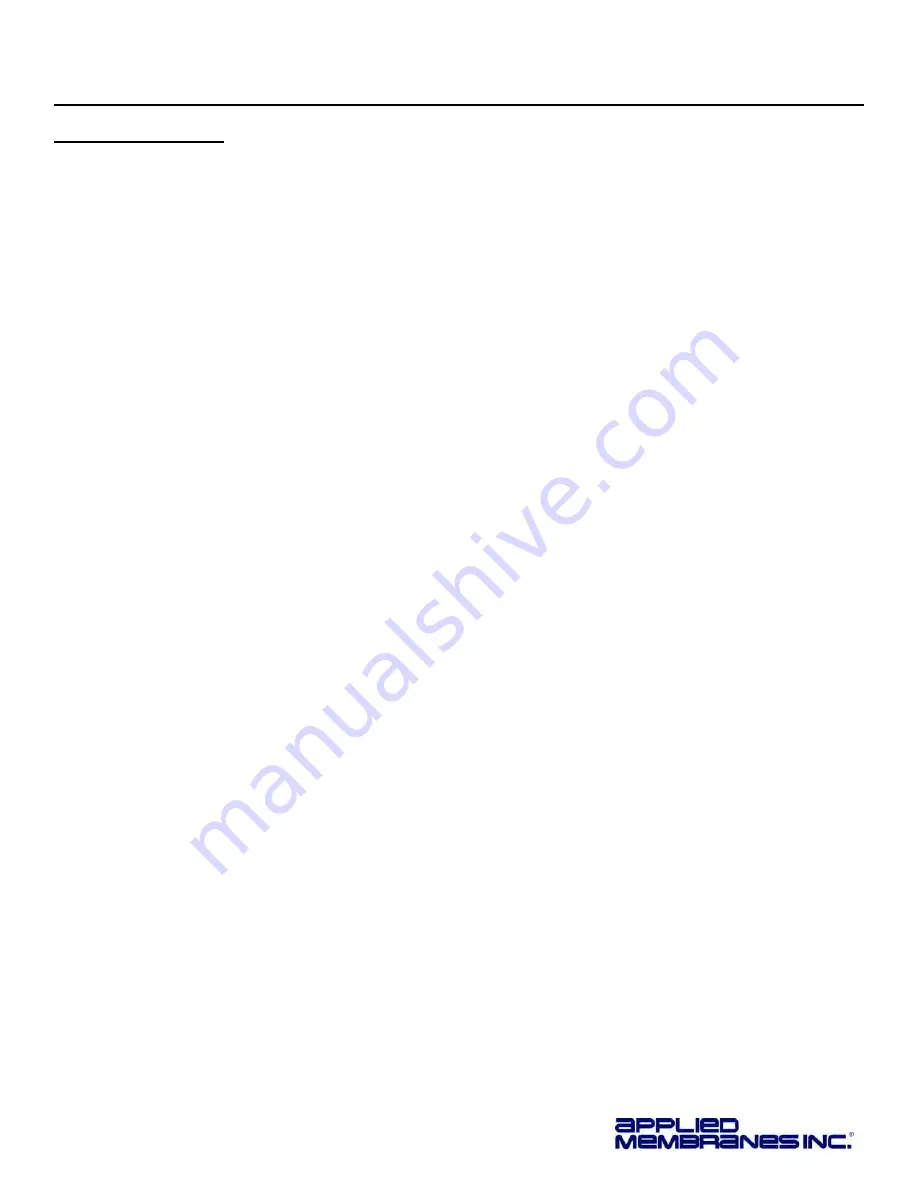
Installation and Service Manual – Metered Carbon Filter
Page 34
Copyright © 2012 Applied Membranes, Inc. All Rights Reserved.
Control
Valve
Service
Instructions
Drive Assembly
Remove the valve cover to access the drive assembly.
Disconnect the power source plug (black wire) from the PC board prior to disconnecting the motor or water meter plugs
from the PC board. The power source plug connects to the four-pin jack. The motor plug connects to the two-pin jack on
the left-hand side of the PC board. The water meter plug (gray wire) connects to the three-pin jack on the far right-hand
side of the PC board.
The PC board can be removed separately from the drive bracket but it is not recommended. Do not attempt to remove the
display panel from the PC board. Handle the board by the edges. To remove the PC board from the drive bracket, unplug
the power, water meter and motor plugs from the PC board. Lift the middle latch along the top of the drive bracket while
pulling outward on the top of the PC board. The drive bracket has two plastic pins that fi t into the holes on the lower edge
of the PC board. Once the PC board is tilted about 45° from the drive bracket it can be lifted off of these pins. To reinstall
the PC board, position the lower edge of the PC board so that the holes in the PC board line up with the plastic pins. Push
the top of the PC board towards the valve until it snaps under the middle latch, weave the power and water meter wires
into the holders and reconnect the motor, water meter and power plugs.
The drive bracket must be removed to access the drive cap assembly and pistons or the drive gear cover. It is not
necessary to remove the PC board from the drive bracket to remove the drive bracket. To remove the drive bracket start
by removing the plugs for the power source and the water meter. Unweave the wires from the side holders. Two tabs on
the top of the drive back plate hold the drive bracket in place. Simultaneously lift the two tabs and gently ease the top of
the drive bracket forward. The lower edge of the drive bracket has two notches that rest on the drive back plate. Lift up
and outward on the drive bracket to disengage the notches.
To reassemble, seat the bottom of the drive bracket so the notches are engaged at the bottom of the drive back plate.
Push the top of the drive bracket toward the two latches. The drive bracket may have to be lifted slightly to let the
threaded piston rod pass through the hole in the drive bracket. Maintain a slight engaging force on top of the drive bracket
while deflecting the bracket slightly to the left by pressing on the side of the upper right corner. This helps the drive gears
mesh with the drive cap assembly. The drive bracket is properly seated when it snaps under the latches on the drive back
plate. If resistance is felt before latching, then notches are not fully engaged, the piston rod is not in hole, the wires are
jammed between the drive bracket and drive back plate, or the gear is not engaging the drive cap assembly.
To inspect the drive gears, the drive gear cover needs to be removed. Before trying to remove the gear cover, the drive
bracket must be removed from the drive back plate. (Refer to the instructions above regarding removing the drive bracket
from the drive back plate. The drive gear cover can be removed from the drive bracket without removing the motor or the
PC board.) The drive gear cover is held in place on the drive bracket by three clips. The largest of the three clips is always
orientated to the bottom of the drive bracket. With the PC board facing up, push in and down on the large clip on the drive
gear cover. Handle the cover and the gears carefully so that the gears do not fall off the pegs in the cover. Replace
broken or damaged drive gears. Do not lubricate any of the gears. Avoid getting any foreign matter on the reflective
coating because dirt or oils may interfere with pulse counting.
The drive gear cover only fits on one way, with the large clip orientated towards the bottom. If all three clips are outside of
the gear shroud on the drive bracket the drive gear cover slips easily into place.
The drive bracket does not need to be removed from the drive plate if the motor needs to be removed. To remove the
motor, disconnect the power and motor plugs from the jacks on the PC board. Move the spring clip loop to the right and
hold. Rotate the motor at least a ¼ turn in either direction so the wires are vertical (up & down) before gently pulling on the
wire connectors to remove the motor. Pulling directly on the wires without rotating the motor may break the wires off the
motor.
Replace the motor if necessary. Do not lubricate the motor or the gears. To reinstall the motor, move the spring clip loop
to the right and hold. Gently turn the motor while inserting so that the gear on the motor meshes with the gears under the
drive gear cover. Release the spring clip loop and continue to rotate the motor until the wires are horizontal and the motor
housing engages the small plastic bulge inside the drive bracket motor retainer. Reconnect the motor plug to the two-
pronged jack on the lower left side of the PC board. If the motor will not easily engage with the drive gears when
reinstalling, lift and slightly rotate the motor before reinserting. Reconnect the power plug.