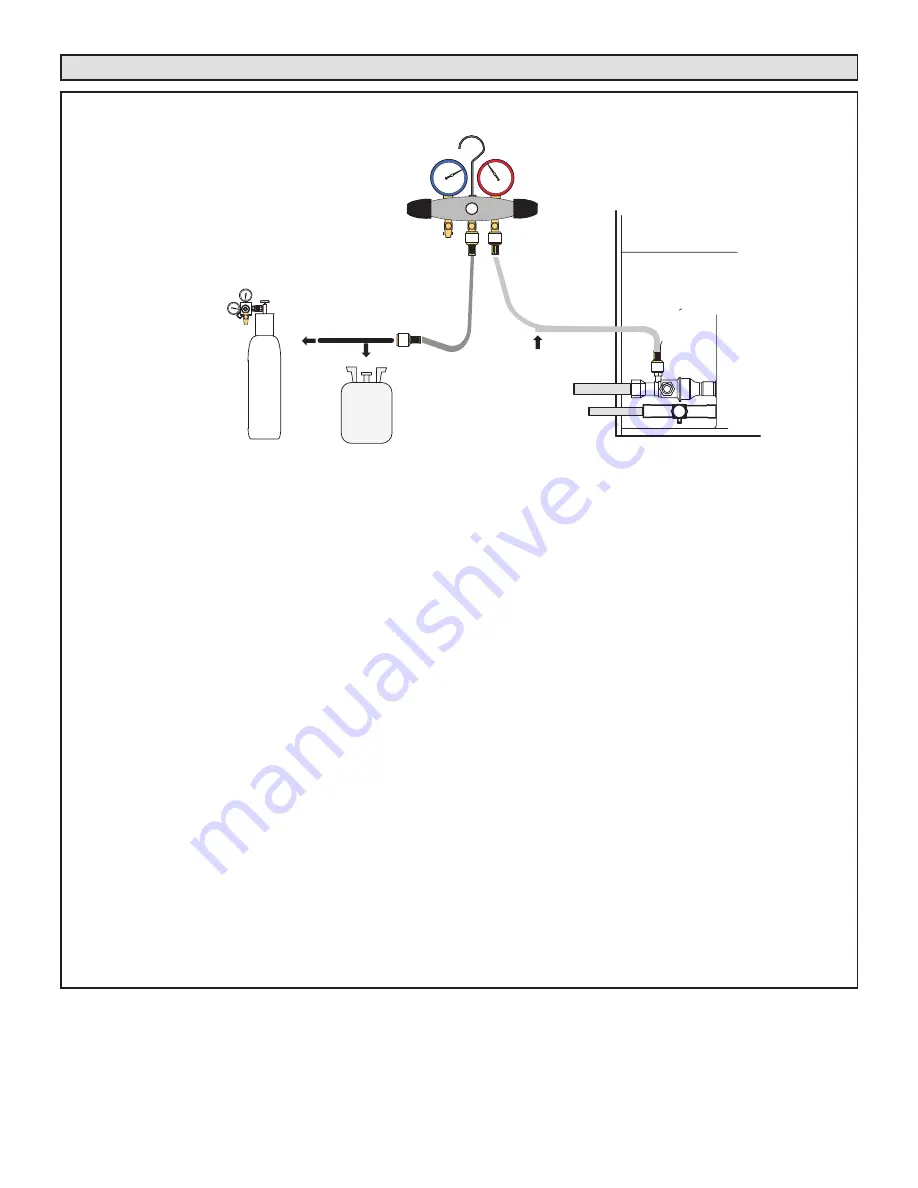
Page 8
STEP 3 – LEAK TEST AND EVACUATION
TO VAPOR
SERVICE VALVE
HFC-410A
MANIFOLD GAUGE SET
OUTDOOR UNIT
HIGH
LOW
1
2
A
B
NITROGEN
NOTE -
Position
canister to deliver
liquid refrigerant.
A -
With both manifold valves closed, connect the cylinder of HFC-410A refrigerant to the center port of the
manifold gauge set. Open the valve on the HFC-410A cylinder (vapor only).
B -
Open the high pressure side of the manifold to allow HFC-410A into the line set and indoor unit. Weigh in
a trace amount of HFC-410A.
[A trace amount is a maximum of two ounces (57 g) refrigerant or three
pounds (31 kPa) pressure.]
Close the valve on the HFC-410A cylinder and the valve on the high
pressure side of the manifold gauge set. Disconnect the HFC-410A cylinder.
C -
Connect a cylinder of nitrogen with a pressure regulating valve to the center port of the manifold gauge
set.
D -
Adjust nitrogen pressure to 150 psig (1034 kPa). Open the valve on the high side of the manifold gauge set
in order to pressurize the line set and the indoor unit.
E -
After a few minutes, open one of the service valve ports and verify that the refrigerant added to the
system earlier is measurable with a leak detector.
F -
After leak testing, disconnect gauges from service ports.
After the line set has been connected to the indoor and outdoor units, check the line set connections and
indoor unit for leaks. Use the following procedure to test for leaks:
A -
Connect the high pressure hose of an HFC-410A manifold gauge set to the vapor valve service port.
NOTE - Normally, the high pressure hose is connected to the liquid line port. However, connecting it
to the vapor port better protects the manifold gauge set from high pressure damage.
B -
With both manifold valves closed, connect the cylinder of HFC-410A refrigerant to the center port of
the manifold gauge set.
CONNECT GAUGE SET
TEST FOR LEAKS
NOTE - Later in the procedure, the HFC-410A container will be replaced by the nitrogen container.
LEAK TEST
FIGURE 8