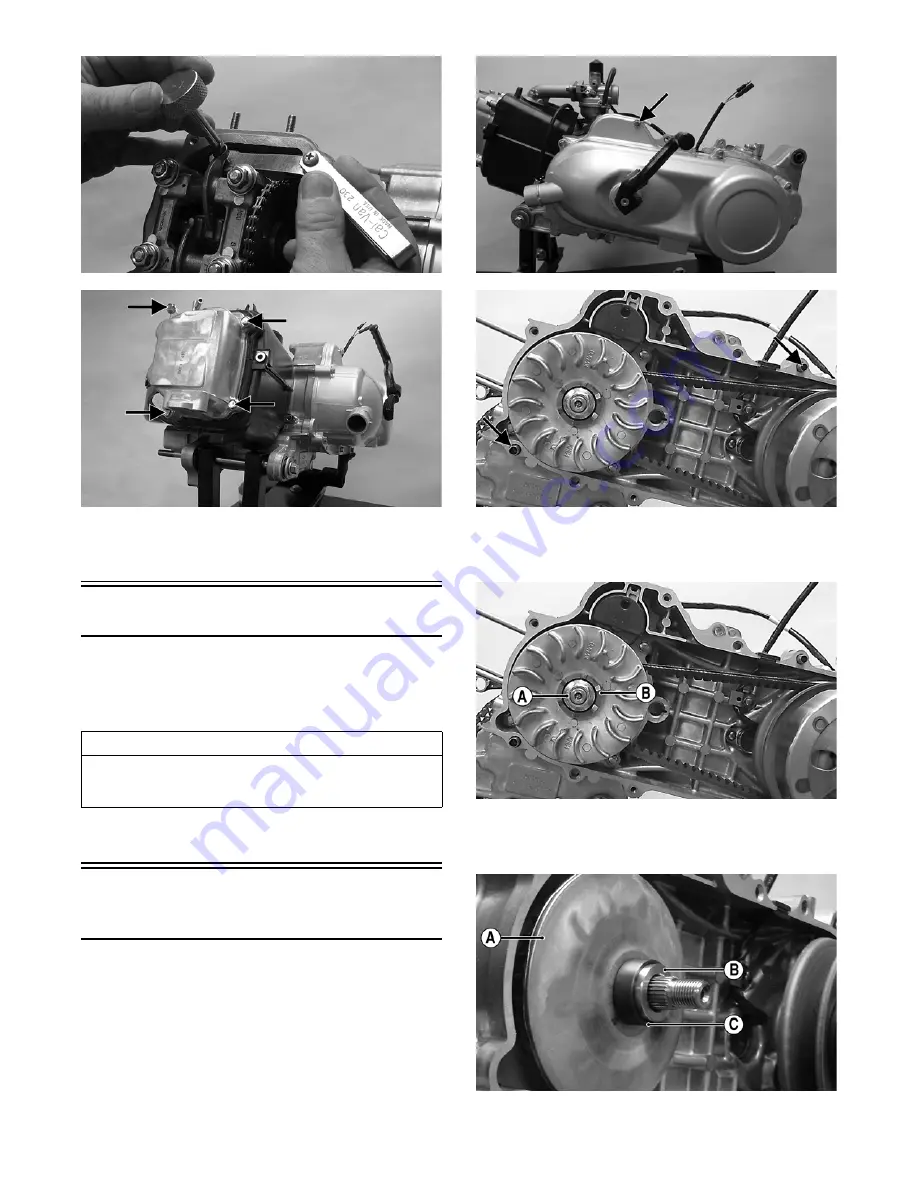
37
YT170
YT090A
13. Install the intake pipe/carburetor assembly onto the
cylinder head using a new O-ring. Tighten the flange
nuts to 7 ft-lb.
Left-Side Components
NOTE: For efficiency, it is preferable to remove and
disassemble only those components which need to be
addressed and to service only those components. The
technician should use discretion and sound judgment.
NOTE: The engine/transmission does not have to be
removed from the frame for this procedure.
Removing Left-Side
Components
A. V-BELT COVER
B. V-BELT/DRIVE CLUTCH/DRIVEN
PULLEY
C. CENTRIFUGAL CLUTCH
D. GEAR POSITION SWITCH
E. STARTER ONE-WAY CLUTCH
1. Remove the V-belt cover noting the location of the
different-lengthed cap screw and the location of the
alignment pins. Account for a gasket.
YT099A
YT160A
2. Remove the flange nut (A) securing the fixed drive
face to the crankshaft. Account for the kick-start
ratchet (B).
YT160B
3. Remove the V-belt; then remove the movable drive
face (A). Account for a bushing (B) and speed lim-
iter spacer (C).
YT021A
AT THIS POINT
To service any one specific component, only limited dis-
assembly of components may be necessary. Note the
AT THIS POINT information in each sub-section.
Содержание 2016 DVX 90
Страница 1: ...www arcticcat com SERVICE MANUAL www arcticcat com ...
Страница 83: ...82 NOTES ...