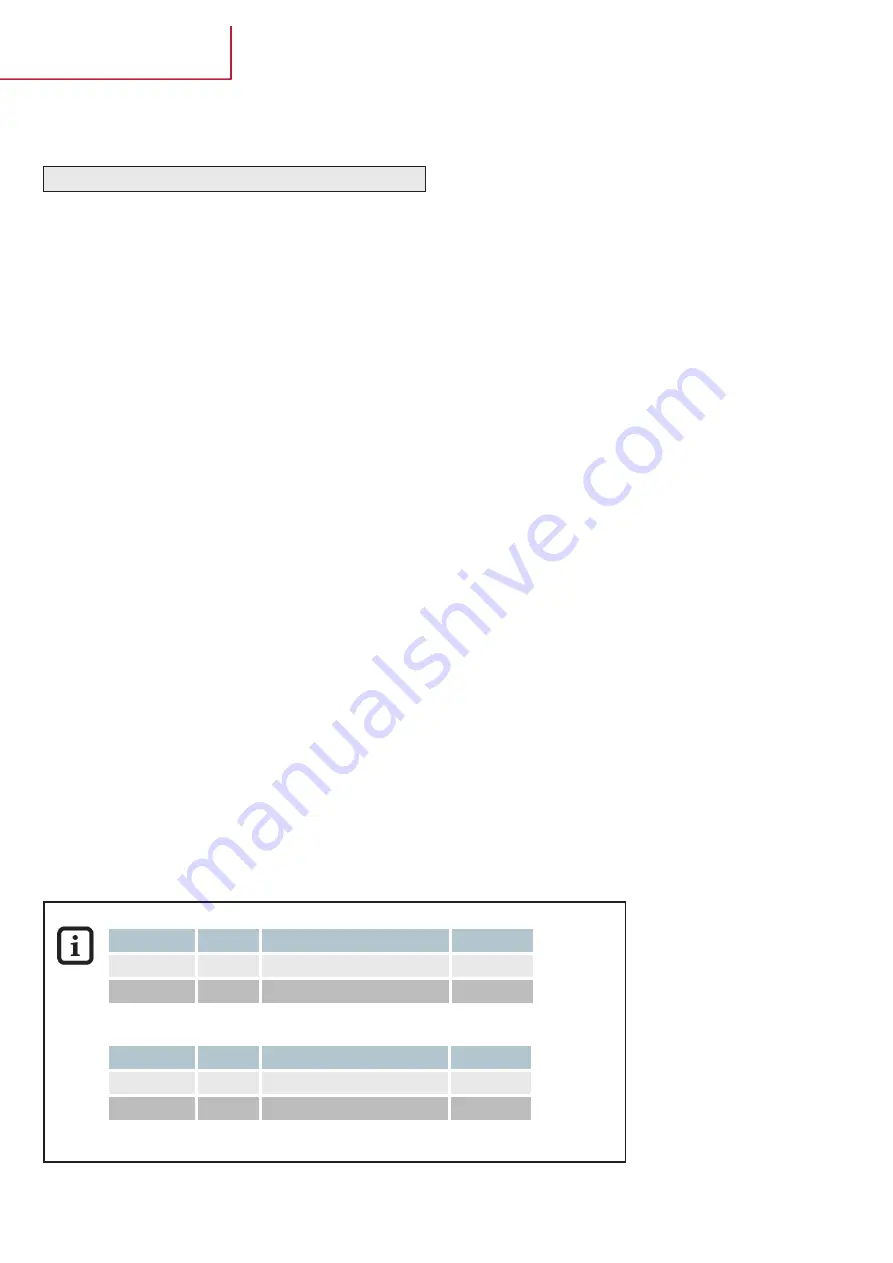
Temposonics
®
MH Digital
Operating Manual
I
20
I
10.3 Setting the operating parameters
CANopen & CANopen Safety
At system start-up (power-on, reset), the sensor saves the operating parameters stored in the EEPROM. When switching on, these are the fac-
tory-set parameters, or the data which has already been changed and saved. Changes are made e.g. via SDOs when the pre-operational mode is
activated. The identifiers are set to the corresponding default value and saved automatically by programming the node ID. Subsequent revision
is possible.
These operating parameters of the Temposonics
®
MH series are stored in the object directory of the sensor.
It serves as a basis for realization of the internal characteristics and functions and of the external communication. For this purpose, the object
directory is divided into „Communication Profile“ and „Device Profile“.
Communication Profile
The Communication Profile contains the parameters decisive for communication, such as identifier settings, PDO configuration, etc. The sensor
includes the encoder communication profile (Device Profile for Encoder – DS406 Vers. 3.1). The advantage: Devices supplied by various manu-
facturers can be connected in a network and replaced very easily, because all units with the same communication profile have mostly identical
parameters.
PDO-Übertragungsart (Transmission Type)
By default, the PDO transmission type is set to asynchronous, i.e.
the sensor transmits its process data independently according to the
preset cycle time. However, the PDO transmission type can also be
set for transmission of process data only after reception of a SYNC
message.
Device Profile
Parameters which are important for sensor operation, e.g. position and speed resolution or cycle time are stored in the Device Profile. In this
context, note that some operating parameters are important:
Resolution
After delivery, the sensor resolution is 100 µm. As standard, the reso-
lution of the motion speed is set to 1mm/s.
For detailed information, see the programming instructions.
Set the cycle time with following commands (e.g. 10, Node-ID = 127*)
Data source
COB-ID
Data
Destination
Controller
0x6
7f*
22; 00; 62; 00; 0A; 00; 00; 00
Sensor
Sensor
0x5
ff*
60; 00; 62; 00; 00; 00; 00; 00
Controller
Save cylcle time: The command ,save parameters’ must be executed.
Data source
COB-ID
Data
Destination
Controller
0x6
7f*
22; 10; 10; 01; 73; 61; 76; 65
Sensor
Sensor
0x7
ff*
60; 10; 10; 01; 00; 00; 00; 00
Controller
Hint:
The answer of the sensor can last up to 600 ms.
For a detailed list of additional operating parameters and the possible settings, please refer to the programming instructions in section
„Object Dictionary“.
PDO Objekt-Mapping
The sensor doesn‘t support dynamic mapping.
The preset mapping parameters cannot be changed.
PDO1 transmits the position and speed.
Error Messages
The position sensor sends emergency objects automatically as soon
as there are errors.
Cycle Time
The cycle time defines the transmission period for the asynchronous
PDO. Values between 1 and 65535 ms can be selected.
A cyclic transmission of the position value is set, when the cyclic
timer is programmed > 0. Changing the cycle time (Object 6200)
cause a direct change of the PDO1 event timer. (see DS406 V3.0) Set-
ting the cycle time shall match the configuration of the CAN network.
A short cycle time, slow Baud rate and too many network users may
lead to a bus overload.
CANopen