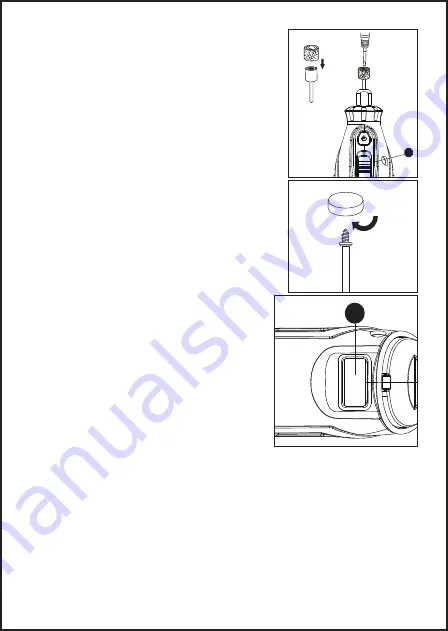
d)
e)
f)
g)
5)
Safety instructions for all operations
Safety warnings common for grinding, sanding, wire brushing, polishing, carving or
abrasive cutting-off operations:
a)
NOTE List only those operations that are applicable.
NOTE List only those operations that were not included in the first warning. If all
listed operations are applicable, then this warning is omitted, but all subsequent
warnings are given without exclusion.
b)
c)
d)
e)
c)
d)
e)
3)
a)
b)
c)
d)
e)
f)
g)
4)
a)
b)
c)
Removing Accessories
Using Mandrels
The most common types of mandrel to use with this tool are the standard mandrel
which is used with cutoff discs, grinding wheels, emery wheels, and cut-off wheels.
Screw mandrels are used with polishing wheels and polishing drums. Drum mandrel
are used with sanding drums.
To install:
●
●
If using the standard mandrel:
●
NOTE: The mandrel washer should be placed between the mandrel screw and the
accessory.
●
f)
g)
h)
i)
j)
k)
l)
m)
n)
o)
Know Your Rotary Tool
Before attempting to use any tool, familiarize yourself with all operating features and
safety requirements.See Fig. 1.
Safety instructions
Warning: read all safety warnings and all instructions. Failure to follow the
warnings and instructions may result in electric shock, fire and / or serious injury.
Save all warnings and instructions for future reference.
1)
a)
b)
c)
2)
a)
b)
p)
q)
r)
s)
Further safety instructions for all operations
Kickback and related warnings
Kickback is a sudden reaction to a pinched or snagged rotating wheel, sanding
band, brush or any other accessory. Pinching or snagging causes rapid stalling of
the rotating accessory which in turn causes the uncontrolled power tool to be forced
in the direction opposite of the accessory’s rotation.
For example, if an abrasive wheel is snagged or pinched by the workpiece, the edge
of the wheel that is entering into the pinch point can dig into the surface of the
material causing the wheel to climb out or kick out. The wheel may either jump
toward or away from the operator, depending on direction of the wheel’s move- ment
at the point of pinching. Abrasive wheels may also break under these conditions.
Kickback is the result of power tool misuse and/or incorrect operating procedures or
conditions and can be avoided by taking proper precautions as given below.
a)
b)
c)
d)
e)
Additional safety instructions for grinding and cutting-off
operations
Safety warnings specific for grinding and abrasive
cutting-off operations:
a)
b)
c)
d)
e)
f)
g)
h)
Additional safety instructions for wire brushing operations
Safety warnings specific for wire brushing operations:
a)
b)
c)
TECHNICAL SPECIFICATIONS
WARNING
Always wear eye protection when using this tool. Failure to do that could result in
objects being thrown into your eyes and cause possible serious injury.
WARNING
Do not use any attachments or accessories not recommended by the manufacturer
of this product. The use of attachments or accessories not recommended can result
in serious personal injury.
Applications
You may use this product for the purposes listed below:
●
●
●
●
●
Functions Description
On / Off Switch
Replacing Collets
Using collets is the most precise way to hold an accessory in a high speed rotating.
Even at high speeds and maximum pressure, collets stay tight.
Installing Accessories
WARNING
Do not press the shaft lock button (E) while rotary tool is running.
●
●
●
●
If using the drum mandrel:
●
Align appropriate sized sanding drum over
mandrel and push down to completely cover drum
end of mandrel.
●
Insert the slot end of the provided wrench into the
slot on top of the mandre and tighten the screw on
the drum mandrel head to expand the drum and
securely hold the sanding drum in place.
If using the screw mandrel:
●
Align desired accessory hole with mandrel screw
head.
●
Screw accessory onto mandrel by twisting
clockwise until secure.
Balancing Accessories
For precision work, it is important that all accesso-
ries be properly balanced. To balance an accesso-
ry, slightly loosen the collet nut and give the
accessory or collet a 1/4 in. turn.
Retighten collet nut and run the rotary tool. You
should be able to judge by the sound and feel if the
accessory is running in balance. Continue
adjusting in this fashion until the best balance is
achieved. Replace accessories if they become
damaged or unbalanced.
Speed Control
The rotary tool has a speed range of 10000 to
35,000 RPM. To select the right speed for each
job, use a practice piece of material.
Rules of Operating Speeds
The best way to determine the correct speed for work on any material is to practice
for a few minutes on a piece of scrap, even after referring to the Speed Dial Settings
tables. You can quickly learn that a slower or faster speed is more effective just by
observing what happens when you make a pass or two at different speeds.
When working with a scrap piece of plastic, start at a slow rate of speed and increase
the speed until you observe whether the plastic is melting at the point of contact;
reduce the speed slightly to get optimum working speed without melting the
workpiece.
Certain materials, some plastics for example, require a relatively slow speed
because at high speed the friction of the tool generates heat and causes the plastic
to melt.
Slow speed operation (15,000 RPM or less) is usually best for polishing operations
using the felt polishing accessories, delicate wood carving and fragile model parts.
All brush applications require lower speeds to avoid wire discharge from the holder.
Allow the tool to do the work for you when using lower speed settings.
Higher speeds are better for drilling, carving, cutting, routing, shaping, and cutting
dadoes or rabbets in wood. Hardwoods, metals and glass also require high speed
operation.
NOTE:
●
●
●
Detailer’s Grip Attachment
Installation Instructions
1.
2.
Vary speed to find the best speed for the accessory you are using and the job to be
done. Use the indicator mark above the speed control dial (H) to set the best speed
for the job. The speed control dial (H) is numbered
from 1 to Max. For example, a speed setting of 1 is approximately 10,000 RPM, and
a speed setting of Max is approximately 35,000 RPM.
Refer to the Speed Dial Settings table to determine the proper speed based on the
material being worked and the type of accessory being used.
Step 2.
Step 3.
Using the Shield Rotary Tool Attachment:
Always turn the tool off before adjusting position, changing accessory and removing
attachment. Rotary Tools cut, sand, grind, and polish in many directions. To
accommodate the Rotary Tool’s Maneuverability, the Shield can be quickly
positioned and repositioned with a turn to the right or left .To extend the life of the
Shield periodically clean with a soft bristle brush or compressed air.
Flexible Driver Attachment
Safety Rules for Flexible Driver
Driver to disengage from the tool. The minimum recommended bend radius is 6”
(
15CM
)
.
Always hold the hand piece firmly in your hands during the start-up. The reaction
torque of the motor, as it accelerates to full speed, can cause the shaft to twist.
Not for use with router bits or other large diameters (1” or larger) bits. Large diame-
ter bits can cause kickback and loss of control when used with the Flexible Driver.
Do not remove end ferrule while tool is running. The cable will become loose from
the jacket and will uncontrollably whip or lash around.
Installation Instructions
It is extremely important to carefully read and follow the directions below to
assemble the Flexible Driver to your rotary to ensure the tool will function properly.
Operating Instructions
it back into the shaft. To prevent damage to tool do not over grease shaft.
Too much grease will cause the unit to overheat. Reattach the Flexible Driver to the
rotary tool.
Cleaning, maintenance
Always pull out the mains power plug before starting any cleaning work.
Cleaning
●Keep all safety devices, air vents and the motor housing free of dirt and dust as far
as possible.
Wipe the equipment with a clean cloth or blow
●it with compressed air at low pressure.
We recommend that you clean the device immediately each time you
●have finished using it.
Clean the equipment regularly with a moist cloth and some soft soap. Do not use
cleaning agents or solvents; these could attack the plastic parts of the equipment.
Ensure that no water can seep into the device.
Maintenance
There are no parts inside the equipment which require additional maintenance.
Environmental Protection
- 10 -
E
H