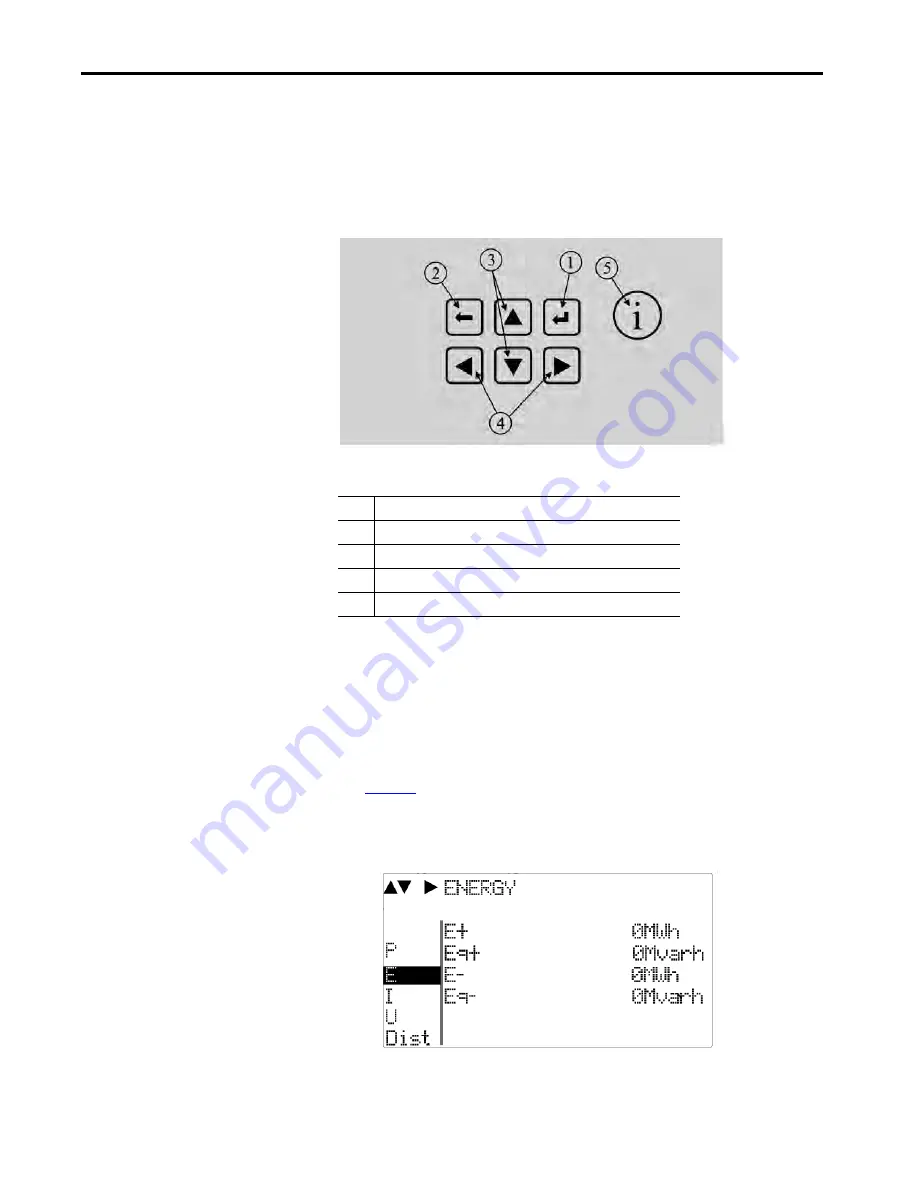
22
Rockwell Automation Publication 857-QS001B-EN-P - April 2017
Chapter 3
Local Panel User Interface
The Keypad
The keypad is used to control objects and switches on the single-line diagram
display. To navigate in the menu, and set the required parameter values, use the
keypad and the guidance that is given in the display.
Figure 5 - Keys on the Keypad
The keypad has these keys and functions:
Menu Navigation and Pointers
Use the up and down arrow keys to move up and down in the main menu
(see
Figure 5
). The active main menu option is indicated with a cursor. The
options in the main menu items are abbreviations, for example Evnt = events.
Figure 6 - Active Menu Options
1
Enter and confirmation key (enter)
2
Cancel key (cancel)
3
Up/Down [Increase/Decrease] arrow keys (up/down)
4
Keys to select submenus [select a digit in a numerical value] (left/right)
5
Additional information key (info)
TIP
The term, which is used for the keys in this manual, is inside the rounded
brackets.
After any selection, the
arrow symbols show the
possible navigating
directions.
The name of the active submenu and a
possible ANSI code of the selected function.
The measured and set
parameters.
The measured and
set values.
Содержание A Series
Страница 4: ...4 Rockwell Automation Publication 857 QS001B EN P April 2017 Table of Contents Notes ...
Страница 12: ...12 Rockwell Automation Publication 857 QS001B EN P April 2017 Chapter 1 Overview Notes ...
Страница 28: ...28 Rockwell Automation Publication 857 QS001B EN P April 2017 Chapter 3 Local Panel User Interface Notes ...
Страница 37: ......