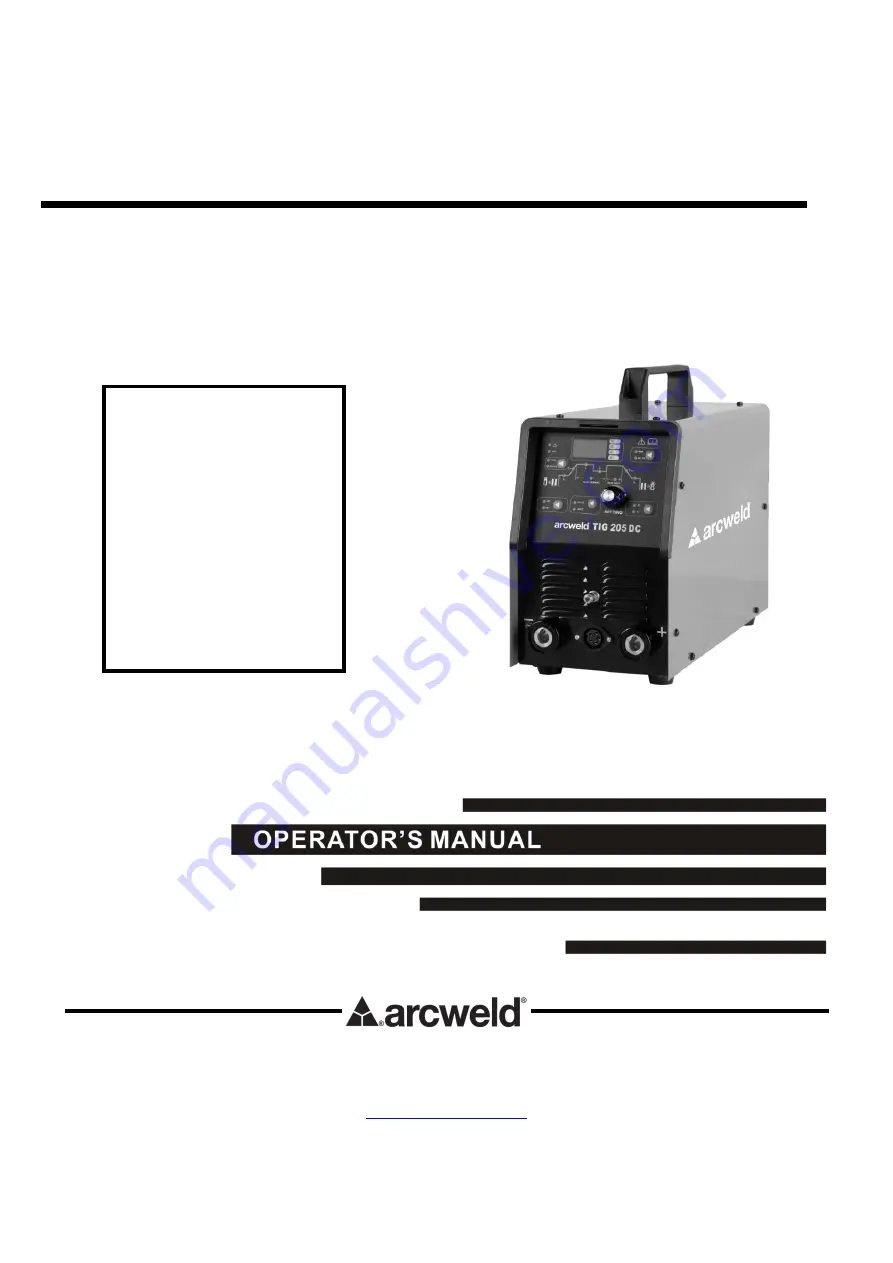
IM7907-5
Apirl. 2015
Rev. 01
arcweld
®
TIG 205 DC
For use with machine Part Number K69029-7, Code 76263
THE SHANGHAI LINCOLN ELECTRIC COMPANY
No. 195, Lane 5008, Hu Tai Rd. Baoshan, Shanghai, PRC 201907
Copyright © 2015 The Shanghai Lincoln Electric Company
Safety Depends on You
arcweld
®
machine is designed
and built with safety in mind.
However, your overall safety
can be increased by proper
installation and thoughtful
operation on your part.
DO NOT
INSTALL, OPERATE OR
REPAIR THIS EQUIPMENT
WITHOUT READING THIS
MANUAL AND THE SAFETY
PRECAUTIONS CONTAINED
THROUGHOUT.
And, most
importantly, think before you act
and be careful.
Содержание TIG 205 DC
Страница 5: ...iii SAFETY iii ...
Страница 6: ...iv SAFETY iv ...
Страница 25: ...E 1 DIAGRAM E 1 ...