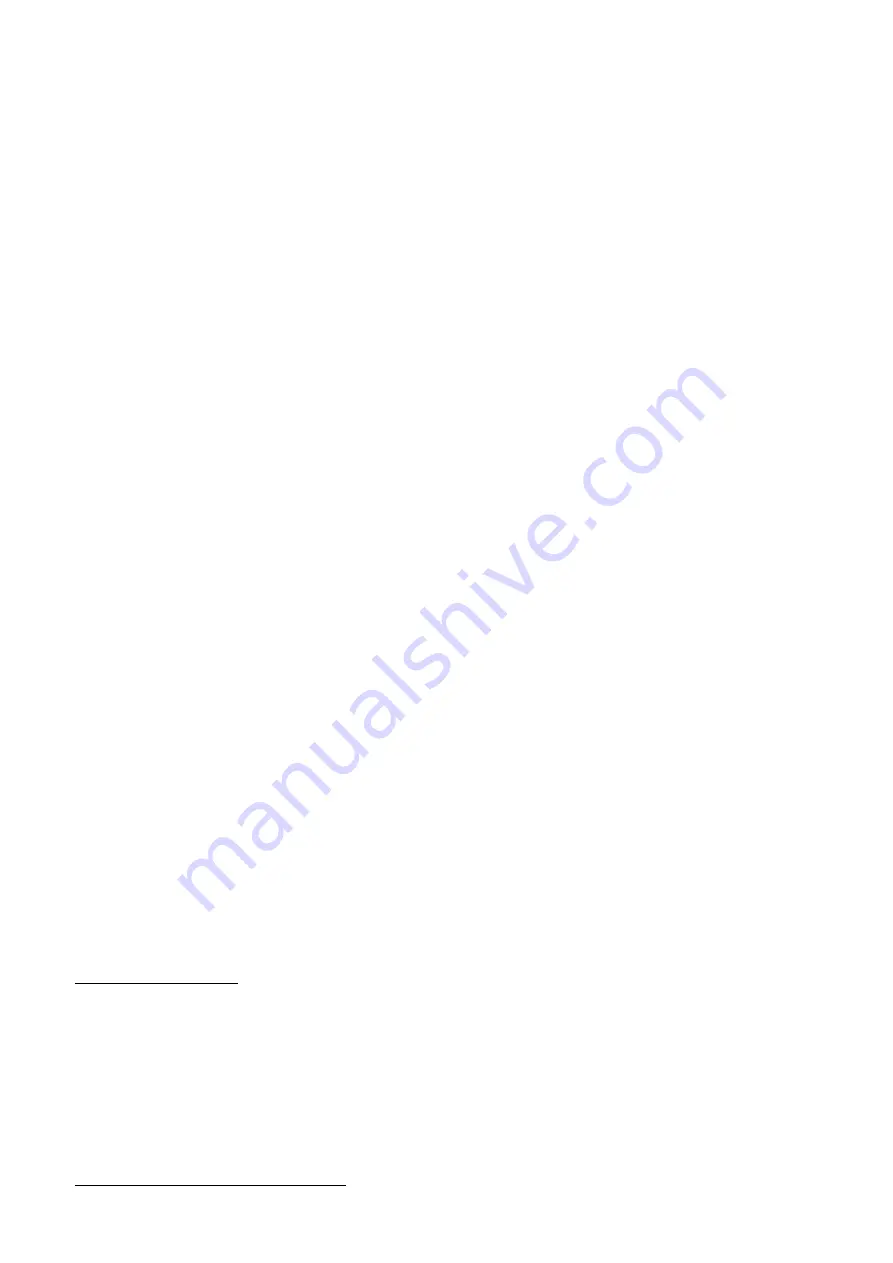
11
-
the suction valve being open at start-up or
the suction tank being emptied without stopping
9.1
INSTALLATION AND COMMISSIONING PERSONNEL
Interventions allowed only to specialised personnel who may eventually delegate to others some operations depending on
specific evaluations (technical capability required: specialisation in industrial plumbing or electric systems as needed).
9.2
OPERATORS AND MAINTENANCE PERSONNEL
Interventions allowed to general operators (after training on the correct use of the plant):
-
pump starting and stopping
-
opening and closing of valves with the pump at rest
-
emptying and washing of the pump body via special valves and piping
-
cleaning of filtering elements
Interventions allowed to qualified personnel (technical capacities required: general knowledge of the mechanical, electrical and
chemical features of the plant being fed by the pump and of the pump itself):
-
verification of environmental conditions
-
verification of the condition of the liquid being pumped
-
inspections of the control/stop devices of the pump
-
inspections of the rotating parts of the pump
trouble shooting
9.3
REPAIR PERSONNEL
Interventions allowed to general operators under the supervision of qualified personnel:
-
stopping of the pump
-
closing of the valve
-
emptying of pump body
-
disconnection of piping from fittings
-
removal of anchoring bolts
-
washing with water or suitable solvent as needed
-
transport (after removal of electrical connections by qualified personnel)
Interventions by qualified personnel (technical capacities required: general knowledge of machining operations, awareness of
possible damage to parts due to abrasion or shocks during handling, know-how of required bolt and screw tightening
required on different materials such as plastics and metals, use of precision measuring instruments):
-
opening and closing of the pump body
- removal and replacement of rotating parts
9.4
WASTE DISPOSAL
Materials: separate plastic from metal parts. Dispose of by authorized companies.
10 IMPROPER USE
The pump must not be used for purposes other than the transfer of liquids.
The pump cannot be used to generate isostatic or counter pressures.
The pump cannot be used to mix liquids generating an exothermal reaction
The pump must be installed horizontally on a firm base.
The pump must be installed on a suitable hydraulic plant with inlet and outlet connections to proper suction and discharge
pipes.
The plant must be able to shut off the liquid flow independently from the pump.
Handling of aggressive liquids requires specific technical knowledge
11 OPERATING FAULTS AND POSSIBLE CAUSES
The pump does not deliver:
1. rotates in wrong direction
2. suction pipe is excessively long and tortuous
3. insufficient geodetic pump head or excessive suction geodetic lift
4. air infiltration into the suction pipe or branches
5. pump or suction pipe not completely covered by liquid
6. impeller channels blocked by impurities
7. check valve on discharge pipe jammed
8. geodetic system height is greater than maximum potential pump head
9. impeller jammed by considerable layer of crystals or by melting of materials for dry rotation.
10. bottom valve blocked by mud or other debris
11. bottom valve insufficiently immersed
12. bottom valve faulty, thereby causing suction valve to empty when pump stops
Pump discharge rate or pressure insufficient: see 01, 02, 03, 04, 05, 06, 10, 11, 12
Содержание ZMR 02.30
Страница 2: ...2 1 DISASSEMBLING SEQUENCE ...
Страница 16: ...16 ...
Страница 17: ...17 ...
Страница 18: ...18 ...
Страница 19: ...19 ...