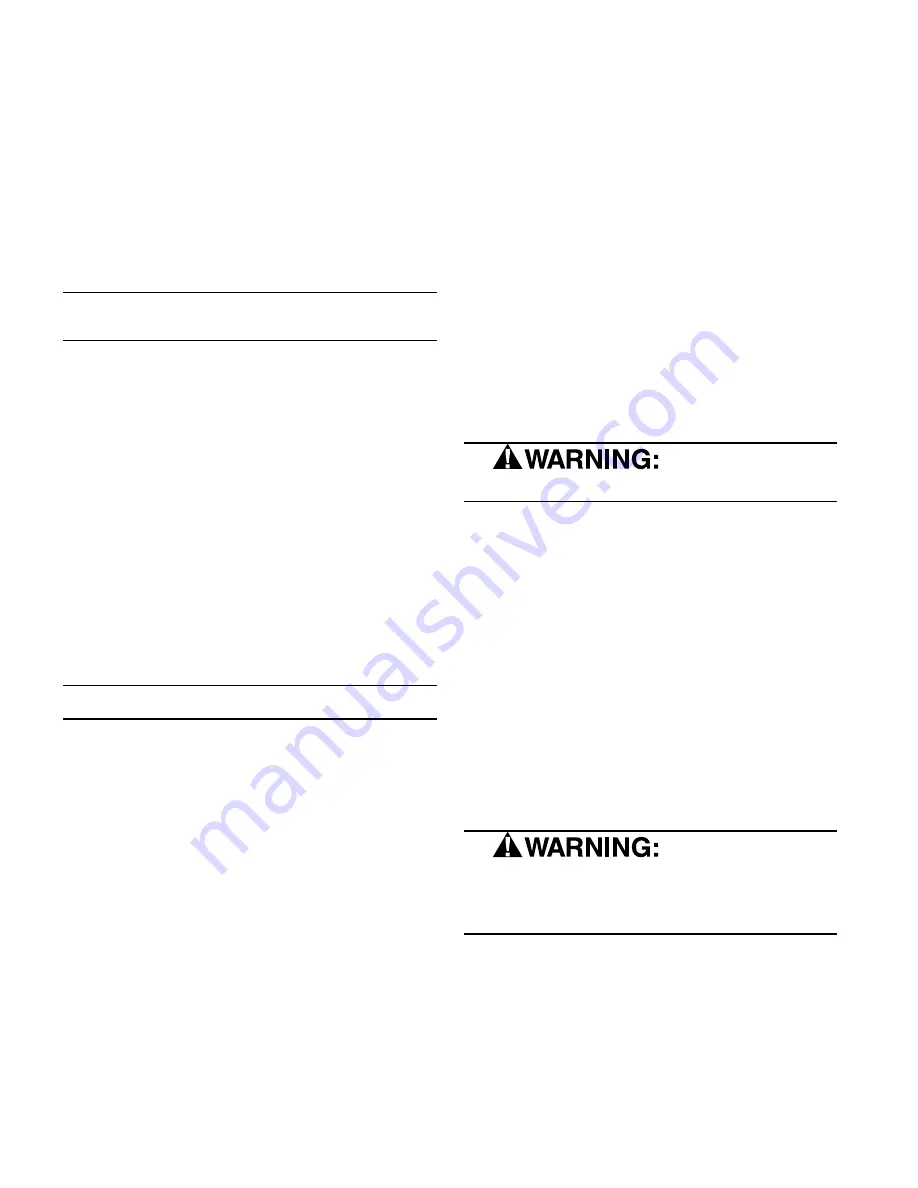
11
4. Reconnect the sensor and re-ignite the burner. Once the
burner is ignited, simulate a high temperature failure by dis-
connecting a wire from the sensor TC01. The gas valve
should close and stop the flaem, re-connect TC01. The ig-
nition sequence will be initiated. The burner should re-light
after about 45 seconds.
5. Once the burner is ignited, simulate overheating by discon-
necting a wire from the sensor TC02. This stops all the
burner's elements (fan and gas valve should no longer be
energized). Reconnect the TC02 wire.
Adaption to available gases (See Table 3)
The gas-fired heating modules built into YK* units are avail-
able in different categories. The units are supplied ready to
operate using natural gases G20 (20 mbar) and G25 (25
mbar) or using gas G31 (37 mbar).
The transition from G20 gas to G25 gas does not require any
action. The available power in G25 gas supply is reduced.
The transition from G20 to G31 gas requires the following
modifications.
- Change of the gas intake orifice in the burner's fan.
- Implementation of pressure limiter.
The orifice and the limiter
for supply with gas G31 must be manufactured by
Trane.
.
Start up
Operating check list before the start-up
- Unit is level, with sufficient clearance all around.
- Duct network is correctly dimensioned according to the unit
configuration, insulated and water tight.
- Condensate drainage line is correctly dimensioned, equipped
with trap and sloped.
- Filters are in position: correct size and quantity, clean.
- Wiring is correctly sized, and connected in accordance with
wiring diagrams.
- Power supply lines are protected by recommended fuses
and correctly earthed.
- Thermostat is correctly wired and positioned unit is checked
for refrigerant charge and leaks.
- Indoor and outdoor fans rotate freely and are fixed on shafts.
- Indoor fan rotation speed is set.
- Access panels and doors are replaced to prevent air entering
and risks of injury.
- Checking of the gas heating section, in accordance with
above precedure.
If any operating checks
must be performed with the unit operating, it is the
technician's responsibility to recognize any possible
hazards and proceed in a safe manner. Failure to do
so could result in severe personal injury or death due
to electrical shock or contact with moving parts.
- Measure the negative pressure downstream of the gas unit.
Connect a flexible hose to the gas unit branch connection
and connect as electronic pressure gauge, or failing this a
U tube.
- Start the burner by modifying the thermostat's set point or by
using the "test mode" terninals on the machines terminal
strip.
- Measure the downstream partial vacuum. It must be between
- (minus) 5 mm and - (minus) 9 mm of water head.
- Check the supply pressure upstream of the gas unit once
more when it is operating to ensure the pressure has not
dropped.
Important note: In the event this measurement is
correct, do not adjust the gas unit setting. It has been
set in the factory.
When the measured partial vacuum is positive (above
atmospheric pressure)
- Remove the paint mark on the brass threaded plug with two
holes drilled in it, located on the gas unit, and unscrew it
(See Figure 6).
- To increase the partial vacuum turn the screw counter-clock-
wise.
- Measure the partial vacuum again while the burner is operat-
ing.
- When the adjustment is finished, seal the brass threaded
plug with paint.
It is highly recommended to check the combustion gases with
a flue gas analyzer. The measured valves must be within the
following ranges:
-Carbon monoxide (CO) less than 50 PPM
-Oxygen (O2) greater than 1.5%
-Carbon dioxide (CO2) less than 11%
Note: If the correct setting cannot be obtained,
contact the Trane technicians.
Checking the correct operation of the burner
After having iginited the burner a few times, it is necessary to
check the proper operation of the burner safeties by following
the following procedure:
1. Close the main gas valve, and then simulate a demand for
heating. The burner must start, and then stop when the
quantity of gas contained in the pipe between the main
valve and the built-in gas unit has run out. To ensure this
takes place, following the drop in supply pressure, the
LPGS cut-out must open and stop all the gas supply chain
components (fans, gas valve, ignition controller). Any at-
tempt to ignite the system again must fail.
2. Open the main gas valve. The pressure switch LPGS
should automatically reset. The burner can now be put
back into operation.
3. Ignite the burner. Once it is burning, simulate a flame failure
by disconnecting a wire of the flame detection sensor
(quick connect). The ignition controller should immediately
stop the burner and close the gas valve.
Содержание YK-IOM-2
Страница 10: ...10 Figure 5 Figure 6 Detail of the Gas Section...
Страница 17: ...17 Figure 11A Zone Sensor Interconnections...
Страница 18: ...18 Figure 11B Conventional Thermostat Interconnections...
Страница 23: ...23...
Страница 24: ...24...