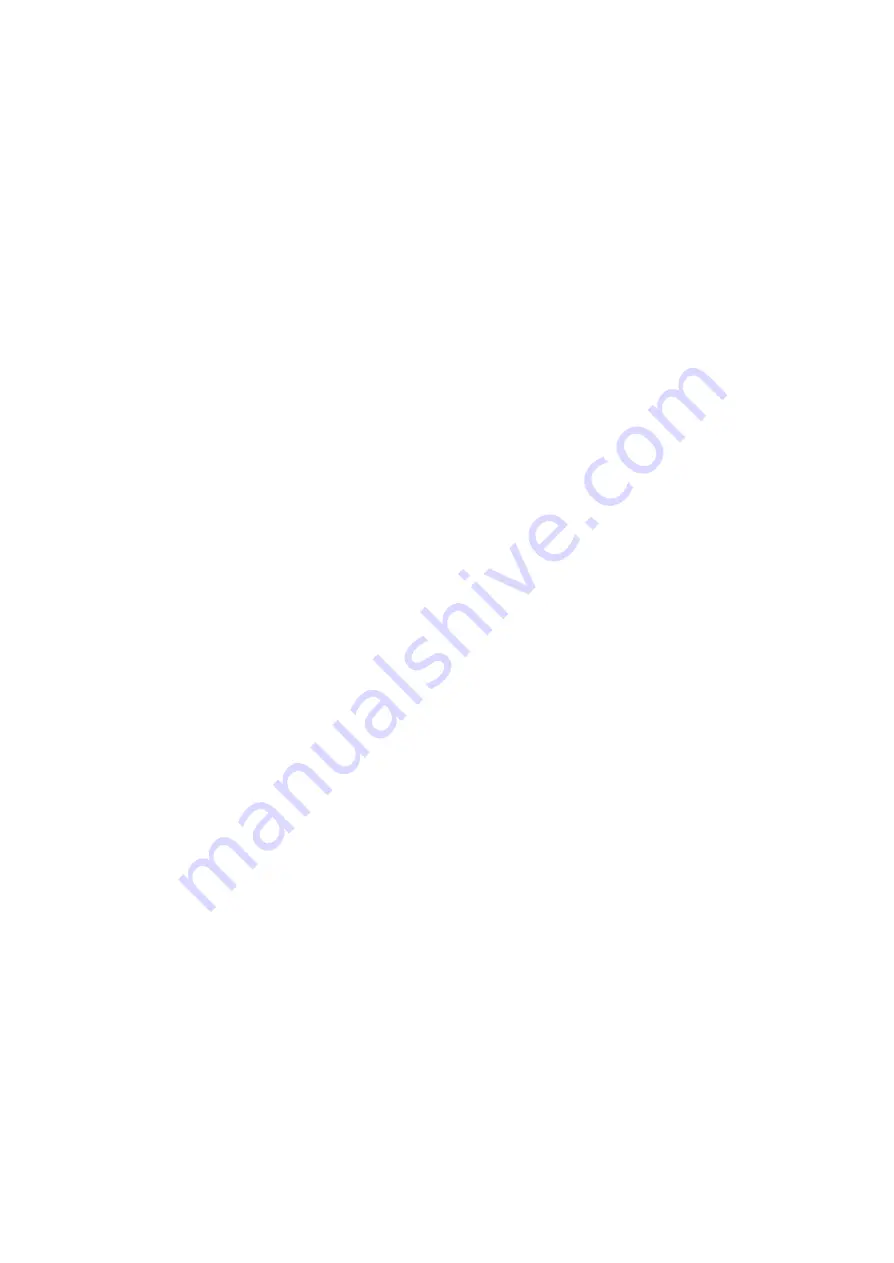
25
5.2 – PARAMETERS DESCRIPTION
GROUP “
]
SP” (PARAMETERS RELATIVE TO THE SET POINT):
They allow the control Set programming and the Set functioning modalities.
nSP
– NUMBER OF THE PROGRAMMABLE SET POINT: It permits to define the number of the Set Point which are desired to
be programmed and stored (from 1 to 4).
SPAt
– ACTIVE SET POINT : Whenever are stored more than one Set Point, it permits to select the active Set Point.
SP1 -
SET POINT 1: Value of the Set Point n. 1
SP2 -
SET POINT 2: Value of the Set Point n. 2 (it appears if “nSP” >2 only)
SP3 -
SET POINT 3: Value of the Set Point n. 3 (it appears if “nSP” >3 only)
SP4 -
SET POINT 4: Value of the Set Point n. 4 (it appears if “nSP” =4 only)
SPLL
– LOW SET POINT: Lower value programmable as Set Point
SPHL
– HIGH SET POINT : Higher value programmable as Set Point
GROUP “
]
InP” (PARAMETERS RELATIVE TO THE INPUTS):
They permit to define the visualization modalities of the variable measured by the probe.
HCFG
– INPUT TYPE : It permits to select the input type : thermocouples (tc), thermoresistances or thermistors (rtd),
normalized signals in current (I), in tension (UoLt) or a measure coming from the serial line (SEr).
SEnS
– PROBE TYPE: Depending on what programmed on par. “HCFG” it permits to select the type of probe :
- thermocouples (“HCFC”=tc): J (J), K (CrAL), S (S) or GREISINGER infrared sensors IRTC1 serie with J (Ir.J) or K (Ir.CA)
linearization.
- thermoresistances/thermistors (“HCFC”=rtd): Pt100 IEC (Pt1) or thermistors PTC KTY81-121 (Ptc) or NTC 103AT-2 (ntc)
- normalized signals in current (“HCFC”=I): 0..20 mA (0.20) or 4..20 mA (4.20)
- normalized signals in tension (“HCFC”=UoLt): 0..50 mV (0.50), 0..60 mV (0.60), 12..60 mV (12.60), 0..5 V (0.5), 1..5 V (1.5),
0..10 V (0.10) or 2..10 V (2.10).
SSC
– LOW SCALE LIMIT IN CASE OF INPUT WITH V/I SIGNALS : This is the value the instrument has to visualise when at
the input it’s present the minimum value measurable on the scale (0/4 mA, 0/12 mV, 0/1 V or 0/2 V).
FSC
– HIGH SCALE LIMIT IN CASE OF INPUT WITH V/I SIGNALS : This is the value the instrument has to visualise when at
the input it’s present the maximum value measurable on the scale (20 mA, 50 mV, 60 mV, 5 V or 10 V).
dP
– NUMBER OF DECIMAL FIGURES: It permits to decide if the measuring resolution has to be 1 (0), 0.1 (1), 0.01 (2), 0.001
(3). In case of temperature probes the allowed resolutions are 1° (0) and 0.1° (1).
Unit
– TEMPERTURE UNIT OF MEASUREMENT : When the temperature is measured by temperature probes, this parameter
permits to define if the visualisation is expressed as degree Centigrade (°C) or Fahrenheit (°F).
Filt
– INPUT DIGITAL FILTER : It permits to program the constant of time as software filter referred to the measured input
value (in sec.) in order to reduce the sensibility at the noises (increasing the time of reading).
OFSt
– MEASURING OFFSET: Positive or negative Offset which is added to the value measured by the probe.
rot
– ROTATION OF THE MEASURING STRAIGHT LINE: It permits to obtain that the offset programmed on par. “OFSt” is not
constant for all the measures. Programming “rot”=1.000, the value “OFSt” is simply added to the value red by the probe
before the visualisation and it results constant for all the measures. If instead it’s desired to have the programmed offset not
constant for all the measures, it’s possible to effectuate the calibration on two desired values.
In this case, to define the values to be programmed on par. “OFSt” and “rot”, it’s necessary to enforce the following formulae :
“rot” = (D2-D1) / (M2-M1)
“OFSt” = D2 - (“rot” x M2)
where: M1 =measured value 1; D1 = visualisation value when the instrument measures M1
M2 =measured value. 2; D2 = visualisation value when the instrument measures M2
It’s then deriving that the instrument will visualise :
DV = MV x “rot” + “OFSt”
where: DV = visualised value; MV= measured value
InE –
“OPE” FUNCTIONING IN CASE OF MEASURING ERROR: It defines which are the error conditions of the input allowing
the instrument to give as output the power programmed on par. “OPE”. The possibilities are :
= Or : the condition occurs in case of overrange or probe breakage
= Ur : the condition occurs in case of underrange or probe breakage
= Our : the condition occurs in case of overrange or underrange or probe breakage
OPE
– OUTPUT POWER IN CASE OF MEASURING ERROR: It permits to program the power that the instrument has to give
as output in case of measuring error. For the ON/OFF regulators the power is calculated considering a cycle time equal to 20
sec.