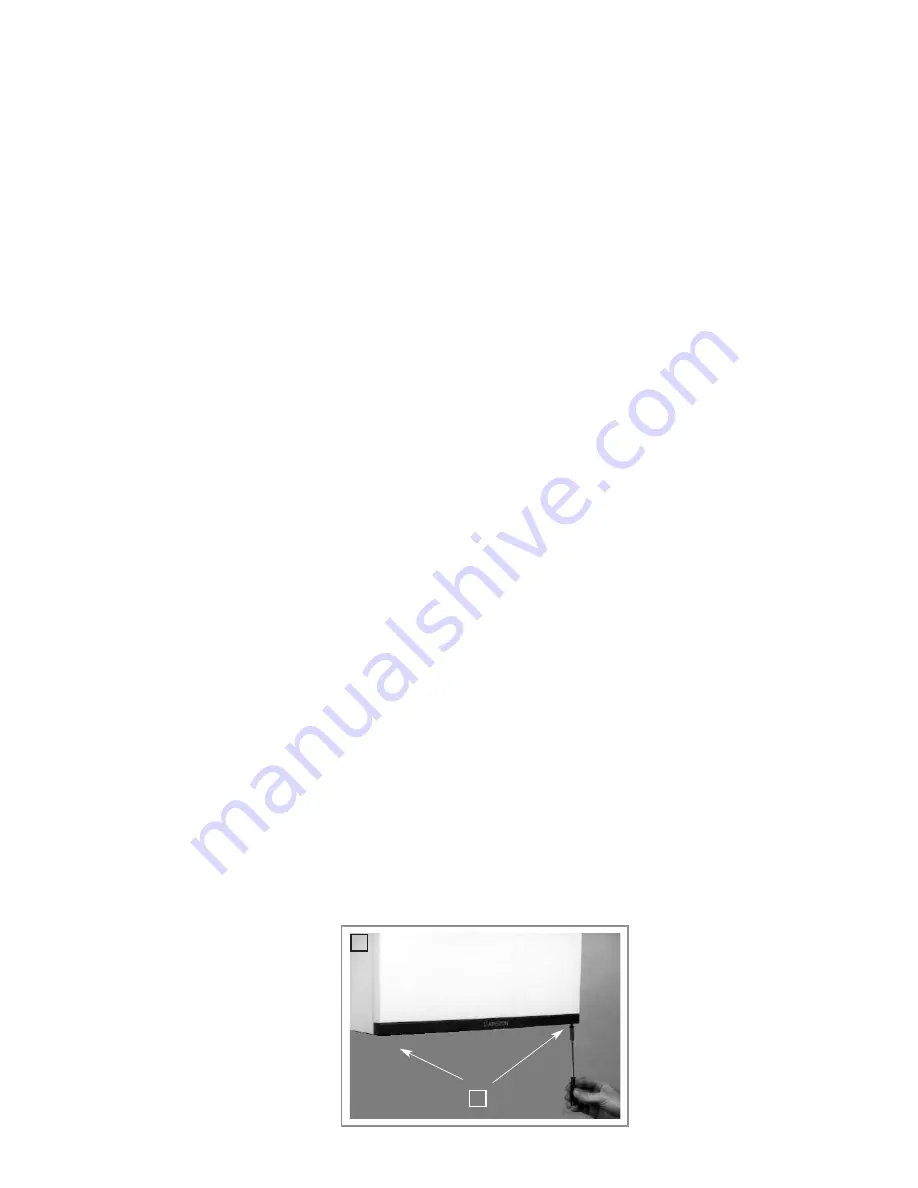
20
B004
3.
COMMISSIONING
3.1
Initial Preparation
Preliminary electrical system checks to ensure electrical safety must be carried
out by a competent person i.e. polarity, earth continuity, resistance to earth and
short circuit.
Filling the Heating System:
Remove the panels of the case and lower the control panel (see point 3.2. for
further information).
Open the central heating flow and return cocks supplied with the connection
kit.
Unscrew the cap on the automatic air release valve one full turn and leave
open permanently.
Close all air release valves on the central heating system.
Gradually open valve(s) at the filling point (filling-loop) connection to the
central heating system until water is heard to flow, do not open fully.
Open each air release tap starting with the lower point and close it only when
clear water, free of air, is visible.
Purge the air from the pump by unscrewing anticlockwise the pump plug and
also manually rotate the pump shaft in the direction indicated by the pump
label to ensure the pump is free.
Close the pump plug.
Continue filling the system until at least 1 bar registers on the pressure
gauge.
Inspect the system for water soundness and remedy any leaks discovered.
Filling of the D.H.W. System:
Close all hot water draw-off taps.
Open the cold water inlet cock supplied with the connection kit.
Open slowly each draw-off tap and close it only when clear water, free of
bubbles, is visible
Gas Supply:
Inspect the entire installation including the gas meter, test for soundness and
purge, all as described in BS 6891:1988.
Open the gas cock (supplied with the connection kit) to the appliance and
check the gas connector on the appliance for leaks.
When the installation and filling are completed turn on the central heating
system (sect. 3.4) and run it until the temperature has reached the boiler
operating temperature. The system must then be immediately flushed through.
The flushing procedure must be in line with BS 7593:1992 Code of practice for
treatment of water in domestic hot water central heating systems.
During this operation, we highly recommend the use of a central heating
flushing detergent (Fernox Superfloc or equivalent), whose function is to
dissolve any foreign matter that may be in the system.
Substances different from these could create serious problems to the
pump or other components.
The use of an inhibitor in system such as Fernox MB-1 or equivalent is strongly
recommended to prevent corrosion (sludge) damaging the boiler and system.
Failure to carry out this procedure may invalidate the appliance warranty.
To dismantle the front part of
the casing, proceed as follows:
1. Loosen the two screws “F”
located on the bottom part
of the boiler until the
first thread on the screws
appears;
1
F
3.2
Removing the Casing
Содержание GENUS 27 MFFI
Страница 17: ...17 B004 Aa GENUS 23 27 30 MFFI Aa GENUS 27 RFFI SYSTEM...
Страница 18: ...18 B004 CN202 P GENUS 23 27 30 MFFI P GENUS 27 RFFI SYSTEM...
Страница 29: ...B004 NOTES...
Страница 30: ...30 B004 NOTES...
Страница 31: ...31 B004...