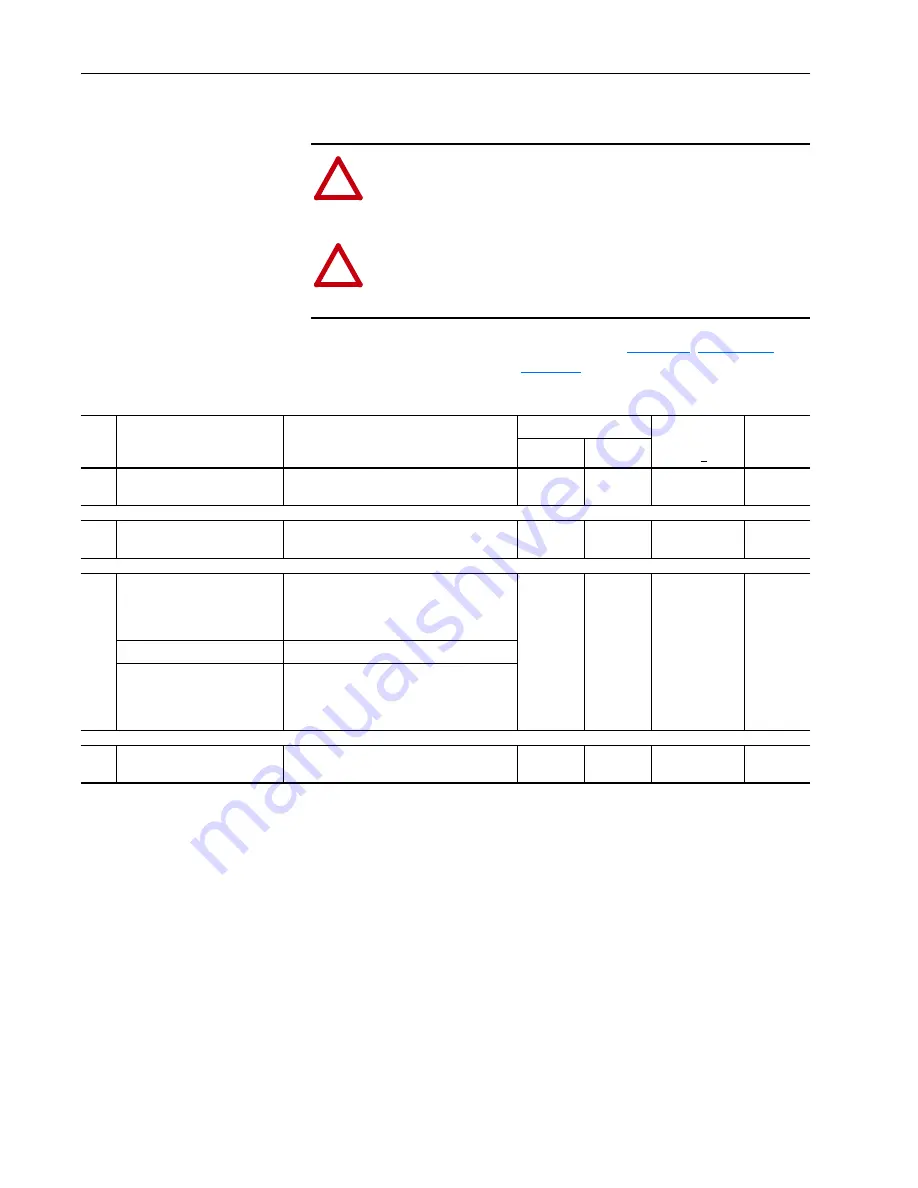
2-18
Frame 2 Installation
PowerFlex 700L Frames 2, 3A, and 3B Liquid-Cooled AC Drives User Manual
Control Wiring
This section provides details on control wiring to the drive.
Connect wiring to terminals in accordance with
Table 2.C
,
Figure 2.16
, and
the Frame 2 drive schematic on
.
Table 2.C Frame 2 Drive Control Wiring Terminal Specifications
!
ATTENTION:
Risk of equipment damage exists. Do not use
drive terminal blocks TB5-1 and TB5-3 to connect any type of
power wiring for auxiliary equipment. These terminals are only
for low amperage control wiring.
!
ATTENTION:
Do not route signal and control wiring with
power wiring in the same conduit. This can cause interference
with drive operation. Failure to observe this precaution can result
in damage to, or destruction of, the equipment.
Item Name
Description
Wire Size Range
(1)
Recommended
Tightening
Torque (+10%)
Wire Strip
Length
Maximum
Minimum
➊
Active Converter Cassette
Terminal Blocks—P1 and P2
Active Converter AC power and control wiring 3.3 mm
2
(#12 AWG)
0.3 mm
2
(#22 AWG)
0.8 N
•
m
(7 lb
•
in)
8 mm
(0.31 in.)
➋
SHLD Terminal
Terminating point for control wiring shields on
the drive
2.1 mm
2
(#14 AWG)
0.3 mm
2
(#22 AWG)
1.4 N
•
m
(12 lb
•
in)
10 mm
(0.39 in.)
➌
Terminal Block—TB1
1b 5: +12/+24V Cooling Loop
1b 6: Cooling Loop Return
Drive control wiring:
Output dry contact (12V DC/24V DC, 2
Amps max.) indicating the drive is
powered and has completed precharge.
4.0 mm
2
(#10 AWG)
0.2 mm
2
(#24 AWG)
0.9 N
•
m
(8 lb
•
in)
8 mm
(0.31 in.)
1b 7: +24V (digin)
Drive-su24V DC
1b 8: Gate Enable
Enables the firing of the IGBTs.
Factory-installed jumper from terminal 1b
7 to terminal 1b 8 allows firing of the
IGBTs.
➍
PS- Terminal
PS+ Terminal
300V DC Auxiliary Control voltage
4.0 mm
2
(#12 AWG)
0.5 mm
2
(#22 AWG)
0.6 N
•
m
(5.3 lb
•
in)
10 mm
(0.39 in.)
(1)
Maximum/minimum sizes that the terminals will accept - these are not recommendations.
Aotewell Ltd
www.aotewell.com
Industry Automation
HongKong|UK|China
+86-755-8660-6182