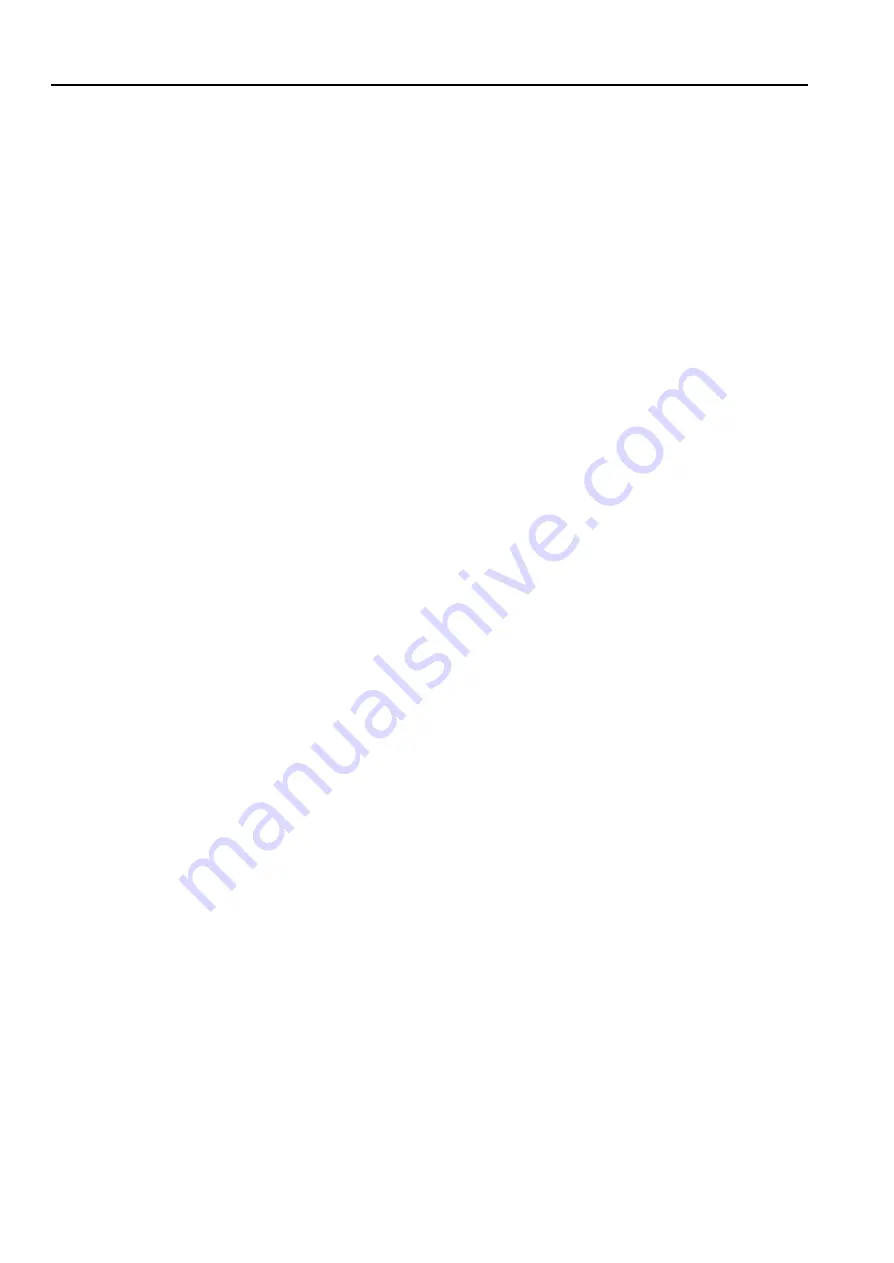
2
2.3
Dangers in case of non-compliance with the safety
hints
Non-compliance with the safety hints may result in dan-
ger not only to persons, but also to environment and
machine. Non-compliance with the safety hints may
lead to the loss of any claims for damages.
In detail, non-compliance may,
for example
, entail the
following dangers:
– Failure of important functions of the machine/plant
– Failure of specified methods for maintenance and
servicing
– Danger to persons by electrical, mechanical and
chemical influences
– Danger to the environment by leakage of dangerous
substances
2.4
Responsible working
The safety hints mentioned in these operating instruc-
tions, the current national rules for the prevention of
accidents as well as any internal working, operating and
safety regulations of the owner must be observed.
2.5
Safety hints for the user/operator
– If hot or cold machine parts lead to dangers, these
parts must be protected against accidental contact
at the site.
– Protection against accidental contact for moving
parts must not be removed when the machine is in
operation.
– Leakages (e.g. of the shaft seal) of dangerous mate-
rials to be handled (e.g. explosive, toxic, hot) must be
discharged so as not to result in danger to persons
and the environment. Legal stipulations are to be
observed.
– Dangers by electrical energy are to be excluded (for
details with regard hereto, please refer e.g. to the
regulations of the VDE and the local energy supply
associations).
2.6
Safety hints for maintenance, inspection and mount-
ing operations
The customer shall see to it that all maintenance, ins-
pection and mounting operations are performed by aut-
horized and qualified expert personnel who have suffi-
ciently informed themselves by thoroughly studying the
operating instructions.
Basically, operations at the machine must be performed
during standstill only. The mode of operation for stop-
ping the machine described in the operating instruc-
tions must by all means be observed.
Pumps or aggregates handling noxious liquids must be
decontaminated.
Immediately upon completion of the operations, all
safety and protective devices must be mounted and
made operational again.
Prior to restarting, the items listed in Section „6.1 Prepa-
ration for Starting“ are to be observed.
2.7
Arbitrary reconstruction and spare parts production
Reconstruction of or changes to the machine are only
admissible after consultation with the manufacturer. Ori-
ginal spare parts and accessories authorized by the
manufacturer serve safety purposes. The use of other
parts may cancel the liability for the consequences
resulting therefrom.
2.8
Inadmissible modes of operation
The operating safety of the machine supplied is only
ensured with due application according to Section 1 –
General – of the operating instructions. The limit values
given in the data sheet must by no means be exceeded.
3.
Transportation and intermediate storage
3.1
Packing
The symbols applied to the packing must be observed.
During transportation and storage, suction side and
auxiliary connections of the pump must be closed with
plugs. During installation of the pump aggregate, the
plugs must be removed.
3.2
Transportation
Due to their weight, eccentric screw pumps and all
pump aggregates are transported to the place of instal-
lation by means of a lifting appliance.
The sling ropes must be placed around the pump and/or
the pump aggregate so that when being lifted, they are
in exact balance.
!
Crane installation and the sling ropes must be suffi-
ciently sized. The sling ropes must not be fixed to the
suspension eyes of the motor.
3.3
Preservation and storage of eccentric screw pumps
Please refer to our document VM 2102 GB/...
4.
Description
4.1
Structural design
Self-priming, single or two-stage eccentric screw pump.
Rotor and stator are the conveying elements. Via the
hollow shaft and/or drive shaft and the coupling rod, the
drive torque is transmitted onto the rotor.
Discharge casing, stator and suction cover are held
together by external casing connecting screws (tie
rods).
The shaft sealing or mechanical seal housing are arran-
ged between discharge casing and lantern and/or bea-
ring bracket.
4.1.1
Bearing and lubrication
Coupling rod on both sides with pin joints encapsulated
liquid-tight. Lubrication by joint oil.
Bearing of the drive/hollow shaft is in the reinforced
bearings of the drive and/or in the bearing bracket by
grease-lubricated axial and grooved ball bearings andor
cylindrical roller bearings.
4.1.2
Shaft seal
By uncooled or cooled stuffing box or by uncooled or
cooled, maintenance-free, non-balanced, single or
double-acting mechanical seal.
4.1.3
Dimensions/branch position/flanges
The dimensions of the pump and/or pump aggregate,
the branch position and flange dimensions are to be
taken from the tables of dimensions.
4.2
Mode of operation
Self-priming, rotary positive-displacement pump, the
conveying elements of which are the rotating eccentric
screw (rotor) and the fixed stator. Both meet in the
cross-section at two points each which, regarded over
the length of the conveying elements, form two sealing
lines. The contents of the tight chambers formed as the
rotor rotates are shifted axially and completely contin-
uously from the suction to the discharge side of the
pump. There is no turbulence despite the rotor rotation.
The constant chamber volume excludes squeezing thus
ensuring an extremely gentle low-pulsation delivery.
4.3
Aggregate construction
4.3.1
Drive
By non-explosion-proof or explosion-proof electric mo-
tors, geared motors or variable-speed geared motors.
Other drive variants (e.g. via V-belt) are possible.
Series SLTP, SETP, SNTP, SLTBP, SETBP, SNTBP
ALLWEILER
a