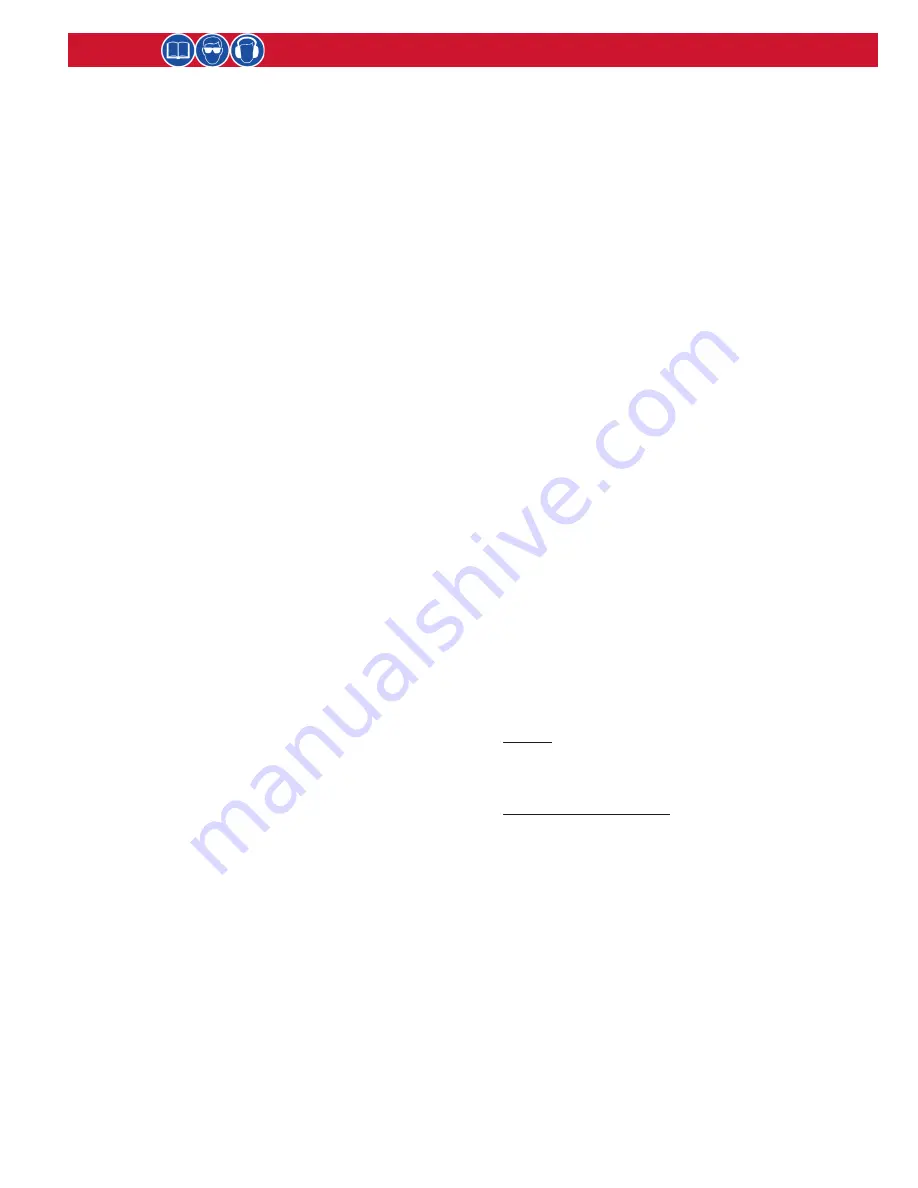
2480 & 2481 series Hydraulic Installation Tools (HK970)
19
Limited Warranties
Limited Lifetime Warranty on BobTail® Tools:
Huck International, Inc. warrants to the original purchaser
that its BobTail® installation tools manufactured after
12/1/2016 shall be free from defects in materials and
workmanship for its useful lifetime. This warranty does not
cover special order / non-standard products, or part failure
due to normal wear, tool abuse or misapplication, or user
non-compliance with the service requirements and
conditions detailed in the product literature.
Two Year Limited Warranty on Installation Tools:
Huck International, Inc. warrants that its installation tools
and Powerig® hydraulic power sources manufactured after
December 1, 2016 shall be free from defects in materials
and workmanship for a period of two years from date of
purchase by the end user. This warranty does not cover
special order / non-standard products, or part failure due
to normal wear, tool abuse or misapplication, or user non-
compliance with the service requirements and conditions
detailed in the product literature.
90 Day Limited Warranty on Nose Assemblies and
Accessories:
Huck International, Inc. warrants that its nose assemblies
and accessories shall be free from defects in materials and
workmanship for a period of 90 days from date of purchase
by the end user. This warranty does not cover special
clearance noses, or special order / non-standard product, or
part failure due to normal wear, abuse or misapplication, or
user non-compliance with the service requirements and
conditions detailed in the product literature.
Useful lifetime is defined as the period over which the
product is expected to last physically, up to the point when
replacement is required due to either normal in-service
wear, or as part of a complete overhaul. Determination is
made on a case-by case basis upon return of parts to Huck
International, Inc. for evaluation.
Tooling, Part(s) and Other Items not manufactured by
Huck:
HUCK makes no warranty with respect to the tooling,
part(s), or other items manufactured by third parties. HUCK
expressly disclaims any warranty expressed or implied, as to
the condition, design, operation, merchantability, or fitness
for use of any tool, part(s), or other items thereof not
manufactured by HUCK. HUCK shall not be liable for any
loss or damage, directly or indirectly, arising from the use
of such tooling, part(s), or other items or breach of warranty
or for any claim for incidental or consequential damages.
Huck shall not be liable for any loss or damage resulting
from delays or non-fulfillment of orders owing to strikes,
fires, accidents, transportation companies or for any reason
or reasons beyond the control of the Huck or its suppliers.
Huck Installation Equipment:
Huck International, Inc. reserves the right to make changes
in specifications and design and to discontinue models
without notice.
Huck Installation Equipment should be serviced by trained
service technicians only.
Always give the serial number of the equipment when
corresponding or ordering service parts.
Complete repair facilities are maintained by Huck
International, Inc. Please contact one of the offices listed
below.
Eastern
One Corporate Drive Kingston, New York 12401-0250
Telephone (845) 331-7300 FAX (845) 334-7333
Outside USA and Canada
Contact your nearest Huck International location (see
reverse).
In addition to the above repair facilities, there are
Authorized Tool Service Centers (ATSC’s) located
throughout the United States. These service centers offer
repair services, spare parts, Service Parts Kits, Service Tool
Kits and Nose Assemblies. Please contact your Huck
Representative or the nearest Huck International location
(see reverse) for the ATSC in your area.