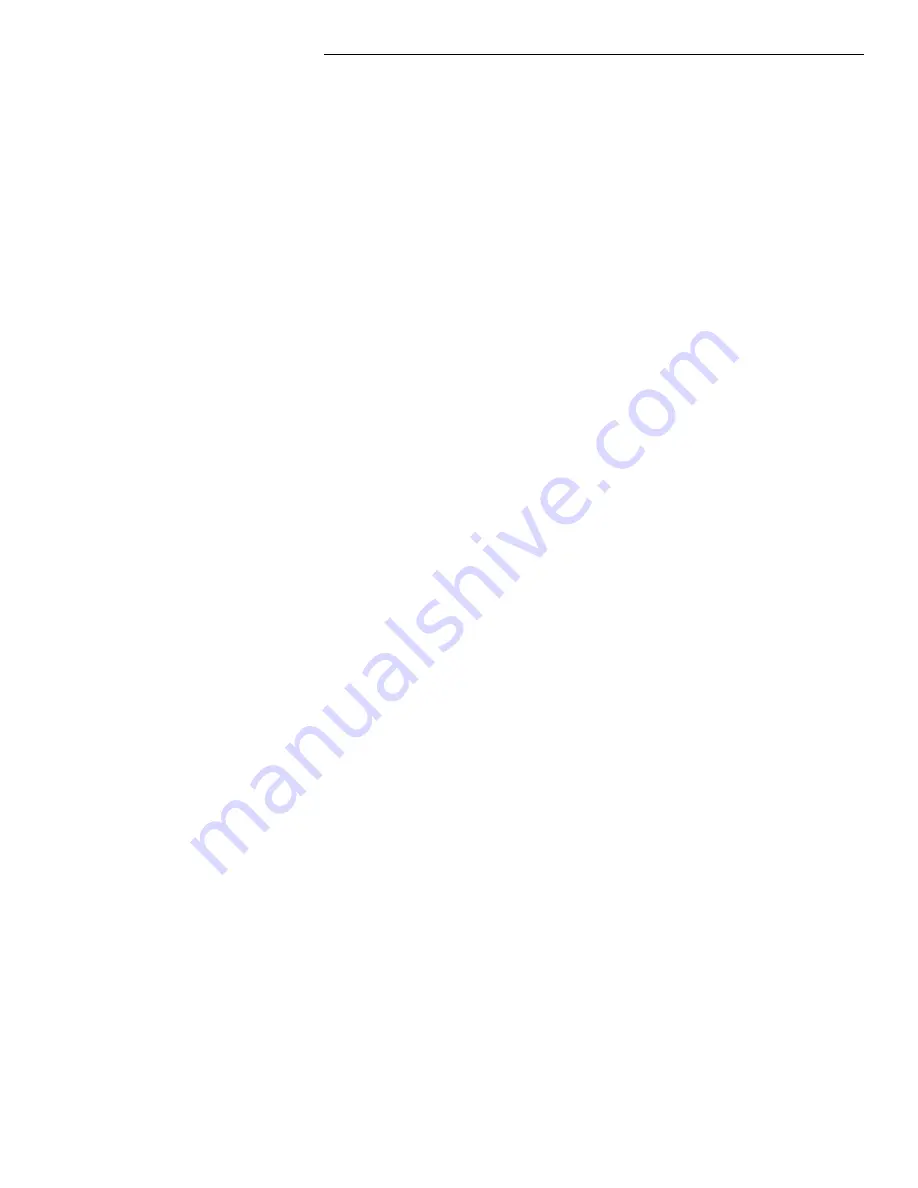
1. INTRODUCTION
1.2
Theory of Operation,
continued
1.2.2
Inverter (STANDBY) Operation
When the incoming AC line voltage drops significantly, or a complete power outage
occurs, the control logic’s line monitor activates STANDBY operation. The battery pow-
ered inverter comes on-line (in-phase with the failing AC line) as the transfer / isolation
relay switches to prevent AC power from back-feeding to the utility. During the brief
transfer from LINE to STANDBY operation, the energy contained in the ferro-resonant
transformer continues to supply power to the load. The following changes occur: The
transfer / isolation relay K101 opens to disconnect the AC line from the primary winding of
ferroresonant transformer T1. The control logic drives the inverter transistors on and off at
line frequency. This switching action converts the DC battery current into AC in the
inverter winding of the ferroresonant transformer which provides regulated power to the
load. The control logic, which includes a circuit to protect the inverter transistors from
over-current damage, monitors the condition of the batteries during inverter operation.
Since a prolonged AC line outage would severely discharge the batteries, resulting in
permanent damage, the control logic disables the inverter when the batteries drop to
approximately 10.5 VDC / battery (31.5 VDC / set).
When AC line voltage returns, the power module transfers back to LINE operation
within 10 to 50 seconds. This delay allows the AC line voltage and frequency to stabilize
before the control logic phase-locks the inverter’s output to the utility input. It then de-
energizes the transfer / isolation relay, re-connects the AC line to the primary of the
ferroresonant transformer and disconnects the batteries from the inverter. This results in a
smooth, in-phase transfer back to utility power without interruption of service to the load.
The battery charging circuit is then activated to recharge the batteries in preparation for the
next power outage.
1.2.3
Charger Operation
The XP Series Uninterruptible Power Supply uses a dual-mode, temperature-compen-
sated battery charger. During AC line operation, a charger / inverter winding on
ferroresonant transformer T1 feeds the charger circuit which provides "float" and "equalize"
charge voltages to the batteries. The circuit consists of a switching regulator, inductor L1
and other associated components. The charger (inverter) winding of transformer T1
produces an AC voltage that is regulated by SCRs Q301, Q302 and filtered by inductor L1.
This produces a regulated DC battery charging voltage. The charge current passes
through R104 to provide current-limit sensing for the charging circuit. Fuse F301, located
on the removable, Main Circuit Module assembly, protects the circuit in the event of
charger malfunction or reversal of the battery leads (Refer to the component layout drawing
at the back of the manual).
The standard control logic provides a constant (programmable) float charge to the
batteries. A switch (CHARGE MODE) SW201 located on the front panel of the power
module allows a technician to manually activate the charger’s equalize mode which has a
1.2 hour duration. With the optional APM or USM logic upgrade installed, the equalize
charging mode becomes an automatic user-programmable function.
When the XM Series module resumes LINE operation, the charger quickly recharges
the batteries. The charge current is determined by the acceptance level of the batteries,
but limited to 10 Amps maximum. As the batteries approach full charge, the charger’s
current tapers off to normal float levels.
The three color-coded LEDs on the XP front panel "CHARGER STATUS" block display
charging modes. When lighted, the LEDs indicate FLOAT (green), EQUALIZE (yellow) and
RECHARGE (red). Recharge represents a charge rate greater than 5 Amps.
3