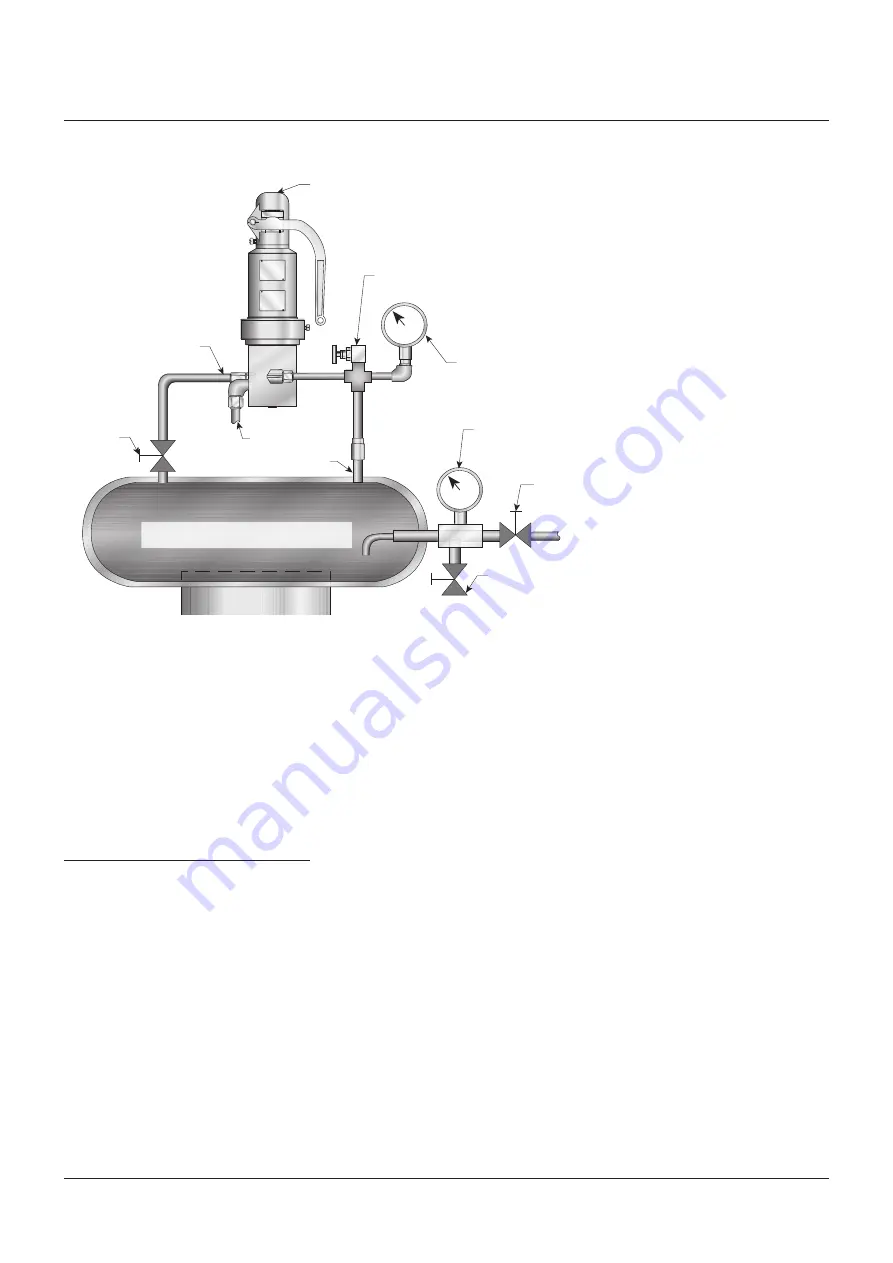
13
Anderson Greenwood
SerieS 5200 POSrV
InstallatIon and MaIntenance InstructIons
FiGUre 10 – PiLOT ADJUSTMeNT STeAM TeST SeT-UP
Set pressure adjustment
(Turn in to increase set pressure)
(Turn out to decrease set pressure)
Bleed valve
Dome pressure gauge
Supply pressure
gauge
Block valve
Air
supply
Vent valve
Shut-off
valve
Accumulator (approx. ¼ cu ft)
Flexible hose
(to inlet port)
Pilot exhaust port
Mounting stub (solid)
6.3 range of adjustment
All pilots can be adjusted ± 5% beyond the
nameplate setting. if a set pressure change is
made that requires a new spring, consult the
factory for information contained in the spring
chart.
6.4 performance requirements, pilot only
Pilot crack pressure must be at least 95%
of set pressure. refer to performance
requirements, Section 7.5, for set pressure
tolerance and reseat pressures.
7 VAlVe AsseMbly TesTInG
7.1 General
The complete valve assembly must be tested
for leakage. The test medium should be steam.
7.2 Set pressure check
Slowly increase pressure to the valve inlet until
the first audible discharge is detected. This is
set pressure. Adjust set pressure as required
to meet the performance requirements of
Section 7.5.
note:
Clockwise rotation of pressure adjusting
bolt increases the relief pressure. Tighten the
locknut after adjustment is completed.
7.3 Leakage check
note:
Actuate the valve a minimum of 2 times
prior to testing the pilot for seat leakage.
7.3.1
Seat tightness test must be conducted at
maximum of 95% of nameplate set pressure,
but not to exceed the reseating pressure of
the valve. When being tested, a valve exhibiting
no visible signs of leakage will be considered
adequately tight.
7.3.2
There should be no visible signs of
external leakage (through any fittings or joints)
at 90% of nameplate set pressure.
7.4 Back pressure test
The secondary zone should be pressure tested
on air at 30 psig minimum. if applicable, plug
the body drain fitting port. There must be no
visible sign of leakage at the body drain fitting
or at the pilot exhaust tubing and fittings. After
test, if applicable, remove drain fitting plug.