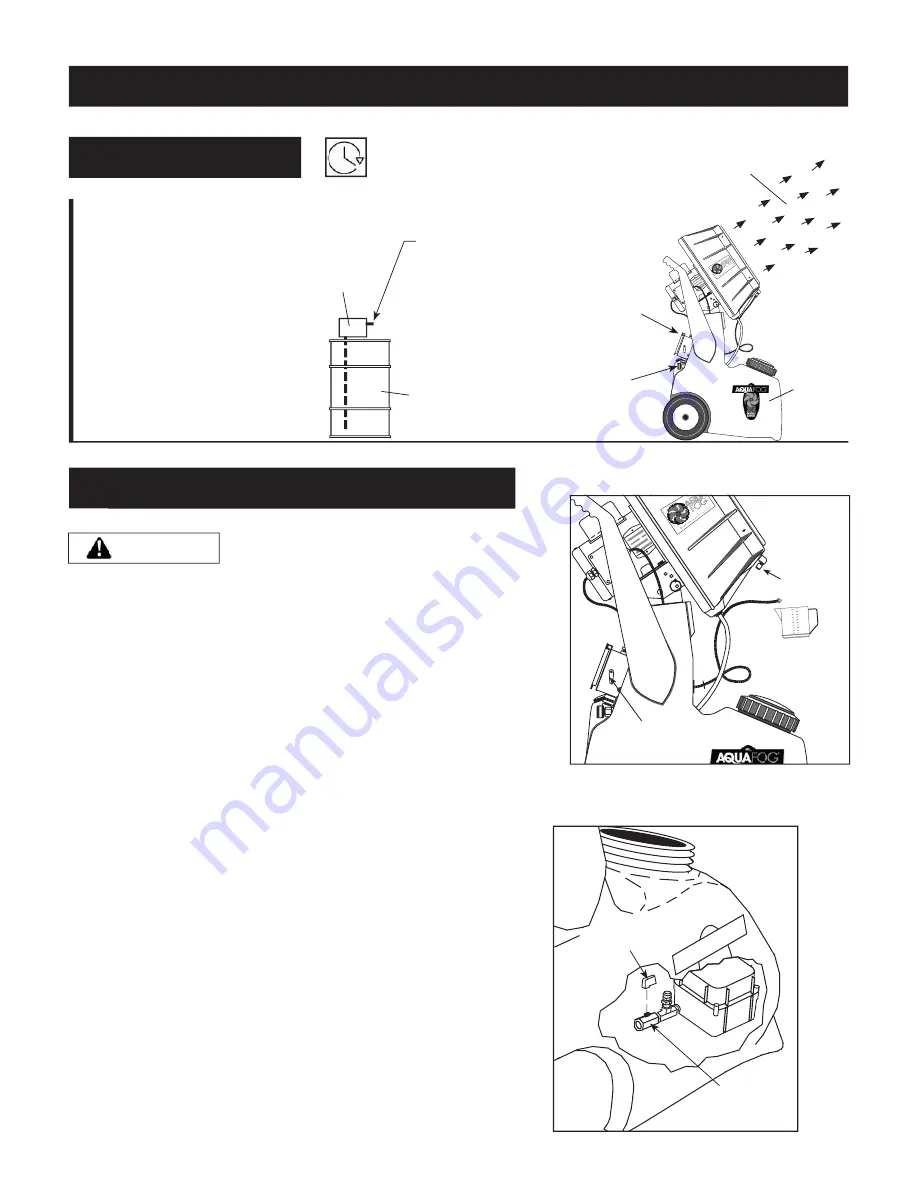
Turbo XE
R
S
M
16
14
12
10
8
6
4
2
Disconnect
to measure
KEY's Storage
Location
6
R
S
M
AQU
AFOG
Fig. 5
Fig. 6
Flow Rate
Valve
Flow Rate
Valve KEY
F
LOW
R
ATE
(F
ACTORY
P
RE
-S
ET
)
The Flow Rate (at full open) is pre-set 5 GPH
This flow rate can easily be changed to achieve customer's desired
output. Output can accommodate the odor control product being
used and customer's need to add humidity. Common outputs are:
4 to 8 GPH ~ Odor Control plus Humification Treatment
1 to 2 GPH ~ Odor Control Treatment
ORSM-1000 min/max range is 1 to 14 GPH.
ORSM-1500 min/max range is 2 to 8 GPH.
Once a flow rate has been chosen and set, connect an
appropriately-sized metering pump to add odor control product.
The KEY is needed to make changes
You will need the KEY located on the side of the electrical control
box to make changes (see
Fig. 5
). Slide this key on top of the flow
valve's stem (see
Fig. 6
) to make your adjustment.
To calibrate a New Flow Rate
Fill the unit's tank with water only and disconnect the small 1/4"
black plastic tubing at the bottom of the fan housing (See
Fig. 5
).
Use a measuring cup and turn on only the feed pump for a 60 second
interval while catching the water from the feed tube. Multiply ounces of
water by 60 and then divide by 128. This will give you your GPH rate.
Example: 1 minute/ (4.2 ozs. x 60 ÷ 128 = 2 GPH)
Do not leave KEY on valve
Regular cleaning and/or maintenance inside the tank will likely
move the setting and cause problems to your pre-set flow rate.
AUTOMATIC PRIMING OF THE SYSTEM
OCCURS THROUGH THE FLOW RATE VALVE,
SO IT SHOULD NEVER BE ADJUSTED TO FULLY CLOSED.
NOTICE
I
NSTALLATION
A) Short Treatments
For evualation(s), simply fill
the tank with some pre-diluted
product and operate manually.
B) Long Treatments
For permanent installation,
connect the ORSM to a
metering pump, to a
concentrated supply of
product, and a fresh water
source.
S
ETUP
A timer can be used to control the
power to the Metering Pump and ORSM
simultaneously.
Water Connection
Metering
Pump
Odor Control
Concentrate
The metering pump connects directly
to the ORSM, usually dosing
concentrated product at about 1 GPH
or less into the feed water traveling to
the fogging head. For location of inlet
connection see
Fig. 3
.
►
Fresh
Water
Storage
Atomized
Mixture