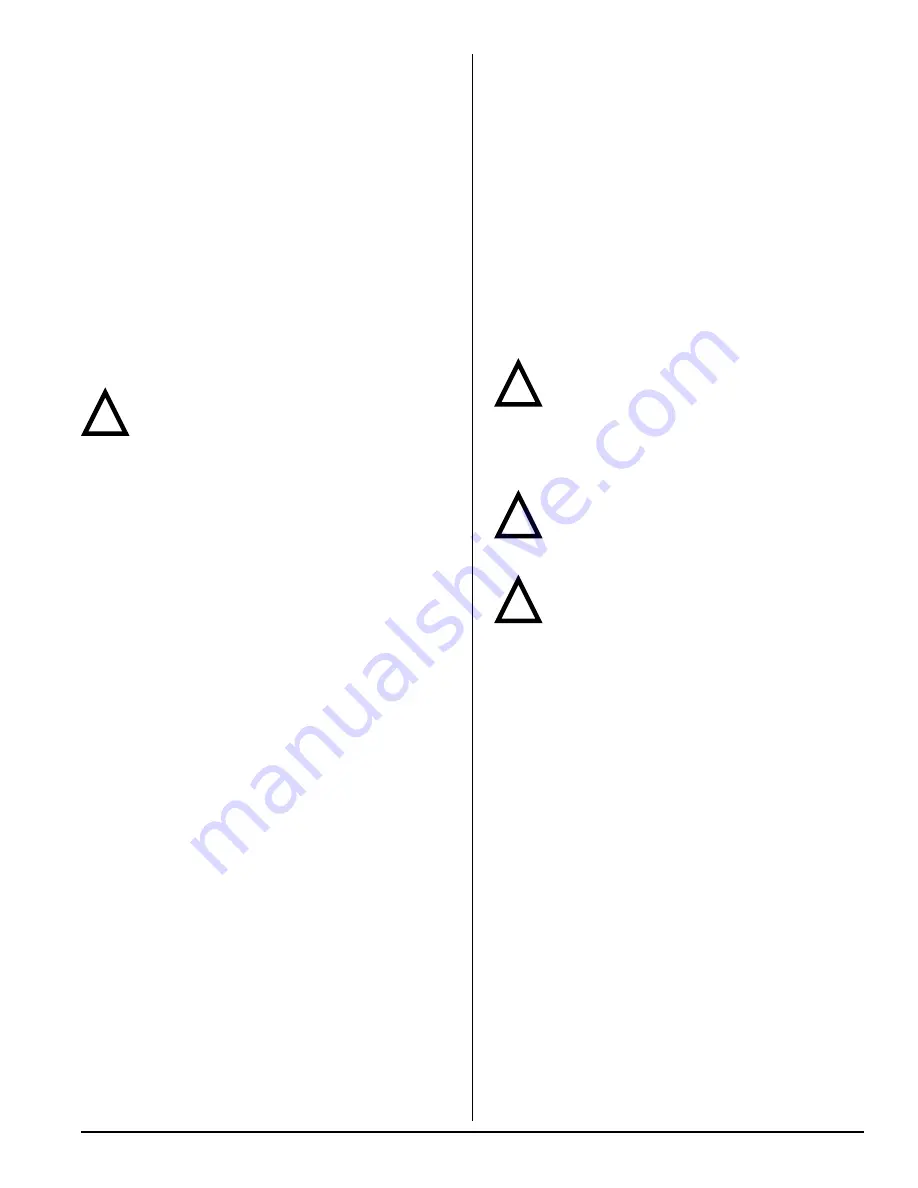
113431 - 10
www.amdry.com
25
!
!
!
Optional Manual Bypass
Provisions are made in the dryer’s fire suppression system
for the installation of an optional manual bypass. The
connections for the manual bypass are made at the “tee” or
“three way” fitting located in the outlet supply side of the water
solenoid valve. The manual ball cock shutoff valve must be
located outside of the dryer at a distance from the dryer where
it is easily accessible. The use and connection of this manual
bypass is at the option or discretion of the owner.
The water connection for the manual bypass is made to the
“tee” or “three way” fitting, which has a 3/8” F.N.P.T. and a
coupling must be used to provide the minimum 1/2-inch (12.7
mm) supply (feed) line.
Electrical Requirements
No independent external power source or supply connection
is necessary. The 24-volt power to operate the fire
suppression system is accomplished internally in the dryer
(from the dryer controls).
Warning
Electrical power must be provided to the dryer at
all times. If the main electrical power supply to the
dryer is disconnected, the fire suppression system is
inoperative!!
Preparation for Operation/Start-Up ___
The following items should be checked before attempting to
operate the dryer:
• Read all “CAUTION,” “WARNING,” and “DIRECTION”
labels attached to the dryer.
• Check incoming supply voltage to be sure that it is the
same as indicated on the data label. In the case of
208 VAC or 240 VAC, the supply voltage must match
the electric service exactly.
• GAS MODELS – Check to ensure that the dryer is
connected to the type of heat/gas indicated on the dryer
data label.
• GAS MODELS – Be sure that all gas shutoff valves are
in the open position.
• Be sure all back panels (guards) and electric box
covers are in place.
• Be sure the service doors are closed and securely in
place.
• Be sure the lint door/drawer is securely in place.
• Rotate the tumbler (drum) by hand to be sure it moves
freely.
• Check bolts, nuts, screws, terminals, and fittings for
tightness and security.
• Check that the vent is connected to the dryer and is
exhausted to the outdoors.
• STEAM MODELS – Check to ensure all steam shutoff
valves are open.
Preoperational Test ___________________
All dryers are thoroughly tested and inspected before leaving
the factory. However, a preoperational test should be
performed before the dryer is publicly used. It is possible
that adjustments have changed in transit or due to marginal
location (installation) conditions.
Turn on electric power to the dryer.
Refer to the Operating Instructions for starting your particular
model dryer.
Gas Dryers
Open all shutoff valves.
When a gas dryer is first started (during initial start-up), it has
a tendency not to ignite on the first ignition attempt. This is
because the gas supply piping is filled with air, so it may take
a few minutes for the air to be purged from the lines.
Note
During the purging period, check to be sure that all
gas shutoff valves are open.
A gas pressure test should be taken at the gas valve pressure
tap of each dryer to ensure that the water column pressure is
correct and consistent.
Note
Water column pressure requirements (measured
at the pressure tap of the gas valve body) must be
verified.
Important
In most cases there is no regulator provided in an
L.P. dryer. The water column pressure must be
regulated at the source (L.P. tank), or an external regulator
must be added to each dryer.
Electrical Dryers
Check to ensure that electric oven/contactor assembly is
activating.
Safety Related Circuits
Make a complete operational check of all safety related
circuits:
• Door Switch(es)
• Hi-Limit Thermostats
• Sail Switch
Make a complete operational check of all operating controls.
Tumbler Coating
The tumbler is treated with a protective coating. We suggest
dampening old garments or cloth material with a solution of
water and nonflammable mild detergent and tumbling them
in the tumbler to remove this coating.
Microprocessor Programs/Selections
Each microprocessor controller (computer) has been
preprogrammed by the factory with the most commonly used
parameter (program) selections. If computer program
changes are required, refer to the computer programming
manual, which was shipped with the dryer.
!
Содержание M31SL
Страница 30: ...ADC Part No 113431 10 06 04 08 10 ...