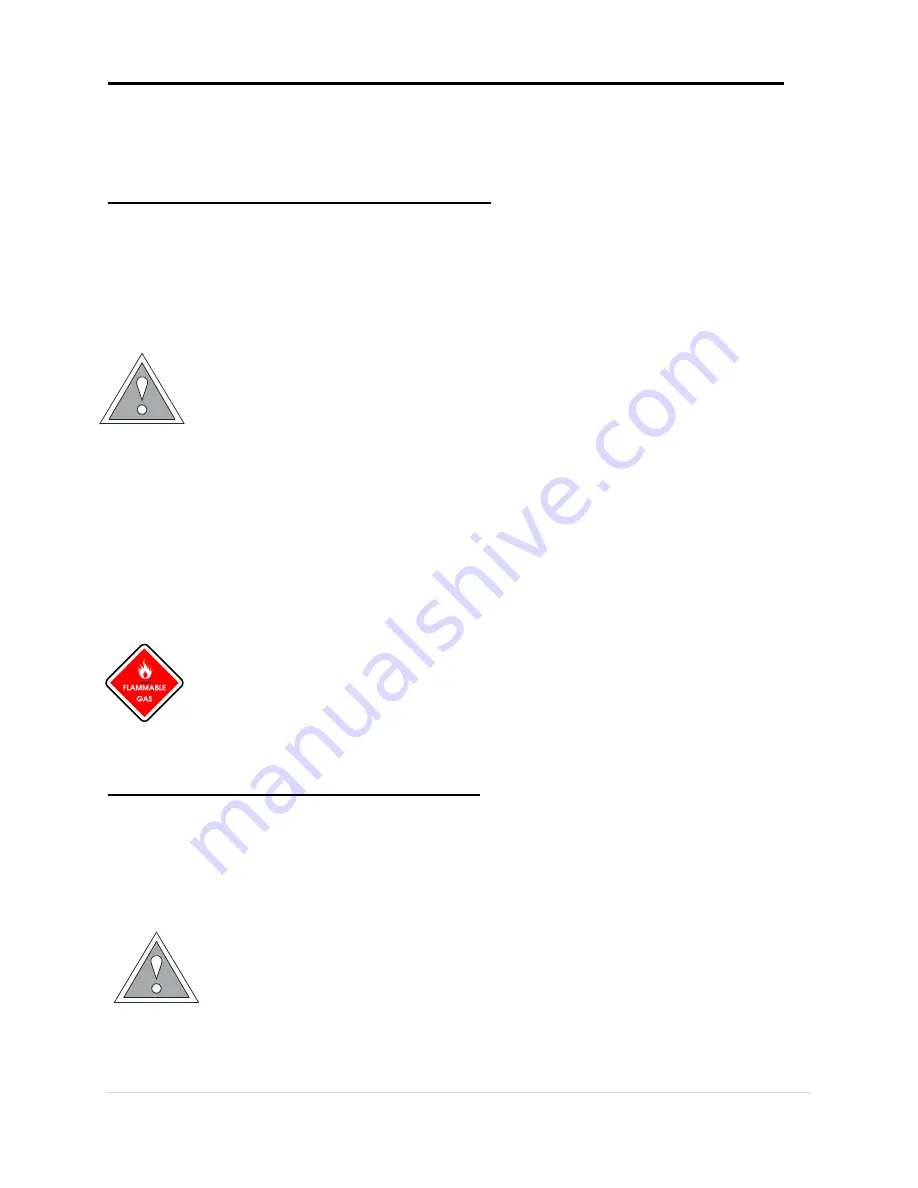
Maintenance/Commissioning
Algas-SDI Operation and Maintenance Manual - SH100-SH200
4-2
STEP 3: Set the high fire fuel flow
If the burner has ignited, drive the main gas control valve to
high fire.
Measure the gas differential pressure.
Adjust fuel control valve until gas differential pressure value
aligns with high fire value in Phoenix SH specification sheet.
NOTE:
The Phoenix SH gas orifice is sized to optimize performance
for 10% excess air at high-fire.
Once chamber pressure and temperature conditions
stabilize, repeat step 3.
Check the gas inlet pressure at the ratio regulator. This
should be at or greater than pressure stated in the Phoenix
SH specification sheet. It should not exceed the maximum
pressure rating of the ratio regulator.
Remove manometer from pressure taps.
Close pressure taps.
DANGER:
Insufficient gas inlet pressure may cause the ratio regulator
to remain full open if there is a loss of air flow to the burner. This can
cause excess fuel operation and the possible accumulations of
unburned fuel in the chamber. In extreme cases, this may cause
explosions or fires.
STEP 4: Set the low fire fuel flow
Drive the main gas control valve to low fire.
Adjust the control valve in provided fuel piping to provide the
desired low fire gas flow.
NOTE:
Measuring low gas pressures at low fire can prove difficult,
and it may be necessary to rely on visual inspection of the flame. This
is especially true when gas turndowns greater than 10:1 are being
used. The main intent is to provide a stable flame with good flame
signal at a firing rate that will not cause the chamber temperature to
overshoot.