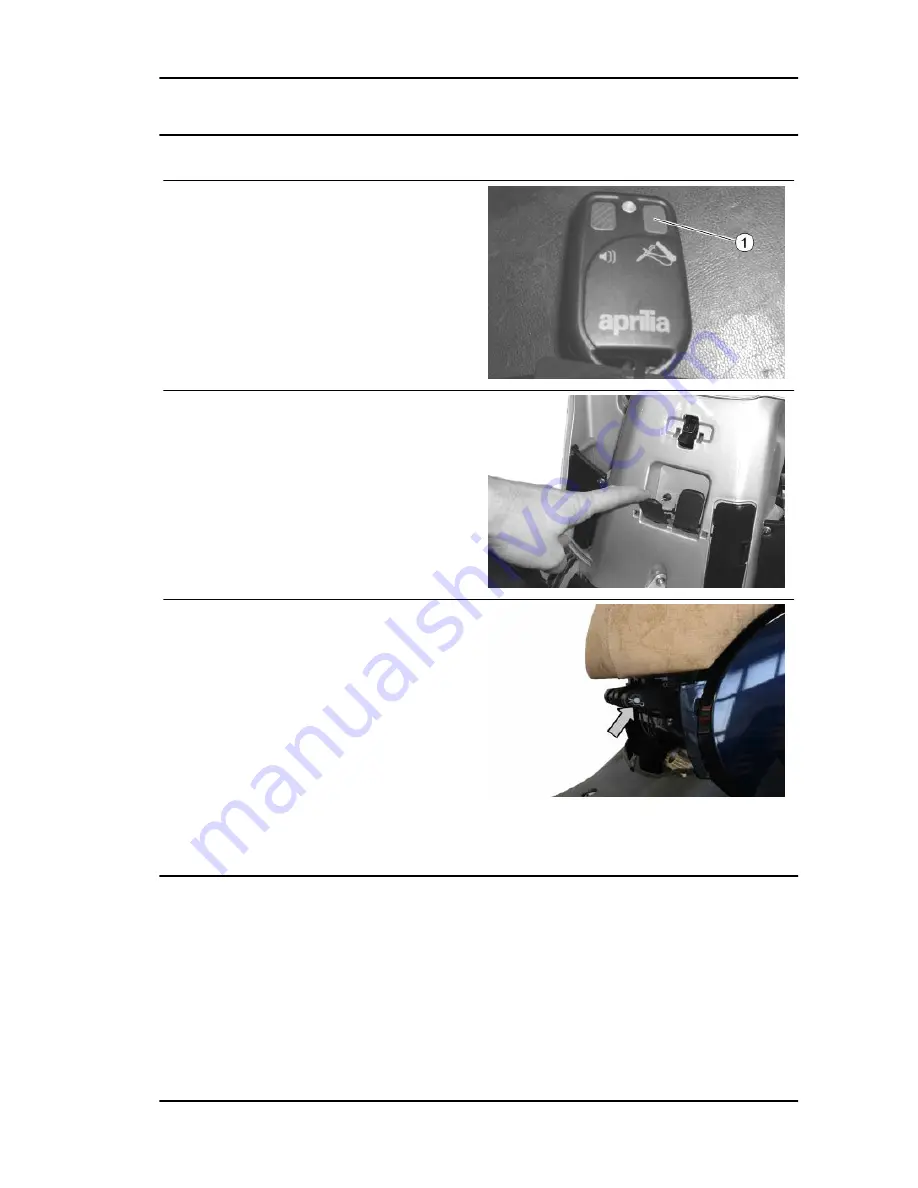
Seat
It is necessary to lift the saddle before removing it.
There are two ways to do so:
•
use the supplied remote control, press
the key «1» and the saddle will open
automatically.
•
Insert the key in the key lock and press
down. The glove-box opens automati-
cally. Pull the left lever to open the
saddle manually.
•
Lift the saddle.
•
Remove the central inspection cover.
•
Remove the cotter pin and collect the
washer.
•
Slide off the pin.
•
Remove the saddle.
SCARABEO 500
Chassis
CHAS - 301
Содержание SCARABEO 500 - 2008
Страница 1: ...SERVICE STATION MANUAL 854190 SCARABEO 500...
Страница 4: ......
Страница 6: ...INDEX OF TOPICS CHARACTERISTICS CHAR...
Страница 30: ...INDEX OF TOPICS TOOLING TOOL...
Страница 41: ...INDEX OF TOPICS MAINTENANCE MAIN...
Страница 63: ...INDEX OF TOPICS ELECTRICAL SYSTEM ELE SYS...
Страница 64: ...Components arrangement Electrical system SCARABEO 500 ELE SYS 64...
Страница 73: ...KEY 1 Do not use any clamps 2 290x4 5 Clamp SCARABEO 500 Electrical system ELE SYS 73...
Страница 77: ...KEY 1 Cable guide plus a clamp 2 98x2 5 Clamp SCARABEO 500 Electrical system ELE SYS 77...
Страница 78: ...KEY 1 98x2 5 Clamp 2 98x2 5 Clamp 3 98x2 5 Clamp KEY Electrical system SCARABEO 500 ELE SYS 78...
Страница 80: ...KEY 1 98x2 5 Clamp LEFT LIGHT SWITCH KEY 1 98x2 5 Clamp Electrical system SCARABEO 500 ELE SYS 80...
Страница 81: ...SPEED SENSOR FITTING KEY 1 98x2 5 Clamp 2 98x2 5 Clamp 3 98x2 5 Clamp SCARABEO 500 Electrical system ELE SYS 81...
Страница 102: ...INDEX OF TOPICS ENGINE FROM VEHICLE ENG VE...
Страница 117: ...INDEX OF TOPICS ENGINE ENG...
Страница 228: ...INDEX OF TOPICS INJECTION INJEC...
Страница 241: ...Remove the MIU control unit connector Remove throttle control retainer SCARABEO 500 Injection INJEC 241...
Страница 263: ...INDEX OF TOPICS SUSPENSIONS SUSP...
Страница 281: ...INDEX OF TOPICS BRAKING SYSTEM BRAK SYS...
Страница 293: ...INDEX OF TOPICS COOLING SYSTEM COOL SYS...
Страница 299: ...2 Check the head gasket seal see the Thermal group and Timing system chapter SCARABEO 500 Cooling system COOL SYS 299...
Страница 300: ...INDEX OF TOPICS CHASSIS CHAS...
Страница 321: ...INDEX OF TOPICS PRE DELIVERY PRE DE...