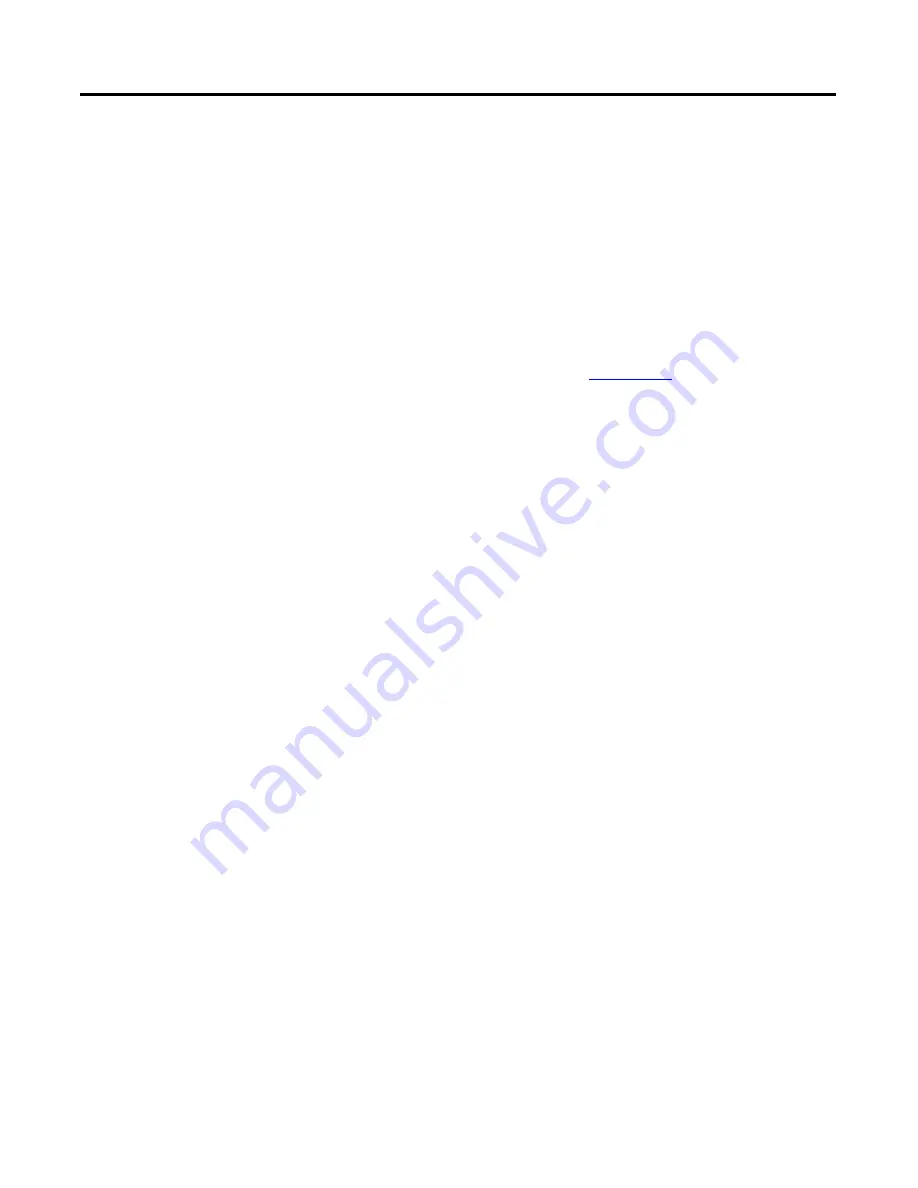
Publication 1794-RM001G-EN-P - December 2011
FLEX I/O Modules
3-7
Using Analog Input
Modules
General Considerations when using Any FLEX I/O Analog Input
Module
There are a number of general application considerations that you must follow
when applying these modules in a SIL2 application:
•
Proof Tests -
Periodically (for example, once every several years) a
System Validation test must be performed. Manually, or automatically,
test inputs to make sure that all inputs are operational. Field signal levels
should be varied over the full operating range to make sure that the
corresponding channel data varies accordingly. For additional
information, refer to publication
.
•
Calibrate Inputs Periodically, As Necessary
: FLEX I/O modules
ship from the factory with a highly accurate level of calibration.
However, because each application is different, users are responsible for
making sure their FLEX I/O modules are properly calibrated for their
specific application.
Users can employ tests in application program logic to determine when
a module requires recalibration. For example, to determine whether an
input module needs to be recalibrated, a user can determine a tolerance
band of accuracy for a specific application. The user can then measure
input values on multiple channels and compare those values to
acceptable values within the tolerance band. Based on the differences in
the comparison, the user could then determine whether recalibration is
necessary.
Calibration (and subsequent recalibration) is
not a safety issue
.
However, we recommend that each analog input be calibrated at least
every 3 years to verify the accuracy of the input signal and avoid
nuisance application shutdowns.
•
Compare Analog Input Data and Annunciate Miscompares
: When
wiring sensors to two inputs channels, the values from those channels
must be compared to each other for concurrence within an acceptable
range for the application before actuating an output. Any miscompare
between the two inputs outside the programmed acceptable range must
be annunciated as a fault.
In Figure 3.7, a user-defined percentage of acceptable deviation (that is,
tolerance) is applied to the configured input range of the analog inputs
(that is, range) and the result is stored (that is, delta). This delta value is
then added to and subtracted from one of the input channels; the results
define an acceptable High and Low limit of deviation. The second input
channel is then compared to these limits to determine if the input are
working properly.
Содержание FlexLogix 1794
Страница 1: ...FLEXI OSystemwithControlLogixforSIL2 Catalog Number Bulletin 1794 Reference Manual AB Drives ...
Страница 18: ...Publication 1794 RM001G EN P December 2011 1 14 SIL Policy Notes ...
Страница 22: ...Publication 1794 RM001G EN P December 2011 2 4 ControlLogix Communications ...
Страница 42: ...Publication 1794 RM001G EN P December 2011 3 20 FLEX I O Modules Notes ...
Страница 44: ...Publication 1794 RM001G EN P December 2011 4 2 General Requirements for Application Software Notes ...
Страница 46: ...Publication 1794 RM001G EN P December 2011 5 2 Technical SIL2 Requirements for the Application Program Notes ...
Страница 56: ...Publication 1794 RM001G EN P December 2011 A 10 Failure Estimates Notes ...
Страница 59: ...AB Drives ...