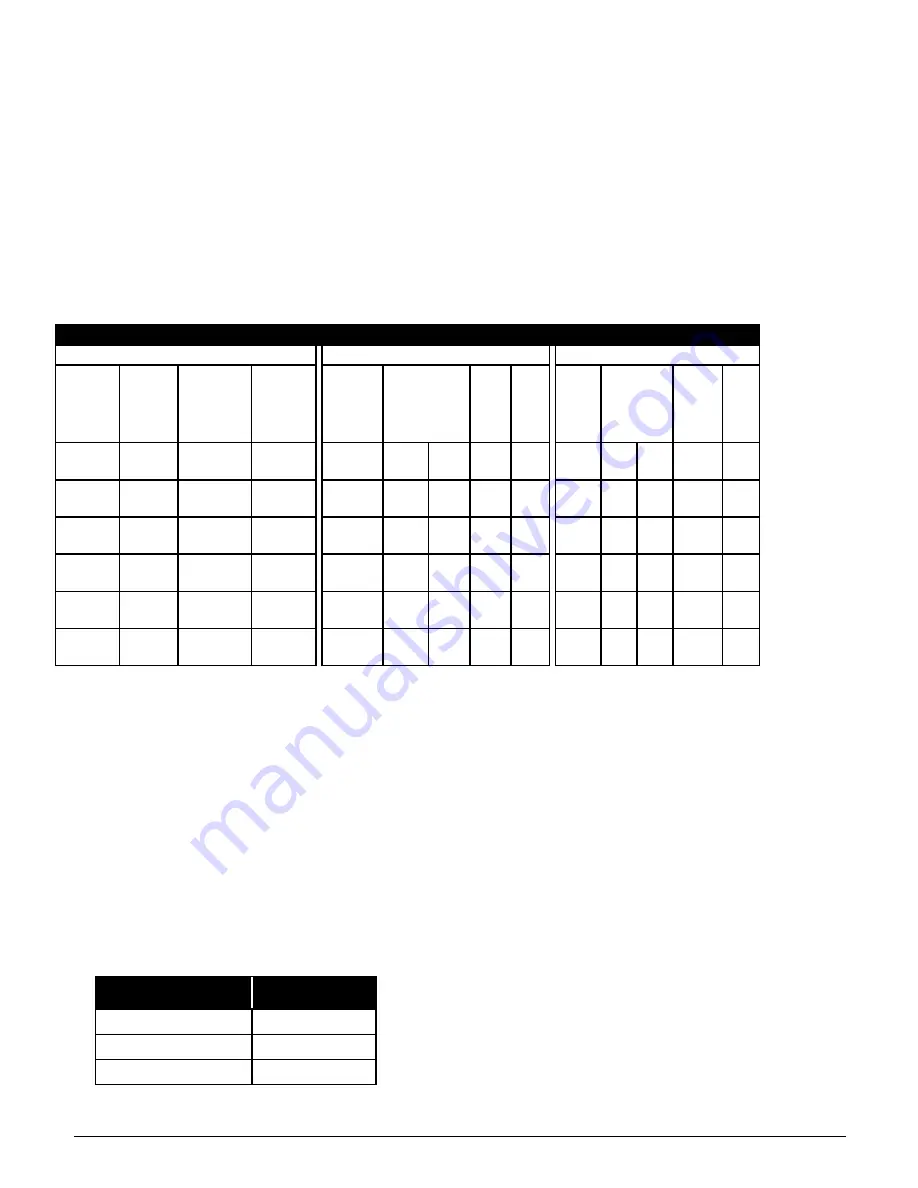
North America • Latin America • India • Europe / Middle East / Africa • China • Pacific Rim
armstrong
international.com
Designs, materials, weights and performance ratings are approximate and subject to change without notice. Visit
armstrong
international.com for up-to-date information.
50
Testing
The following steps require the power supply be turned back on; extreme caution must be exercised when performing service with
the power supply on and the door off.
• When turning the appliance back on, listen for significant noises from the fan and pump. Also, inspect for leaks at the pump
connections.
• Enter the status menu from the home screen to access the sensor readings, and record each reading, making sure that all
sensors and thermometers are reading the same, with the heat off.
• Fire the appliance on maximum output for 5 minutes, in order to check the ∆T from the inlet sensor to the outlet sensor.
-If the ∆T reading is out of design range by more than 10% or there is an A1 or A2 error on the display, refer to coil cleaning
instructions below. Record ∆T to track any increases from one year to the next.
Model
Air Pressure (
∆
P)
HW299
< .7" wc
HW399
< 1" wc
HW599
< .86" wc
Maintenance - continued
• Fire the appliance on maximum output, and measure and adjust the CO
2
percentage as required.
• Fire the appliance on minimum output, and measure and adjust the CO
2
percentage as required.
• If there are an unusual number of G01 faults or if combustion is off significantly, gas supply pressure must be verified at static
(no load) and full building load conditions.
• See Table 3.3, page 17 for specific settings.
• Inspect intake and exhaust screens at the termination point for signs of contamination (i.e. leaves, twigs, etc).
• A differential pressure (∆P) reading should be taken across the exhaust and inlet air connection points of each appliance to
confirm that it is below the maximum shown below.
Table 7.6 Flow and Pressure Drop Heat Exchanger only - (GPM and Feet of Head @ 68°F)
Hydronic Applications
DHW Applications
Model
BTU/hr.
(HW/hr)
Input
Minimum
Flow Rate
must be
clean water
system*
∆
P at
Minimum
Flow Rate
- ft. of
head
Hydronic*
Pipe
Size
Design
∆
T
Hydronic*
@ 95%
efficiency
°F °C
GPM
(LPM)
Head
(M)
DHW
Pipe
Size
Design
∆
T
DHW
@ 97%
efficiency
°F °C
GPM
(LPM)
Head
(M)
HWH 299
300,000
(87.9)
8.5
5.1
1.5”
51.8
28.8
11
(41.7)
9.3
(2.8)
HWD 299
300,000
(87.9)
1.5”
35.3
19.6
16.5
(62.5)
21.1
(6.4)
HWH 399
399,999
(117.2)
11.31
3.9
1.5”
43.2
24.0
17.6
(66.6)
9.4
(2.8)
HWD 399
399,999
(117.2)
2”
29.4
16.3
26.4
(100)
19.2
(5.9)
HWH 599
630,000
(185)
17.8
5.1
1.5”
45.3
25.2
26.4
(100)
9.4
(2.8)
HWD 599
630,000
(185)
2”
30.9
17.1
39.6
(150)
21.5
(6.5)
* Must be closed loop system with clean, treated water.
NOTE: The inlet air pressure should be negative.