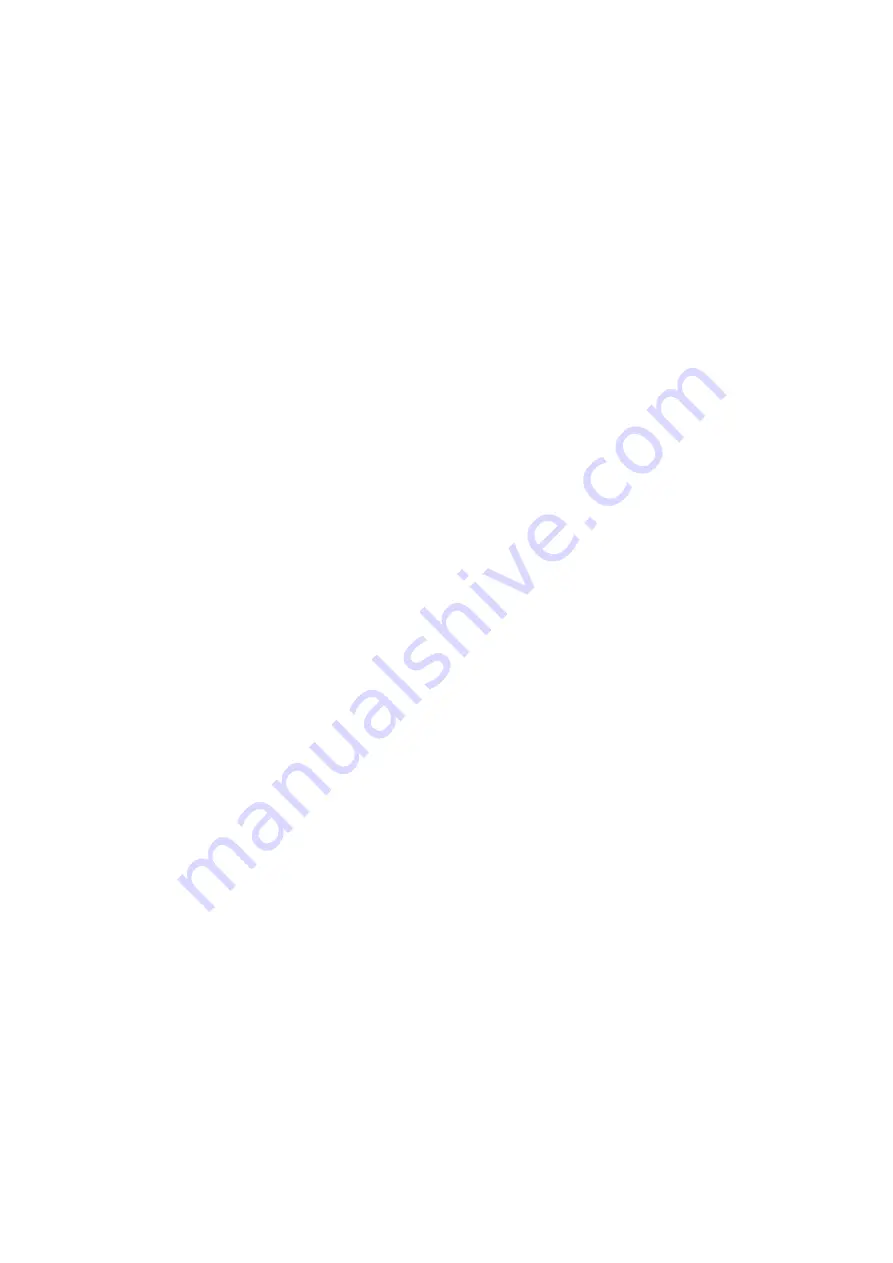
4
1
User Advisory / Application Requirements
The SRH-3 stabilized remote head and related products should only be used by experienced and
trained operators. This product is
not
designed for
inexperienced
users, and must not be used without
proper training.
Stabilization of remote heads is an extremely complex and at times difficult task and therefore
stabilized remote heads do have their limitations. For example, the remote head will only correct for
angular movement and not parallel movement. This means that when the remote head is attached
directly to a lift, or to a pole, or structure that is subjected to vertical movement, it cannot compensate
for lift as it moves up and down (because that movement is parallel). In order to absorb vertical and
parallel movements, the remote head must be mounted on a suitable shock absorber.
Stabilization systems are limited by engine power, as well as their bandwidth or frequency response.
Very fast movements required to correct the camera position may not be within system capabilities.
This can be seen when using longer lenses.
The use of suitable Iso Dampers devices improves the application.
Mounting a suitable Iso Dampers device between the remote head and the mounting point of the head,
will soak up the fast, unwanted movements, leaving the stabilization with unwanted movements that
are slower and within the bandwidth of the system.
There are many Iso Damper devices that follow different designs and qualities.
Choosing the right Iso Damper is as important as the stabilized head itself.
Another purpose of Iso Dampers is that they decouple the stabilized remote head from some
resonance and flexing of the mounting point.
All gimbal-based stabilized remote heads will always face some kind of drift.
Drift is unwanted movement of the system usually caused by the gyros and the earth’s rotation, which
can’t be measured by the MEMS sensors.
Drift is normally measured in degrees per hour.
The SRH-3 remote head has a very small amount of drift that would only be noticed while the head is
stationary over a long period of time. The average drift can be up to approximately 10° in 30 minutes.
Drift can also be caused by a non-calibrated joystick or a loose camera setup, or an Iso Damper that is
too soft.
Reduction of flexing or bending of the camera and lens package, and flexing of the remote head
attachment are critical. The overall setup needs be as rigid as possible because any flexing can cause
the head to vibrate or oscillate. Every attempt to improve the stiffness of the camera setup and the
head attachment, and to reduce or eliminate any flexing should be made.
Many different camera and lens packages can be used with the SRH-3, and there are also many
different ways to mount the remote head. As a result, it is not always possible or practical to obtain
perfect conditions regarding rigidity and balance. This may cause the load to become unstable and it
will then shake and oscillate when the stabilization is active. In these situations, adjustment of the PID
parameters will be required. The correct setting of these PID values is crucial for the proper working of
the system.
An unbalanced camera setup will place more strain on the motors of the SRH-3. The system will need
more force to move the load and this will sometimes increase the possibility of the load becoming
unstable, and that the remote head may over compensate or shake and oscillate.
Please remember that what the remote head is mounted on, and the manner in which it is mounted,
will directly impact on its performance. The total mass of the head and its load are an important
consideration when choosing how and where to mount it. This torque will change in direction and
amplitude in varying amounts. The more solid the mount, the easier it is for the system to perform well.
Sometimes even the leveling linkage on a camera crane will have play or backlash that allows the
mounting point to move slightly when loads are reversed. If there is mechanical play between the
components in the shock absorber, vibrations of the overall system may occur. Iso Dampers with the
appropriate dimensions and hardness should always be used - the system may become too elastic if
the Iso Damper used is too soft, causing vibration.
NOTE
Each of these aspects can lead to the motor power of single axis having to be lowered,
which will limit the effectiveness of the overall stabilization.
User Advisory