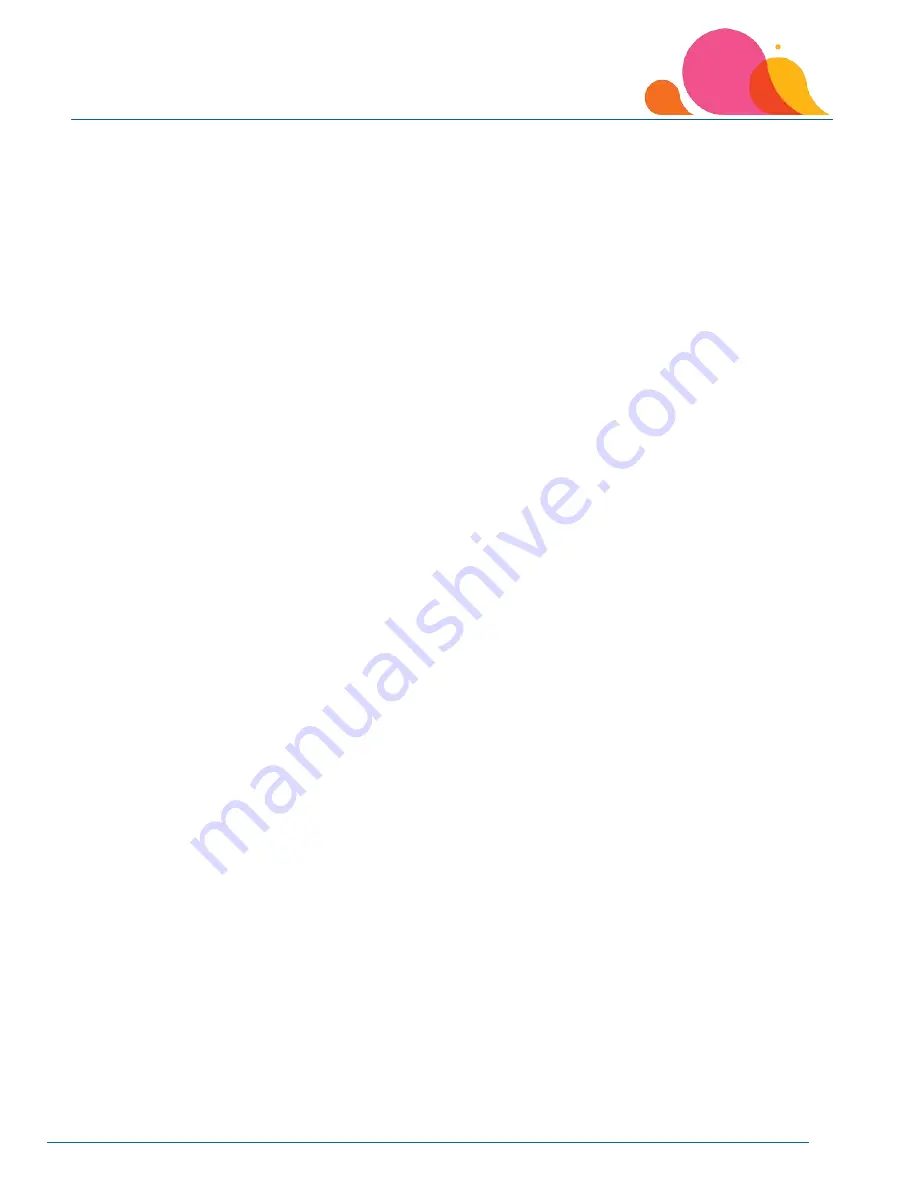
8
8-1-2021
APQS.com
Lenni – Lucey Standard Table Manual
General Assembly Order
Your new quilting machine is not difficult to assemble. It can usually be accomplished in just a few hours. While the basic
assembly is possible alone, extra hands are very helpful throughout the process.
Assembly Process Overview
1.
Add the rear Aluminum Table Rail to the two Table Legs
If installing optional casters, put them on before this step
2.
Install the Rail Cross Tubes.
3.
Add the front Aluminum Table Rail to the two Table Legs
If installing optional Quilt Path, Overhead Lighting or a Hydraulic Lift, add those BEFORE installing the Table Top.
4.
Install the Tabletop pads and bumpers, then add the Table Top
5.
Assemble and mount the Carriage
6.
Assemble and install the Sewing Head
7.
Install the Pick-Up Roller and Leveler Bar
8.
Deluxe or Standard Table
9.
Deluxe Table - add the optional Auto Quilt Advance
10.
Standard Table - install one Roller Brake
11.
Install the Quilt Top and Quilt Backing Rollers
12.
Add the Roller Brake to these two Rollers
13.
Complete the electrical connections
Содержание Lenni
Страница 71: ...71 5 2 2020 APQS com Daily Maintenance ...