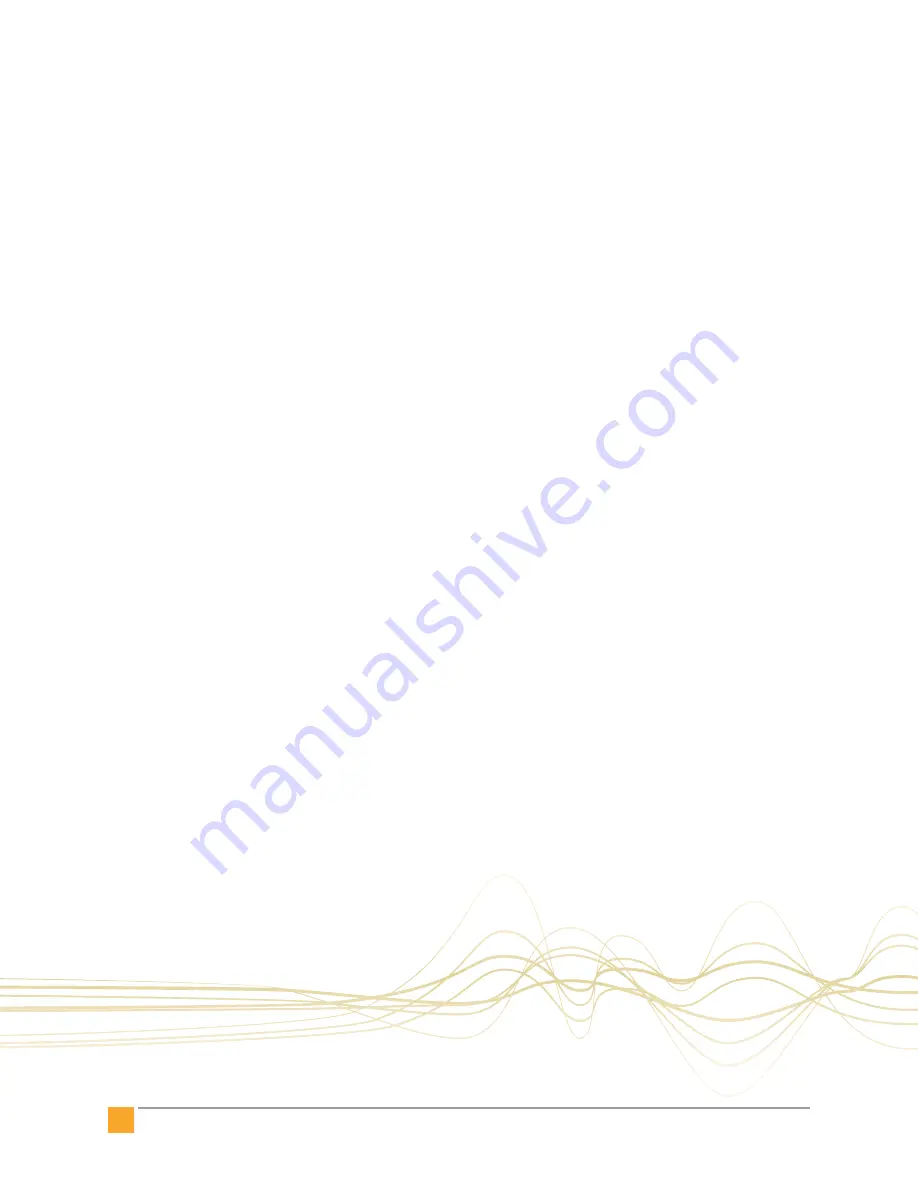
20
8 0 0 8 A N D I R I D I U M U S E R G U I D E
©2012 Indy Audio Labs, LLC all rights reserved / Revision20130220
Document No. 1000571
have current and voltage capabilities to drive even the
most difficult speaker loads with ease. High-current UL-
rated heavy-gauge wiring and internal connection points
ensure that peak supply currents are delivered to the load
with negligible internal losses. The large bifilar wound
toroids are built with virgin core material in North America
and are wound for high-current and low stray fields. In
fact, stray fields are so low that no transformer shields are
required thus improving transformer heat dissipation.
Beyond audio and power circuitry advancements over
prior Aragon designs, both the IRIDIUM and 8008 now
feature one of the most complete control integration fea-
ture sets of any amplifier in or near it’s class. Integrated
Ethernet, RS-232 and 12V trigger control capabilities
afford today’s audiophile or systems integrator state-of-
the-art design and relevance. In-home and remote di-
agnostics on these audio separates are not just possible
– these new-to-Aragon features are a revolution in sim-
plicity for both the end user and installer. All this control
and monitoring is applied with no impact on signal path
integrity since maximum audio performance was always
and still remains the main design goal for Aragon.
Aragon Housing and Material
Many amplifier designers seem to place function above
form and utilize a traditional rectangular metal housing
with a more-or-less stylized front panel to add interest.
Other designs are built around a radical new form that
more closely resembles a spacecraft from an H.G. Wells
novel than a piece of audio gear. We chose to build our
new design around the instantly recognizable V-notch
that was introduced in the original Aragon 4004, Mondial’s
first amplifier design. This design feature quickly became
the signature look for the Aragon brand. Aragon’s new
custom-tooled heat sink fins are manufactured in the USA
from precision-machined Aluminum alloy and provide
even better dissipation characteristics than the originals.
Beyond its distinctive look, the V-notch has some practi-
cal advantages that remain relevant today. In addition to
enhancing vertical convective airflow due to its broad fin
spacing, the V-notch allows for front-to-back airflow in an
equipment shelf, thus improving cooling efficiency.
The front panel is precision machined from a solid 3/4-
inch extruded Aluminum billet. Precision machining and
finishing is performed at the same Indianapolis firm that
provides critical chassis parts for a number of motor