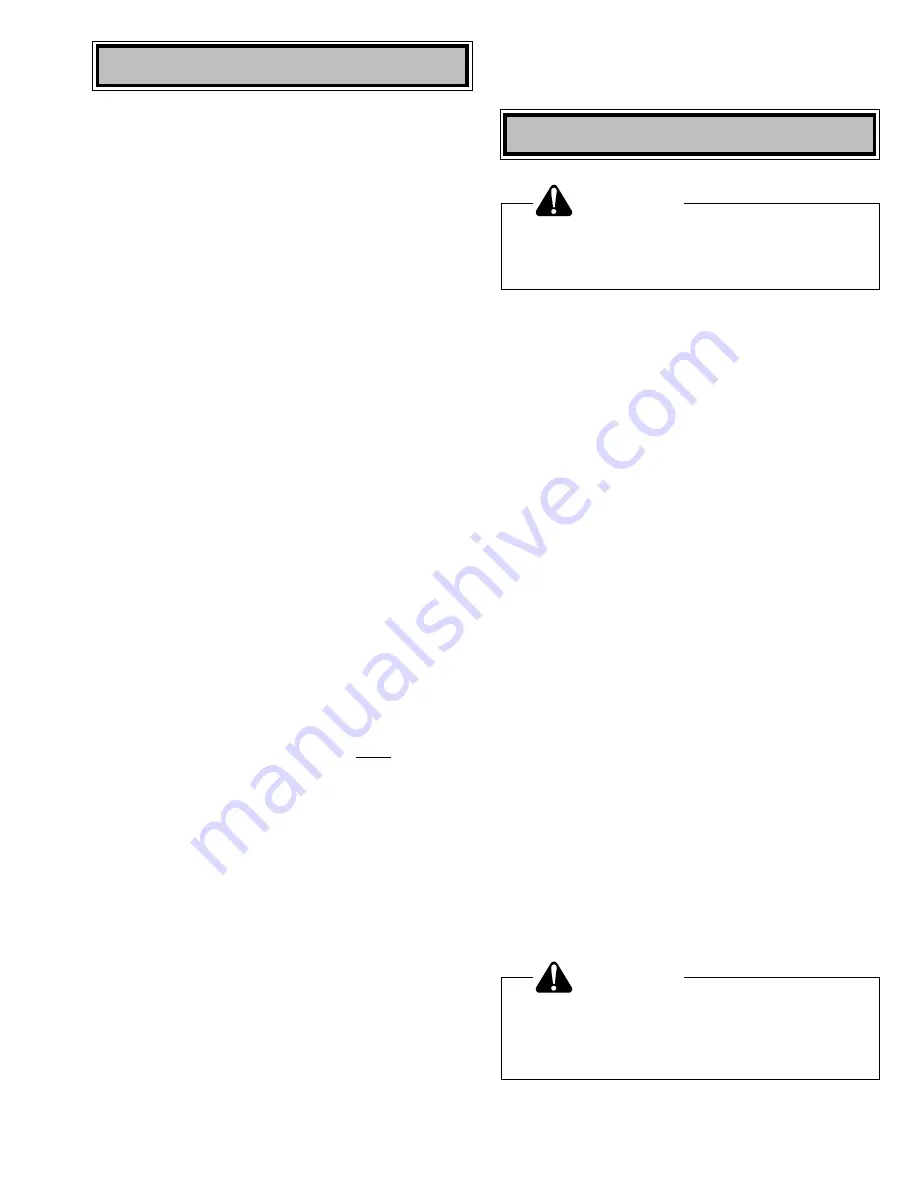
3
Refrigerant Piping
REFRIGERANT LINE SIZING
See unit “Specification Sheet” for required line sizes.
Using smaller vapor lines may decrease performance .
These sizes are suitable for line lengths of fifty feet or less.
It also assumes that the indoor coil will not be more than
forty feet above or below the outdoor unit. Longer runs and
greater lifts are not recommended. If a run of more than
fifty feet is required, contact your Amana distributor for
assistance.
ROUTING OF REFRIGERANT LINES
All of the vapor line must be insulated. The insulation must
include a vapor barrier.
The liquid line must be outside of the vapor line’s insula-
tion.
If part of the liquid line must run through an area that will
be hotter than 120°F, then that portion of the liquid line
must be insulated.
Avoid burying refrigerant lines. If you must bury them, first
dig the trench so that it gradually slopes toward the
compressor (at least 1 inch per 10 feet). Then, insulate the
liquid and suction lines separately. Enclose all under-
ground portions of the refrigerant lines in waterproof
material (conduit or pipe). If the lines must pass under or
through a concrete slab, be sure they are adequately
protected.
Seal the holes where the refrigerant piping enters the
building.
Be careful not to kink or dent the refrigerant lines. Kinked
or dented lines will cause poor performance or compressor
damage.
FILTER DRIER INSTALLATION
1. The filter drier shipped with the unit must be installed
in the liquid line. Warranty may be void if filter dryer is
not installed per these instructions.
2. The filter drier may be installed near the condensing
unit or near the indoor coil.
SWEAT CONNECTIONS AT THE UNIT
1. IMPORTANT: To avoid overheating of the service
valve while brazing, wrap the valve body with a wet
rag, or use a thermal heat trap compound as recom-
mended by the compound manufacturer.
2. The ends of the refrigerant lines must be cut square,
deburred, cleaned, and be round and free from nicks
or dents. Any other condition increases the chance of
a refrigerant leak.
3. After brazing, quench the joints with water or a wet
cloth. This will also help prevent overheating of the
service valve.
SWEAT CONNECTIONS AT THE INDOOR COIL
Check the indoor coil liquid and vapor line diameter. A
bushing or coupling may be needed to match with the line
sizes used. If mix matching to a restrictor orifice indoor coil,
check the “Specification Sheet” for the proper orifice size
to be used with this outdoor unit.
Safe Refrigerant Handling
WARNING
To avoid possible explosion, death, or
injury; practice safe handling of
refrigerants.
While these items will not cover every conceivable situa-
tion, they should serve as a useful guide:
—Refrigerants are heavier than air. They can “push out”
the oxygen in your lungs or in any enclosed space. To
avoid possible death or difficulty in breathing:
—Never sniff a refrigerant.
—Never purge refrigerant into an enclosed room or
space. In fact, all refrigerants must, by law, be
reclaimed.
—If an indoor leak is suspected, thoroughly ventilate
the area before beginning work.
—Liquid refrigerant can be very cold. To avoid possible
frostbite or blindness, avoid contact and wear gloves
and goggles. If liquid refrigerant does contact your
skin or eyes, get medical help immediately.
—Always follow EPA regulations. Never burn refriger-
ant, as poisonous gas will be produced.
—To avoid possible explosion, use refrigerant cylinders
properly:
—If you must heat a cylinder for faster charging, partly
immerse it in warm water. Never apply flame or
steam to the cylinder.
—Store cylinders in a cool, dry place. Never use a
cylinder as a platform or a roller.
—Never add anything other than R-22 to an R-22
cylinder.
—Never fill a cylinder more than 80% full of liquid
refrigerant.
—When removing refrigerant from a system, use only
returnable (not disposable) service cylinders. Check
the cylinder for its pressure rating and hydrostatic
test date. Check the cylinder for any damage which
may lead to a leak or explosion. If in doubt, do not
use the cylinder.
LEAK TESTING
WARNING
To avoid the risk of fire or explosion, never
use oxygen, high pressure air or flammable
gasses for leak testing of a refrigeration
system.
1. Be sure both hand valves on the gauge manifold are
closed relative to the center port (i.e., turned in all the