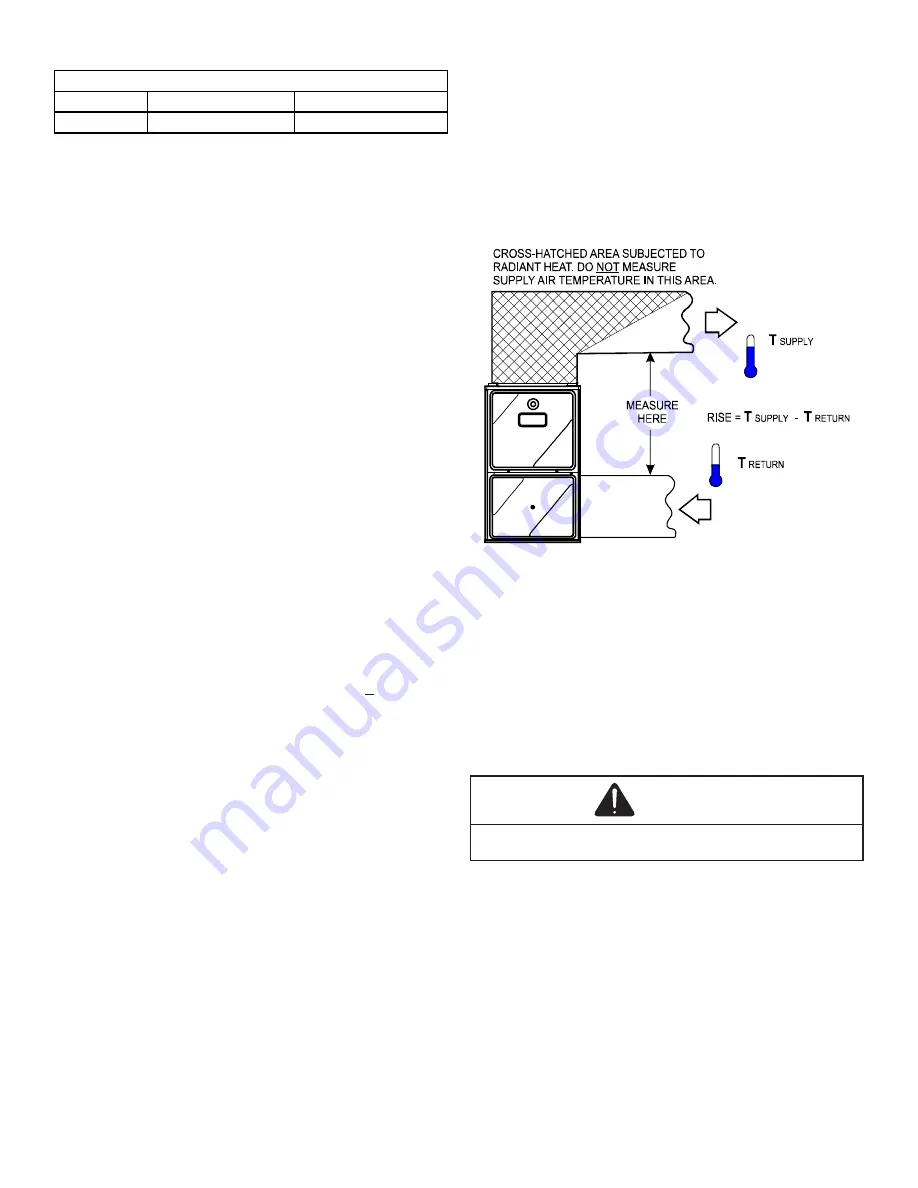
33
Gas Input Rate Measurement (Natural Gas Only)
Natural Gas Minimum: 4.5" w.c. Maximum: 10.0" w.c.
Propane Gas Minimum: 11.0" w.c Maximum: 13.0" w.c.
INLET GAS SUPPLY PRESSURE
The actual gas input rate to the furnace must never be
greater than that specified on the unit rating plate. To
measure natural gas input using the gas meter, use the
following procedure.
1.
Turn OFF the gas supply to all other gas-burning
appliances except the furnace.
2. While the furnace is operating at high fire rate, time
and record one complete revolution of the gas meter
dial measuring the smallest quantity, usually the dial
that indicates 1/2 cu. ft. per revolution. You will use this
number to calculate the quantity of gas in cubic ft. if
the furnace would consume if it ran steadily for one
hour (3600 seconds).
3. If the 1/2 cu. ft. dial was used, multiply your number x 2.
EXAMPLE
: If it took 23 seconds to complete one
revolution of the 1/2 ft. dial (23 x 2 = 46).
This tells us that at this rate, it would take 46 seconds to
consume one cu. ft. of gas. 3600 / 46 = 78.
This tells us that in one hour, the furnace would consume
78 cu. ft. of gas.
The typical value range for 1 cu. ft. of natural gas is around
1000 BTU. Check with your gas utility, if possible. In this
example, the furnace is consuming 78,000 BTUH.
NOTE: The final manifold pressure cannot vary
by more than ± 0.3” w.c. for Natural and
+
0.5” for
LP from the specified setting. Consult your local
gas supplier if additional input rate adjustment is
required.
4. Turn ON gas to and relight all other appliances
turned off in step 1. Be certain that all appliances
are functioning properly and that all pilot burners are
operating.
Temperature Rise
Temperature rise must be within the range specified on the
unit rating plate. An incorrect temperature rise may result
in condensing in or overheating of the heat exchanger.
An airflow and temperature rise table is provided in the
Specification Sheet applicable to your model. Determine
and adjust temperature rise as follows:
1. Operate furnace with burners firing for approximately
ten minutes. Ensure all registers are open and all
duct dampers are in their final (fully or partially open)
position.
2. Place thermometers in the return and supply ducts as
close to the furnace as possible. Thermometers must
not be influenced by radiant heat by being able to
“see” the heat exchanger.
3. Subtract the return air temperature from the supply
air temperature to determine the air temperature rise.
Allow adequate time for thermometer readings to
stabilize.
4. Adjust temperature rise by adjusting the circulator
blower speed. Increase blower speed to reduce
temperature rise. Decrease blower speed to increase
temperature rise. Refer to
Startup Procedure and
Adjustment - Circulator Blower Speeds
for speed
changing details.
SUPPLY
AIR
RETURN
AIR
Temperature Rise Measurement
Figure 45
Circulator Blower Speeds
This furnace is equipped with a multi-speed ECM motor.
The line voltage (115 VAC) power supply to the motor is
constant and not switched by the control board. Motor
operation is also dependent on a pulsing D.C. signal on
one of the four speed taps on the motor. The airflow tables
for heating and cooling speeds show the relationship
between airflow (CFM) and external static pressure for
each size furnace.
WARNING
To avoid personal injury or death due to electrical shock,
turn OFF power to the furnace before changing speed taps.
Circulator Blower Speed Facts
1. Motor speed Tap wiring must remain in factory
position on the control board and motor.
2. There are 4 speed Tap wires to the motor T1, T2, T3,
T4.
3. There are 5 speeds available, depending on DIP
switch settings and found in air flow table for each
size furnace.
4. Heating input (W1/ W2) always has priority over all
other thermostat input.
5. Cooling input (YLo/ Y) has priority over continuous fan
input.
Содержание *MEC96
Страница 59: ...59 THIS PAGE IS LEFT INTENTIONALLY BLANK ...