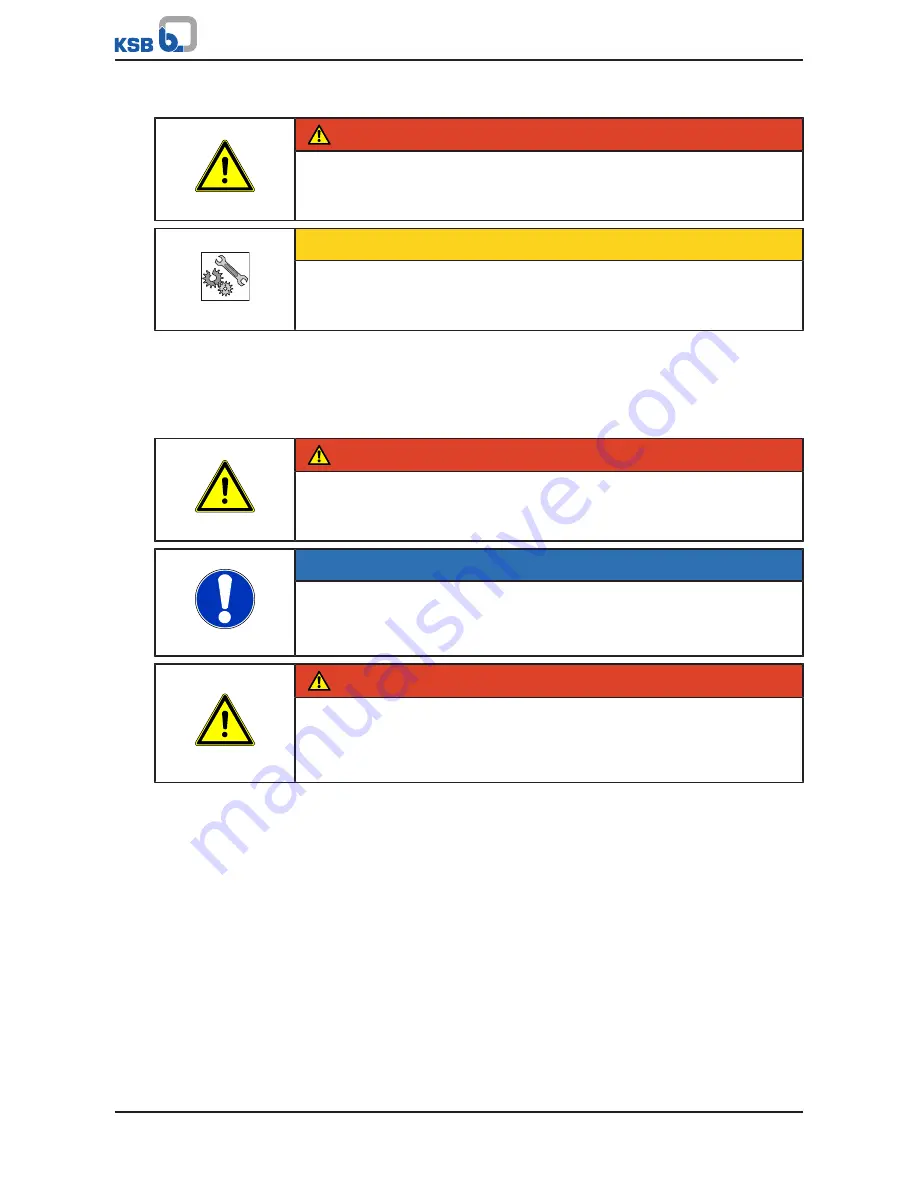
5 Installation at Site
40 of 124
Amarex KRT
5.4.1.2 Level control
DANGER
Pump set running dry
Explosion hazard!
▷
Never allow a nonincendive pump set to run dry.
CAUTION
Fluid level below the specified minimum
Damage to the pump set by cavitation!
▷
Never allow the fluid level to drop below the specified minimum.
Automatic pump set operation in a tank requires the use of level control equipment.
Observe the specified minimum fluid level. (
ð
Section 6.2.4.2, Page 51)
5.4.1.3 Operation on a frequency inverter
The pump set is suitable for operation on a frequency inverter as per IEC 60034-17.
DANGER
Operation outside the permitted frequency range
Explosion hazard!
▷
Never operate an explosion-proof pump set outside the specified range.
NOTE
For pump sets with rated voltages exceeding 500 V, a dv/dt filter should be fitted at
the output of the frequency inverter to reduce the rate of voltage rise to the limits
specified in IEC 60034-17. Otherwise a considerably reduced service life of the
insulation system has to be expected.
DANGER
Incorrect selection and setting of the frequency inverter
Explosion hazard!
▷
Observe the following information on selecting and setting a frequency
inverter.
Selection
When selecting a frequency inverter, check the following details:
▪
Data provided by the manufacturer
▪
Electrical data of the pump set, particularly the nominal current
▪
Only voltage intermediate-circuit inverters (VSI) with pulse width modulation
(PWM) and carrier frequencies between 1 and 16 kHz are suitable.
Setting
Observe the following instructions for setting a frequency inverter:
▪
Set the current limit to max. 1.2 times the rated current. The rated current is
indicated on the name plate.
Start-up
Observe the following instructions for starting up a frequency inverter:
▪
Ensure short start ramps (maximum 5 seconds).
▪
Only start speed-controlled operation after 2 minutes at the earliest.
Pump start-up with long start ramps and low frequency may cause clogging.
Operation
Observe the following limits when operating the pump set on a frequency inverter:
▪
Only utilize up to 95 % of the motor rating P
2
indicated on the name plate.
▪
Frequency range 30 to 60 Hz
Содержание KRT series
Страница 120: ...Index 120 of 124 Amarex KRT W Warnings 7...
Страница 121: ......
Страница 122: ......
Страница 123: ......
Страница 124: ...KSB SE Co KGaA Johann Klein Stra e 9 67227 Frankenthal Germany Tel 49 6233 86 0 www ksb com 2553 8051 04 EN US 01463269...