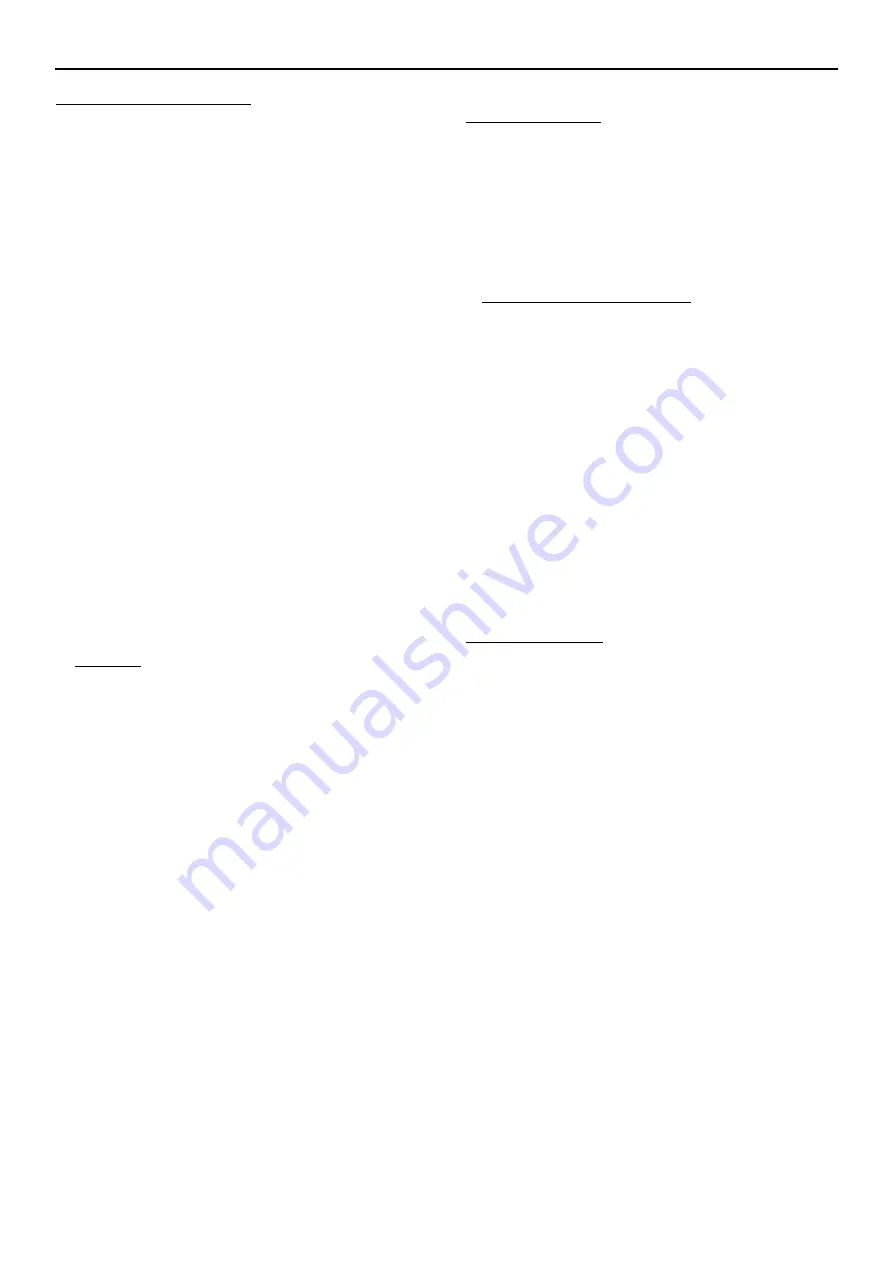
pag. 24
MDE/C133 2561 001
MX3IPG2A
9. SETTING THE UNIT AT WORK
The relay is supplied with factory settings and configurations
as indicated in tables A, B and C (factory settings).
These settings may happen not to match the specific system
where the unit is to be placed. Therefore, the relay settings
must be changed in compliance with the tables D, E and F for
customer’s use, which must be used as a support to develop
a customized setting scheme.
9.1 Safety regulations
During the equipment tests and the start-up, the general safety
regulations applicable to electrical systems must be com-
plied with. Failure to comply with these regulations might
cause harm to the working staff and damage to property. All the
inspections and tests must only be carried out by specially
trained staff.
9.2 Checking nameplate ratings
Inquire whether the equipment ratings are consistent with
those of the system, namely:
- the auxiliary voltage
- the auxiliary voltage of the attachment X2/IPG2A
- the direct rated voltage, the check shall be carried out by
checking the position of the jumper located on the board (see
fig. 4a, 4b, 4c, 4d). warning: any wrong position of the jumper
as to the set values is likely to damage the device.
- the presence of the special jumper S6, see figure 2, if the
communication board is provided and the network is present.
I
WARNING
hazardous voltages may remain in the device even when the
latter has been de-energized or pulled out of its casing
(capacitor's storage)
9.3 Final test with gauging of the attachment X2/IPG2A
Inject auxiliary voltage into the device.
On switching on, after a long time of power failure, the device
can indicate an 'L' type fault (internal clock), a NON-VITAL
FAULT which does not affect the remaining functions: by
updating DATE and TIME, the normal service conditions are
restored.
If the system is running and the relay settings are unknown, the
unit must be inhibited from operating before feeding it with
voltage by pressing the “settings change” key (see § 4.14 and
6.1.13 clause 2) to avoid troubles.
Select the rated frequency of the system on the device, set the
rated current and the rated direct voltage.
Load the settings and configure the relays, the LED’s and the
digital inputs as per the design plans.
Since the unit is equipped with a self-monitoring system, all
hardware and software failures possibly occurring are auto-
matically detected; this makes it useless to test the thresholds
for accuracy, which can however be tested by making refer-
ence to the tolerances specified on the catalogue.
The following tests are however recommended:
Power supply unit test
- Check that the burden of the auxiliary voltage circuit falls
within the 5 to 10W range as far as the d.c. supply is
concerned, and within the 10 to 20VA range as far as the a.c.
supply is concerned.
The feeder is protected by a special 5x20 2 A rapid fuse,
class IEC127/II, as regards the unit with 19-100Vcc (or 19-
72Vca) auxiliary voltage, and a 1A fuse as regards the unit
with 64-300Vcc (or 64-275Vca) auxiliary voltage.
Gauging the attachment X2/IPG2A
- connect to one another terminals 9B-10B-12B of the
attachment X2/IPG2A
- inject the (alternating) auxiliary voltage into the attachment
X2/IPG2A
- ensure that the connection between the attachment X2/
IPG2A and the device MX3IPG2A is correct
- enter the main Settings Change mode (see 6.2 - 6.2.2)
-press
ò
until the following message is displayed:
[ CALIBRATION ]
[X2/IPG2A YES >]
-press
ð
, the display unit will show:
[ CONFIRM? ]
[< NO YES >]
-press
ð
- remove the connection among terminals 9B-10B-12B of
the attachment X2/IPG2A
- leave Settings Change
Checking connections
- Connect between rotor winding and mass a resistance
that ranges between 200 and 6500 Ohm in value and check
it matches the values displayed in the MEASUREMENT
menu.
- Inject a direct voltage into the input (terminals 10-9) and
check it matches the values displayed in the MEASURE-
MENT menu.
- Test each output relay through the procedure given in the
TEST MENU paragraph, simultaneously test the related
external circuit.
- Check the wiringof the digital inputs to ensure it matchesthe
provisions of the design plans.
If the relay has not worked correctly or shows VITAL failures,
it must be put out of order and sent back to the factory for repair
or re-gauging.
The presence of a NON-VITAL fault does not cause an ill-timed
operation, but demands an analysis of the fault type to assess
its importance (for instance, a failing end relay should be
replaced with another end relay that is not currently being used
or, else, whose function is not strictly required).
The possibility of exchanging the relays makes it possible to
maintain the protection scheme working during repairs, so
that any faulty relay can be replaced with a new one of the same
type.