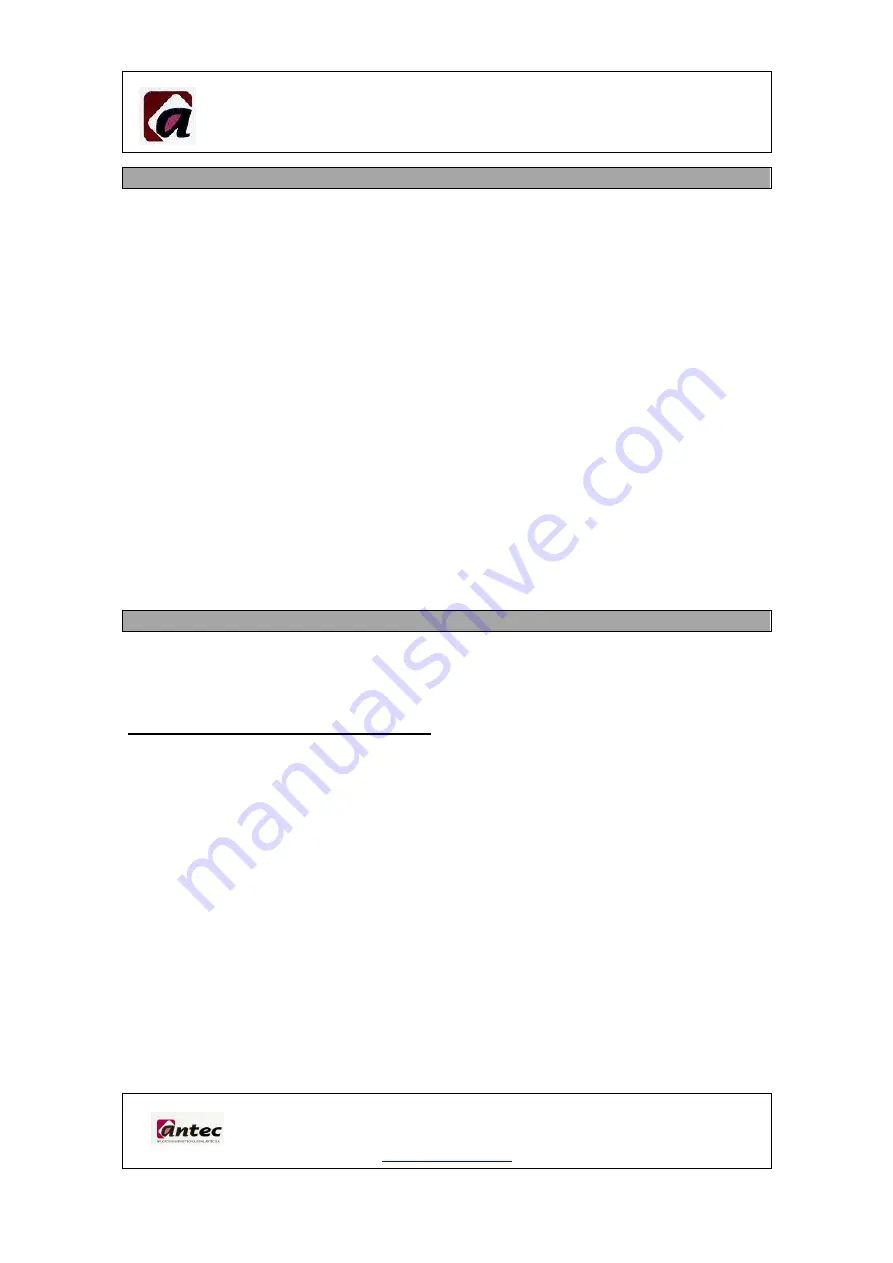
HYDRAULIC CALLIPER TYPE NHCD-1400
Instructions for assembly, adjustment and maintenance
T.D.S.: BC.TDS.00025I
Rev.0.: September - 2012
3
. BRAKE MAINTENANCE.
NHCD-1400 brake maintenance will consist of regularly checking the following
points:
3.1 – Lining wear. When the lining thickness drops below 2 mm at the thinnest point, it
needs to be replaced. If the brake comes with a wear sensor (optional), replace the
linings when the sensor warning comes on. See point 4.2 (adjustment of detectors) and
point 5 (linings change).
3.2 – Adjust the brake whenever it displays a loss of force. If the brake comes with a
wear sensor (optional), adjust the brake when the sensor warning comes on. See point
4.1. (adjustment of the calliper opening).
3.3. - Check the torque of the stopper screws and the fastening screws of the brake to
any of the brackets. See the blueprint of the brake supplied with the documentation sent
by Antec.
3.4. - Check that there is no leakage in the hydraulic connections.
4. ADJUSTING THE BRAKE.
The brake has two unique adjustment points:
4.1. - Adjustment of the calliper opening.
The explanation of the adjustment of the calliper opening will be given for one of the
two semi-callipers. and is the same for the other.
4.1.1
Feed the semi-calliper with the related hydraulic pressure for each brake, as
shown in the attached table in point 1.3. of the instructions. At this pressure the
brake will be opened to the utmost.
4.1.2
Dismantle the bracket of the sensors (marked 9) with their bolts and washers
(marked 30-31) and the sensor (36). Loosen the nut (marked 19) up until the end
of the bolt, enough to free up the adjustment screw (marked 5). Dismantle the
locking backstop (6).