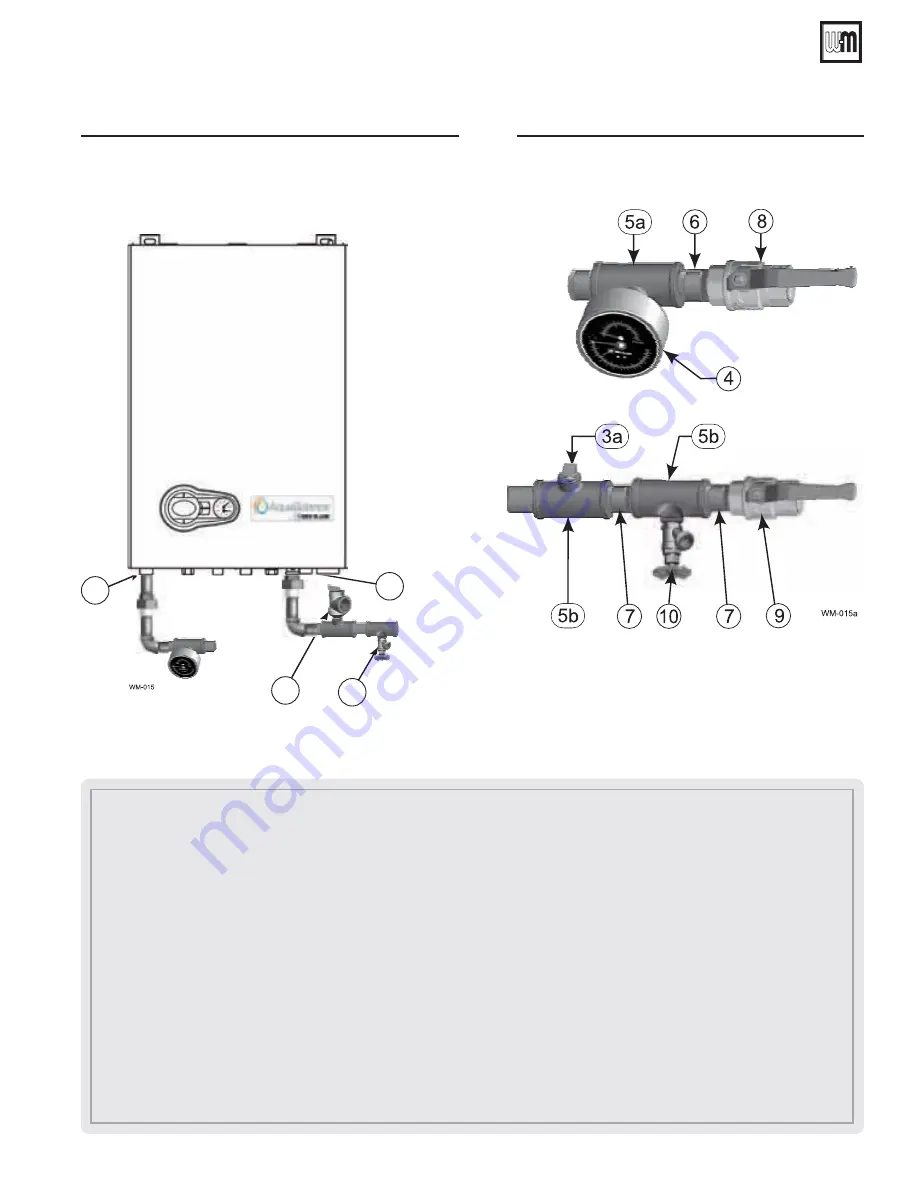
Figure 7
)NSTALLPIPINGCOMPONENTSREQUIREDFOR
HYDROSTATICTEST
see legend below)
Part number 550-100-305/0916
11
AquaBalance
TM
W
ALL
M
OUNT
GAS
-
FIRED
WATER
BOILER
— C
OMBI
Boiler Manual
1. Boiler Supply (outlet) connection, (male,
1”NPT ).
2. Boiler Return (inlet) connection, (male,
1”NPT).
Recommend Near Boiler Piping to be 1-1/4” NPT or larger. Bushing 1” x 1-1/4” NPT at Supply (outlet) and Return (inlet) not
shown.
(
field supplied
by installer
)
3. Boiler relief valve, shipped loose with boiler —
$/./4MOUNTRELIEFVALVEUNTIL!&4%2HYDROSTATICTESTING
.
3a.
4%-0/2!2),9/.,9
Insert a ¾” NPT plug in the relief valve tapping of the reducing tee.
4HIS-534"%2%-/6%$
after the test and the relief valve mounted here
.
4. Pressure/temperature
gauge,
(
field supplied)
by installer, (Optional – can use boiler gauge).
5a. Reducing tee, NPT, 1
-1/4
” x 1
-1/4
” x ¼”
(
field supplied)
by installer .
5b. Tee, NPT, 1
-1/4
” x 1
-1/4
” x ¾”
(
field supplied)
by installer.
6. Nipple, NPT, 1
-1/4
” x close
(
field supplied)
by installer.
7. Nipple, NPT, 1
-1/4
” x close
(
field supplied)
by installer.
8. Isolation valve on supply connection,
(
field supplied)
by installer (
1-1/4”NPT).
9. Isolation valve on return connection,
(
field supplied)
by installer (
1-1/4”NPT).
10. ¾” NPT boiler drain valve,
(
field supplied)
by installer — after hydrostatic testing, move drain valve to lowest point on the return piping
if not already there.
3 Prepare boiler
continued
Figure 6
)NSTALLPIPElTTINGSFORRELIEFVALVEANDPRESSURE
TEMPERATUREGAUGE
$/./4MOUNTRELIEF
VALVEUNTIL!&4%2HYDROSTATICTESTING
(see
legend below)
"OILER2ETURN
INLET
"OILER3UPPLY
OUTLET
2
3
1
10