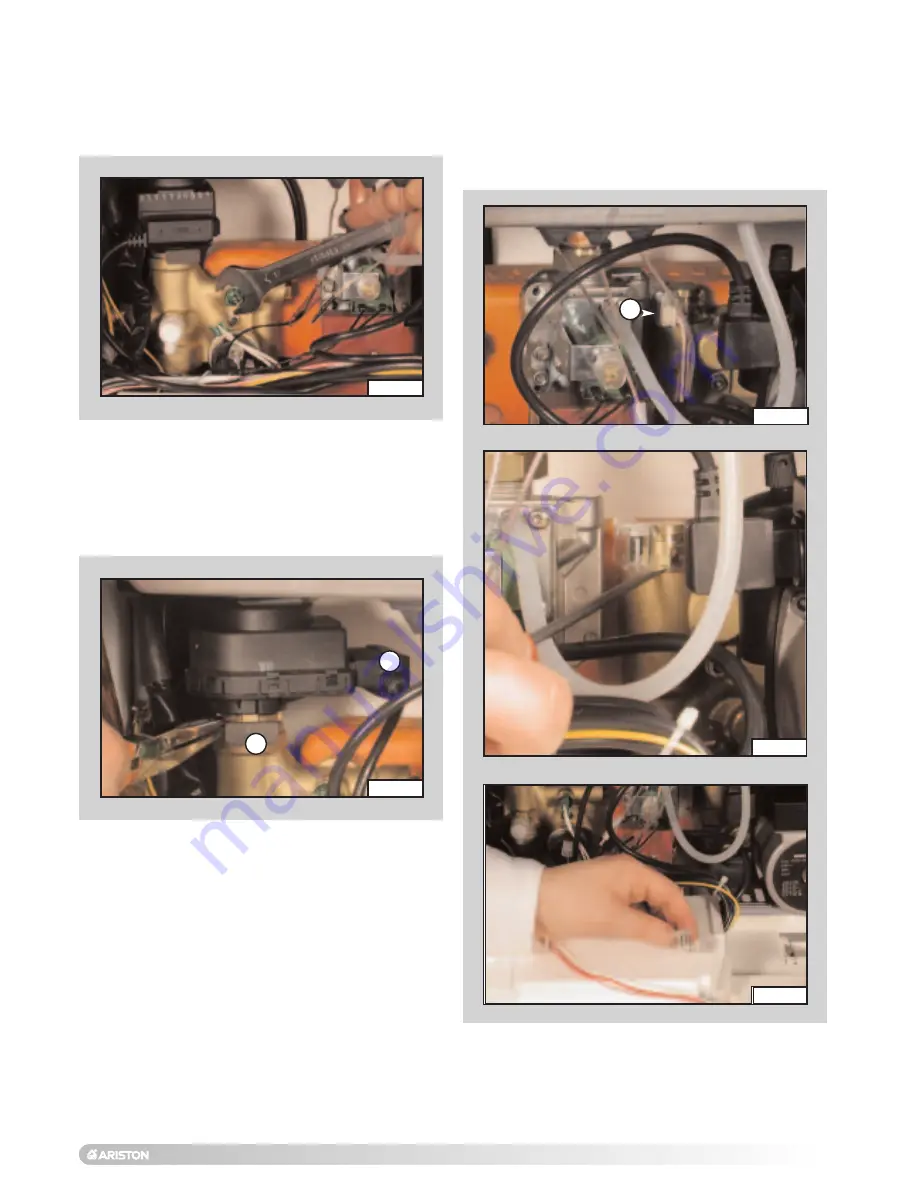
F
IG
. 6.66
F
IG
. 6.67
F
IG
. 6.68
O1
6.5.12 Removing the D.H.W. flow switch
1. Unplug the electrical connector “O1” (F
IG
. 6.66);
2. Remove the D.H.W. flow switch using a screwdriver
(F
IG
. 6.67-6.68).
6.5.10 Removing the D.H.W. temperature sensor
(N.T.C.)
1. Pull off the electrical connector and unscrew the
sensor probe using a suitable spanner (F
IG
. 6.64).
F
IG
. 6.64
6.5.11 Removing the diverter valve actuator
1. Unplug the electrical connector “M1” (F
IG
. 6.65);
2. Release the retaining clip “N1” and remove the divertor
valve actuator
F
IG
. 6.65
M1
N1