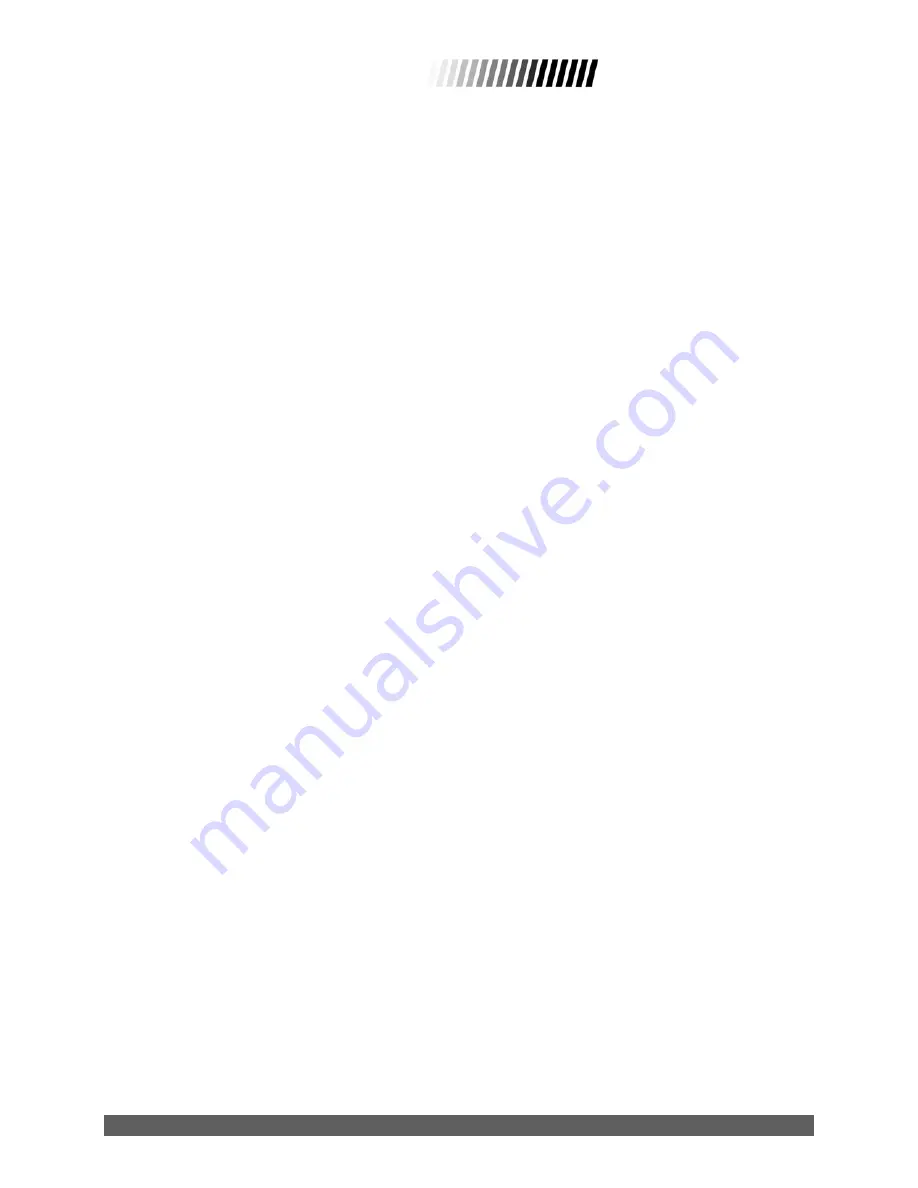
UltraMig 175
- 13 -
3. Aluminium welding
A. Aluminum welding with a standard torch normally
requires the installation of a teflon liner in a size to
match the gun and cable assembly.
B. Reduce the tension on the upper drive wheel.
There should be just enough drag to feed the torch
without damage to the aluminum wire (see fig.).
C. Use only 100% argon inert gas with 14 to 18 l/min
flow rate.
D. Always "PUSH" the weld bead with aluminum to
keep the gas "IN FRONT" of the welding. The argon
will provide the inert shield for a clean weld. E) Use a
stainless steel brush to clean the aluminum before the
welding.
F. Begin with a low power setting and gradually
increase it obtain a smooth, even weld.
G. As aluminum is an excellent heat conductor, it will
be necessary to decrease the power after few
centimetres (inches) of welding.
NOTE
: Always use a contact tip one size bigger then
the aluminum welding wire selected.
Ex: for a wire of
0.8mm (.030”), use a contact tip for a wire diameter
of 0.9mm (.035”)
.
4. Spot welding
Spot welding can be done through two thickness of
sheet metal. However, the best results are obtained by
drilling or punching a hole the top piece.
A. In case of spot welding through two pieces of sheet
metal, both pieces should be clean, properly aligned,
and securely clamped together.
B. Install the spot weld nozzle on the torch.
C. Adjust the power to obtain a flat bead. If possible,
test the setting on a sample made with the same
sheets of metal to be spot welded.
D. Hold the torch perpendicular to the work surface
with the two spot nozzle legs touching the metal and
pull the trigger.
E. In case of welding in a pre-drilled hole, center the
spot nozzle above of the hole and fill it up.
F. When working without a pre-drilled hole it will be
necessary to turn up the power high enough to
penetrate the top sheet of steel.
G. When a spot nozzle is not available, use a standard
conical welding nozzle and maintain a distance of
6mm to 12mm between the nozzle and the sheet
metal.
5. Stitch welding
Stitch welding is a convenient process to use when
welding rusty or thin material, and where there is a risk
of deforming or burning through the metal. A stitch
weld actually consists of a series of spot welds strung
together. A short gap between each stitch allows the
piece of steel to cool down.
A. Select a power setting appropriate for the thickness
of the piece of steel.
B. Hold the trigger and move slowly along the welding
line while maintaining the angle to and distance from
the work.
C. The gap between each stitch should be long
enough to allow the orange color of the preceding weld
to disappear.
A build in “post” gas flow of 1 sec. keeps the gas valve
open after the arc stops providing better cooling before
the next weld.
6. Filling holes
A. Throughly clean the edges of the hole.
B. Make a short weld at one spot on the edge of the
hole and let cool.
C. Make another short weld on each side of the first
weld and let them cool.
D. Make two longer welds overlapping the first three
with an arching movement of the torch. Again, allow
the welds to cool.
E. Repeat the same technique on the other side of the
hole and across the top of the hole, if necessary.
F. Long, narrow gaps may also be easily filed and
closed by using the stitch welding mode.
Содержание UltraMig 175
Страница 16: ...UltraMig 175 16 Exploded views UltraMig 175 ...
Страница 17: ...UltraMig 175 17 ...
Страница 19: ...UltraMig 175 19 Exploded view Torch MB14 ...