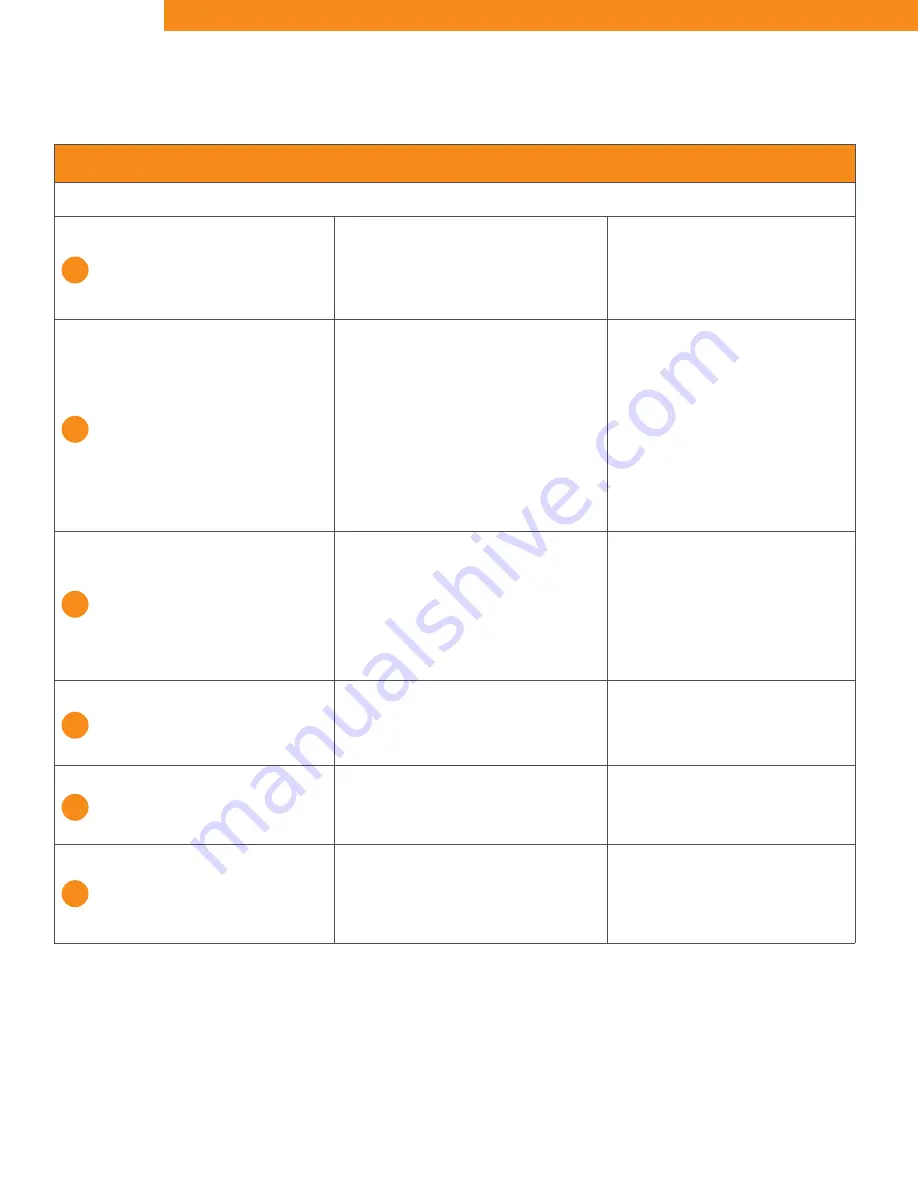
1007 & 3007 ROLL GROOVER
22
TROUBLESHOOTING
TROUBLESHOOTING INSTRUCTIONS
Problem
Possible Cause
Solution
1.
Pipe will not stay in grooving rolls.
Incorrect pipe positioning.
Improper grooving technique.
Power drive running counterclockwise
Model 3007.
See "Pipe Set-up & Positioning"
See "Grooving Pipe"
Ridgid 300 check setting in reverse
Clockwise rotation of pipe
2.
Pipe stops rotating during grooving.
Rust or dirt has built up on lower roll.
Worn grooving rolls.
Ridgid 300 chuck jaws not engaged
properly.
Steel Pipe – Groove Diameter Stop
improperly adjusted.
Copper Tube – Groove Diameter Stop making
contact with top surface of Groover.
Remove accumulation from lower roll
with stiff wire brush.
Inspect lower rolls for worn knurls,
replace if worn.
See "Groover Set-up"
Adjust Groove Diameter Stop to
correct IPS.
Verify Groove Diameter Stop Nuts are
fully backed off.
3.
Pipe flare excessive
Pipe stand adjusted too high.
Tool is tilted forward.
Incorrect pipe stand offset positioning. Pipe is
over "tracking".
Warped bottom roll shaft.
See "Pipe Set-up & Positioning"
See "Groover Set-up"
See "Pipe Set-up & Positioning"
Replace damaged bottom roll shaft.
The hinged collar may be missing.
Replace damaged parts.
4
.
While grooving loud squeaks echo
through the pipe or tube.
Pipe or Tube not square cut.
Incorrect pipe roller offset positioning.
Pipe is over "tracking".
Cut pipe or tube ends squarely.
Move pipe stand for proper offset.
See "Pipe Set-up & Positioning"
5
.
During grooving loud thumps or bangs
occur about once every revolution of
the pipe.
Pipe has a pronounced weld seam.
Grind welds flush with pipe surface inside
& out 2" back from pipe end.
6
.
Tool won't groove pipe.
Hand pump is low on oil.
Air in hydraulic system.
Pipe wall thickness exceeds tool's capability.
See "Groover Maintenance"
See "Groover Maintenance"
See "Groover Description"
1
2
3
4
5
6